EXECUTIVE SUMMARY
ปี 2568-2570 คาดว่าอุตสาหกรรมพลาสติกจะเติบโตได้ต่อเนื่อง ตามการฟื้นตัวของเศรษฐกิจโลกและเศรษฐกิจไทย ช่วยเพิ่มความต้องการใช้พลาสติกของอุตสาหกรรมปลายทาง ผนวกกับนโยบายส่งเสริมการลงทุนในอุตสาหกรรม New S-Curve จากภาครัฐช่วยสนับสนุนอุตสาหกรรมพลาสติกที่อยู่ในห่วงโซ่อุปทาน (Supply Chain) ของอุตสาหกรรมเหล่านี้ อย่างไรก็ตาม อุตสาหกรรมพลาสติกจะเผชิญความท้าทายจากการแข่งขันที่รุนแรงขึ้น และนโยบายด้านสิ่งแวดล้อมที่เข้มงวดทั้งในประเทศและตลาดส่งออก อาทิ มาตรการลดการใช้ผลิตภัณฑ์พลาสติกโดยเฉพาะแบบใช้ครั้งเดียวทิ้ง และการส่งเสริมการใช้พลาสติกที่เป็นมิตรกับสิ่งแวดล้อม ตลอดจนสนธิสัญญาด้านการจัดการพลาสติกโลก (Global Plastic Treaty) ซึ่งอยู่ระหว่างการจัดทำ จะทำให้ห่วงโซ่อุปทานของพลาสติกต้องปรับตัวสู่การลงทุนในสายการผลิตที่ใช้เม็ดพลาสติกรีไซเคิลและพลาสติกจากชีวมวลมากขึ้น จึงอาจทำให้ต้นทุนการผลิตสูงขึ้น กดดันการเติบโตของรายได้และอัตรากำไร
อย่างไรก็ตาม ผู้ประกอบการที่มีธุรกิจครอบคลุมตั้งแต่ต้นน้ำถึงปลายน้ำ และมีการบริหารจัดการสต็อกวัตถุดิบ การขาย และการจัดจำหน่ายได้อย่างมีประสิทธิภาพจะสามารถรักษาอัตรากำไรได้อย่างต่อเนื่อง ขณะที่ผู้ประกอบการรายเล็กจะเผชิญความท้าทายในการปรับตัวมากกว่า
มุมมองวิจัยกรุงศรี
วิจัยกรุงศรีประเมินทิศทางการเติบโตของผู้ประกอบการพลาสติกในปี 2568-2570 ดังนี้
-
บรรจุภัณฑ์พลาสติก: คาดว่าผลประกอบการจะเติบโตได้ต่อเนื่อง โดยผู้ผลิตบรรจุภัณฑ์ชนิดกึ่งแข็งกึ่งอ่อนและชนิดอ่อนจะเติบโตตามอุตสาหกรรมเกี่ยวเนื่องเช่น อาหารและเครื่องดื่ม ภาคการค้าและการค้าออนไลน์ อย่างไรก็ตาม ความต้องการบรรจุภัณฑ์พลาสติกพื้นฐาน (เช่น ถุงหูหิ้ว) จะลดลงบ้างจากกระแสอนุรักษ์สิ่งแวดล้อม โดยผู้ประกอบการที่มีเทคโนโลยีการผลิตทันสมัย มีคุณภาพสูง และสามารถผลิตบรรจุภัณฑ์ได้หลากหลายประเภท จะรักษาระดับการเติบโตได้ในเกณฑ์ดี
-
แผ่นฟิล์มพลาสติก ท่อพลาสติก หลอดและท่ออ่อน คาดว่าจะเติบโตในระดับปกติ ยกเว้นแผ่นฟิล์มพลาสติกและหลอดพลาสติกที่ใช้ในเครื่องดื่มอาจเติบโตชะลอลง จากแผนการจัดการขยะพลาสติกระยะที่ 2 ที่มีมาตรการเข้มข้นขึ้น ขณะที่ธุรกิจโดยรวมจะเผชิญการแข่งขันที่รุนแรง เนื่องจากมีผู้ประกอบการจำนวนมาก ทำให้ลูกค้ามีอำนาจต่อรองด้านราคาระดับหนึ่ง
-
ผลิตภัณฑ์พลาสติกในครัวเรือน: คาดว่าจะเติบโตชะลอลงจากการแข่งขันสูง โดยเฉพาะจากผู้ประกอบการต่างชาติ เช่น จีน ซึ่งมีต้นทุนการผลิตต่ำกว่าผู้ประกอบการไทย จึงมีความเสี่ยงที่อัตรากำไรจะลดลง
-
ชิ้นส่วนพลาสติกและผลิตภัณฑ์พลาสติกอื่นๆ: จะเติบโตตามการขยายตัวของอุตสาหกรรมปลายทาง อาทิ ยานยนต์และชิ้นส่วน เครื่องใช้ไฟฟ้าและอิเล็กทรอนิกส์ และเครื่องมือแพทย์ อย่างไรก็ตาม ความเสี่ยงของธุรกิจมาจากการแข่งขันรุนแรงจากผู้ผลิตต่างชาติ (โดยเฉพาะจีน) ซึ่งมีต้นทุนการผลิตต่ำกว่า อีกทั้งผู้ประกอบการบางรายยังคงพึ่งพาลูกค้ารายใหญ่ที่มีจำนวนจำกัด
ข้อมูลพื้นฐาน
พลาสติกเป็นสารประกอบไฮโดรคาร์บอน ส่วนใหญ่ได้จากการกลั่นน้ำมันดิบหรือแยกก๊าซธรรมชาติ แล้วนำเข้าสู่กระบวนการแยกสลายเพื่อให้ได้สารประกอบขนาดเล็ก อาทิ Ethylene, Propylene, Styrene, Phenol และ Acrylonitrile ซึ่งเป็นสารตั้งต้นในการผลิตเม็ดพลาสติก (Plastic resins) ประเภทต่างๆ ที่มีคุณสมบัติแตกต่างกัน เช่น ความเหนียวและการทนความร้อน ก่อนนำไปหลอมและขึ้นรูปเป็นผลิตภัณฑ์พลาสติก (ภาพที่ 1 และ Box 1) สำหรับใช้ในอุตสาหกรรมต่อเนื่อง ปัจจุบันมีพลาสติกที่ทำจากทรัพยากรหมุนเวียน (Renewable resource) เช่น พลาสติกที่ทำจากกรดโพลีแลกติก (PLA) ที่ได้จากข้าวโพด อ้อย และมันสำปะหลัง ซึ่งสามารถย่อยสลายได้ทางชีวภาพและมีลักษณะการใช้งานเช่นเดียวกับพลาสติกทั่วไป
อุตสาหกรรมพลาสติกของไทยมีมูลค่าตลาดคิดเป็นสัดส่วน 6.7% ของผลิตภัณฑ์มวลรวมในประเทศ (GDP) (ข้อมูลล่าสุดปี 2566) และเป็นอุตสาหกรรมสนับสนุนที่เชื่อมต่อระหว่างอุตสาหกรรมปิโตรเคมี (ผลิตวัตถุดิบเม็ดพลาสติก) กับอุตสาหกรรมต่อเนื่องหลายสาขา (End-use industries) ในลักษณะของผลิตภัณฑ์พลาสติกสำเร็จรูป (Finished products) และกึ่งสำเร็จรูป (Semi-finished products) อาทิ อุตสาหกรรมบรรจุภัณฑ์ ก่อสร้าง ยานยนต์ เครื่องใช้ไฟฟ้าและอิเล็กทรอนิกส์ และเครื่องมือแพทย์
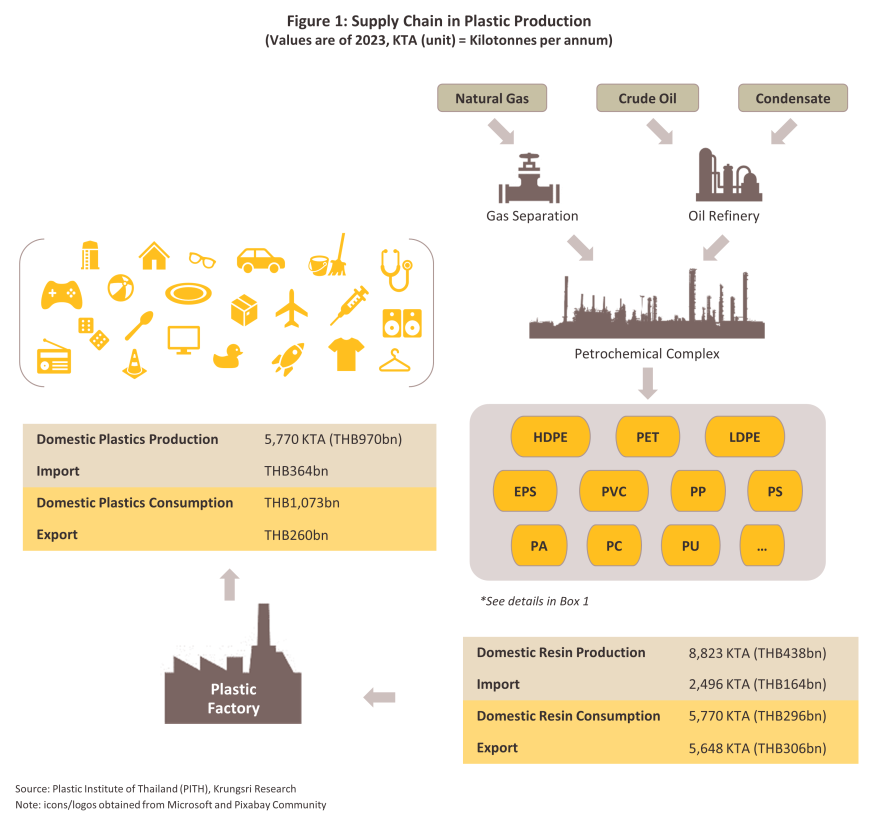
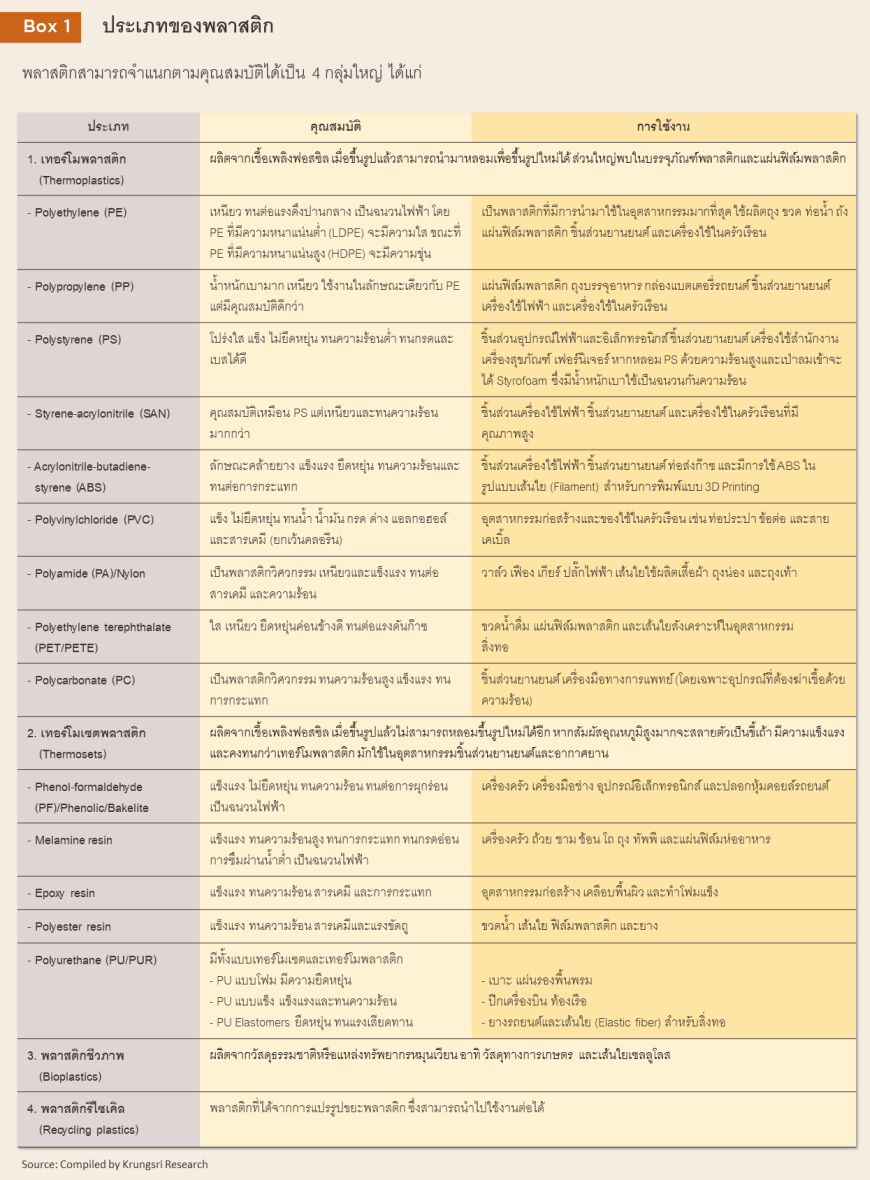
กระบวนการผลิตผลิตภัณฑ์พลาสติกเริ่มต้นจากการหลอมเม็ดพลาสติกด้วยความร้อนในแม่พิมพ์และทำให้เย็นเพื่อให้ได้รูปทรงที่ต้องการ อาจมีการใส่สี (Dyes) และสารเติมแต่ง (Plasticizers) เพื่อเพิ่มคุณสมบัติให้เหมาะสมต่อการใช้งาน เช่น ทนกรด/ด่าง ทนไฟ กันรังสีอัลตราไวโอเลต และเพิ่มความยืดหยุ่น ส่วนการขึ้นรูปพลาสติกทำได้หลายวิธีขึ้นกับวัตถุประสงค์และรูปแบบการใช้งานของผลิตภัณฑ์พลาสติก ประกอบด้วย การเป่าขึ้นรูป (Blow molding) เหมาะกับการผลิตขวดบรรจุภัณฑ์ อาทิ ขวดน้ำ ขวดน้ำมันเครื่อง และขวดแชมพู การฉีดเข้าแม่พิมพ์ (Injection molding) นิยมใช้ในการผลิตชิ้นส่วนอุปกรณ์ อาทิ ชิ้นส่วนอิเล็กทรอนิกส์ ชิ้นส่วนรถยนต์ เครื่องใช้ไฟฟ้า ของใช้ในครัวเรือนและของเล่นเด็ก การอัด (Compression molding) ส่วนใหญ่ใช้กับการผลิตผลิตภัณฑ์ที่ทำจากเมลามินประเภทจาน ชาม ถ้วย และเครื่องครัว และการรีด (Extrusion molding) นิยมใช้ผลิตถุงพลาสติก แผ่นฟิล์มบาง ท่อ PVC ท่อน้ำ และกระสอบพลาสติก โดยผลสำรวจจากสถาบันพลาสติกปี 2566 พบว่าผู้ประกอบการไทยประมาณ 36.5% ผลิตผลิตภัณฑ์พลาสติกด้วยวิธีการฉีดเข้าแม่พิมพ์ รองลงมา คือ การทำฟิล์มและการเป่าขึ้นรูป1/
ด้วยคุณสมบัติทางกายภาพและคุณสมบัติเชิงกลของพลาสติก อาทิ มีน้ำหนักเบา ง่ายต่อการขึ้นรูป สามารถควบคุมการผ่านเข้าออกของก๊าซต่างๆ ป้องกันความชื้นและมีความยืดหยุ่น ทำให้พลาสติกเข้ามามีบทบาทในการเป็นอุตสาหกรรมต้นน้ำสนับสนุนอุตสาหกรรมเฉพาะทางอีกหลายประเภท อาทิ อุตสาหกรรมชิ้นส่วนยานยนต์ใช้พลาสติกช่วยลดน้ำหนักและอัตราการสิ้นเปลืองพลังงาน อุตสาหกรรมวัสดุก่อสร้างใช้ผลิตภัณฑ์พลาสติกเพื่อความคงทนและทนการกัดกร่อนของสารเคมี และอุตสาหกรรมวัสดุอุปกรณ์ทางการแพทย์ที่ใช้พลาสติกช่วยเพิ่มมูลค่า (ภาพที่ 2)
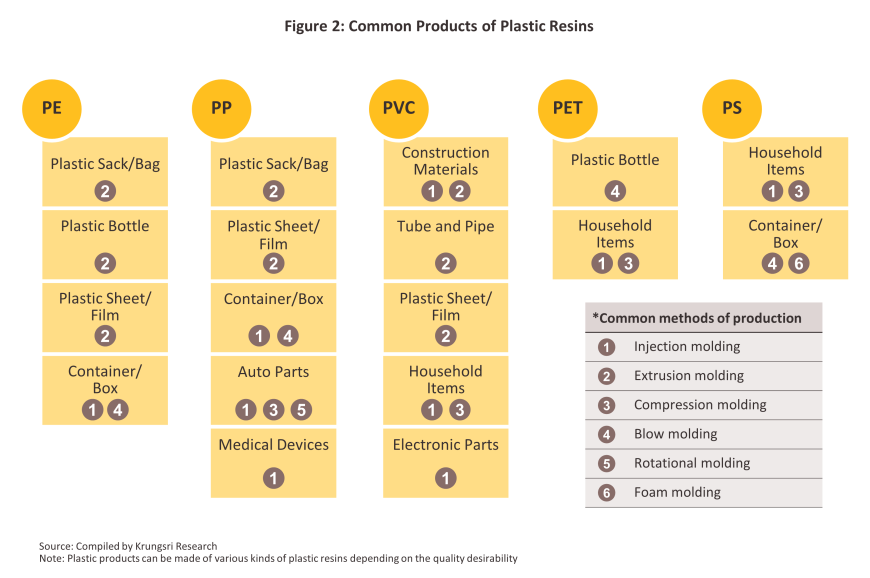
ปี 2566 การผลิตพลาสติกทั่วโลกอยู่ที่ 413.8 ล้านเมตริกตัน เพิ่มขึ้น 3.3% จากปี 25652/ และมีมูลค่าตลาดที่ 712 พันล้านดอลลาร์สหรัฐ โดยทวีปเอเชียเป็นภูมิภาคที่มีการผลิตพลาสติกสูงสุด คิดเป็นสัดส่วนถึง 55.8% ของการผลิตพลาสติกทั่วโลก (ภาพที่ 3) โดยเฉพาะจีนมีสัดส่วนการผลิตสูงถึง 33.3% รองลงมา คือ ภูมิภาคอเมริกาเหนือ (NAFTA) มีสัดส่วนการผลิต 17.1% (นำโดยสหรัฐฯ) และยุโรป 12.3% (นำโดยเยอรมนี) สำหรับความต้องการใช้เม็ดพลาสติกในอุตสาหกรรมต่อเนื่อง พบว่า อุตสาหกรรมการผลิตบรรจุภัณฑ์ใช้เม็ดพลาสติกมากที่สุด คิดเป็น 35% ของเม็ดพลาสติกทั้งหมด รองลงมาคือ อุตสาหกรรมการผลิตสินค้าอุปโภคบริโภค (23%) และอุตสาหกรรมก่อสร้าง (18%) (ภาพที่ 4)

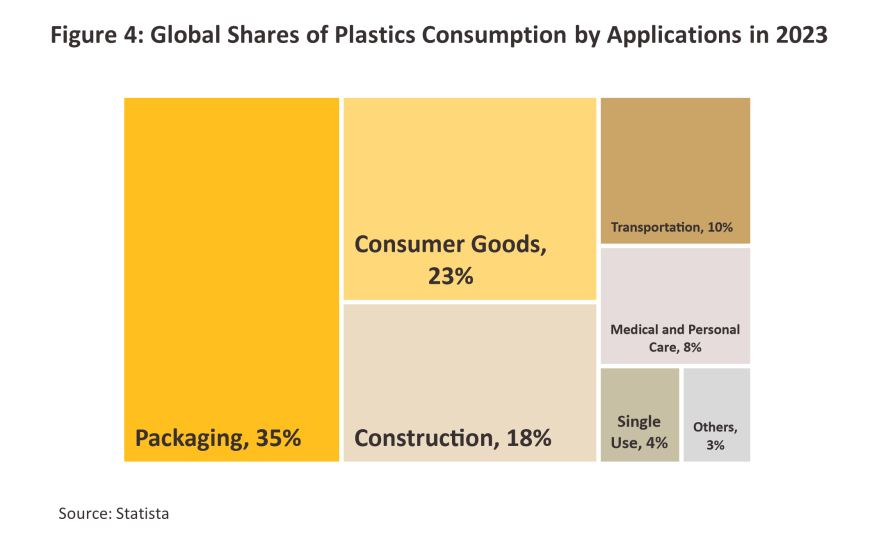
ประเทศไทยเป็นหนึ่งในฐานการผลิตพลาสติกที่สำคัญของโลก มีมูลค่าทางเศรษฐกิจของอุตสาหกรรมโดยรวมอยู่ที่ 1.3 ล้านล้านบาท (ปี 2566) โดยมีจุดแข็งสำคัญจากอุตสาหกรรมปิโตรเคมีของไทยที่มีขนาดใหญ่และมีศักยภาพการผลิตค่อนข้างสูงเมื่อเทียบกับประเทศอื่นๆ ในอาเซียน จึงช่วยเพิ่มจุดแข็งและความสามารถในการแข่งขันให้แก่อุตสาหกรรมเม็ดพลาสติก ซึ่งเป็นผลิตภัณฑ์ปลายน้ำของอุตสาหกรรมปิโตรเคมี อีกทั้งผู้ประกอบการรายใหญ่ของไทยมีความพร้อมในการวิจัยและพัฒนาประสิทธิภาพของเม็ดพลาสติกเพื่อตอบสนองความต้องการของตลาดที่เปลี่ยนแปลงอยู่เสมอ ทำให้ไทยสามารถผลิตเม็ดพลาสติกเพื่อสนับสนุนอุตสาหกรรมต่อเนื่องได้หลากหลายทั้งด้านคุณภาพและราคา โดยปี 2566 ไทยสามารถผลิตเม็ดพลาสติกได้สูงถึง 8.8 ล้านตัน และนำเข้าเพียง 2.4 ล้านตัน โดยเม็ดพลาสติก 49% จะถูกส่งออกไปตลาดต่างประเทศ และ 51% ถูกนำมาแปรรูปเป็นผลิตภัณฑ์สนับสนุนอุตสาหกรรมต่อเนื่องในประเทศ อาทิ ยานยนต์ เครื่องใช้ไฟฟ้าและอิเล็กทรอนิกส์ และก่อสร้าง อุตสาหกรรมการแปรรูปผลิตภัณฑ์พลาสติก (Plastics converter) ของไทยจึงมีห่วงโซ่การผลิตที่ครอบคลุมทั้งวัตถุดิบต้นน้ำ ได้แก่ ผลิตภัณฑ์ก๊าซธรรมชาติในประเทศ อุตสาหกรรมกลางน้ำ ได้แก่ อุตสาหกรรมปิโตรเคมี (ผลิตเม็ดพลาสติก) และอุตสาหกรรมปลายน้ำ ได้แก่ อุตสาหกรรมปลายทางต่างๆ
ผู้ประกอบการอุตสาหกรรมแปรรูปผลิตภัณฑ์พลาสติกในประเทศมีจำนวนมากกว่า 3,217 รายในปี 2566 โดยราว 88.2% เป็นผู้ประกอบการขนาดกลางและเล็ก (SMEs) และ 11.8% เป็นผู้ประกอบการรายใหญ่ เนื่องจากการเข้าสู่ธุรกิจทำได้ไม่ยาก ใช้เงินลงทุนไม่มาก และเทคโนโลยีการแปรรูปฯ ยังอยู่ในระดับพื้นฐานและระดับกลาง ส่วนใหญ่เป็นการผลิตผลิตภัณฑ์พลาสติกที่ใช้งานทั่วไป (Commodity product) ภาวะการแข่งขันของธุรกิจจึงค่อนข้างรุนแรงและมีอัตรากำไรต่อหน่วย (Margin) ไม่สูงนัก ทั้งนี้ ผู้ประกอบการส่วนใหญ่กระจุกตัวในภาคกลาง (76.7% ของจำนวนผู้ประกอบการทั้งหมด) โดยเฉพาะในเขตกรุงเทพฯ และปริมณฑล (รวมสมุทรปราการ และสมุทรสาคร) รองลงมา คือ ภาคตะวันออก (12.2%) และภาคอีสาน (3.6%) (ภาพที่ 5) ผู้ประกอบการเกือบครึ่งอยู่ในอุตสาหกรรมบรรจุภัณฑ์ (45.5% ของผู้ประกอบการทั้งหมด) รองลงมา คือ เครื่องใช้ในครัวเรือน (12.3%) และไฟฟ้าและอิเล็กทรอนิกส์ (8.7%) ตามลำดับ
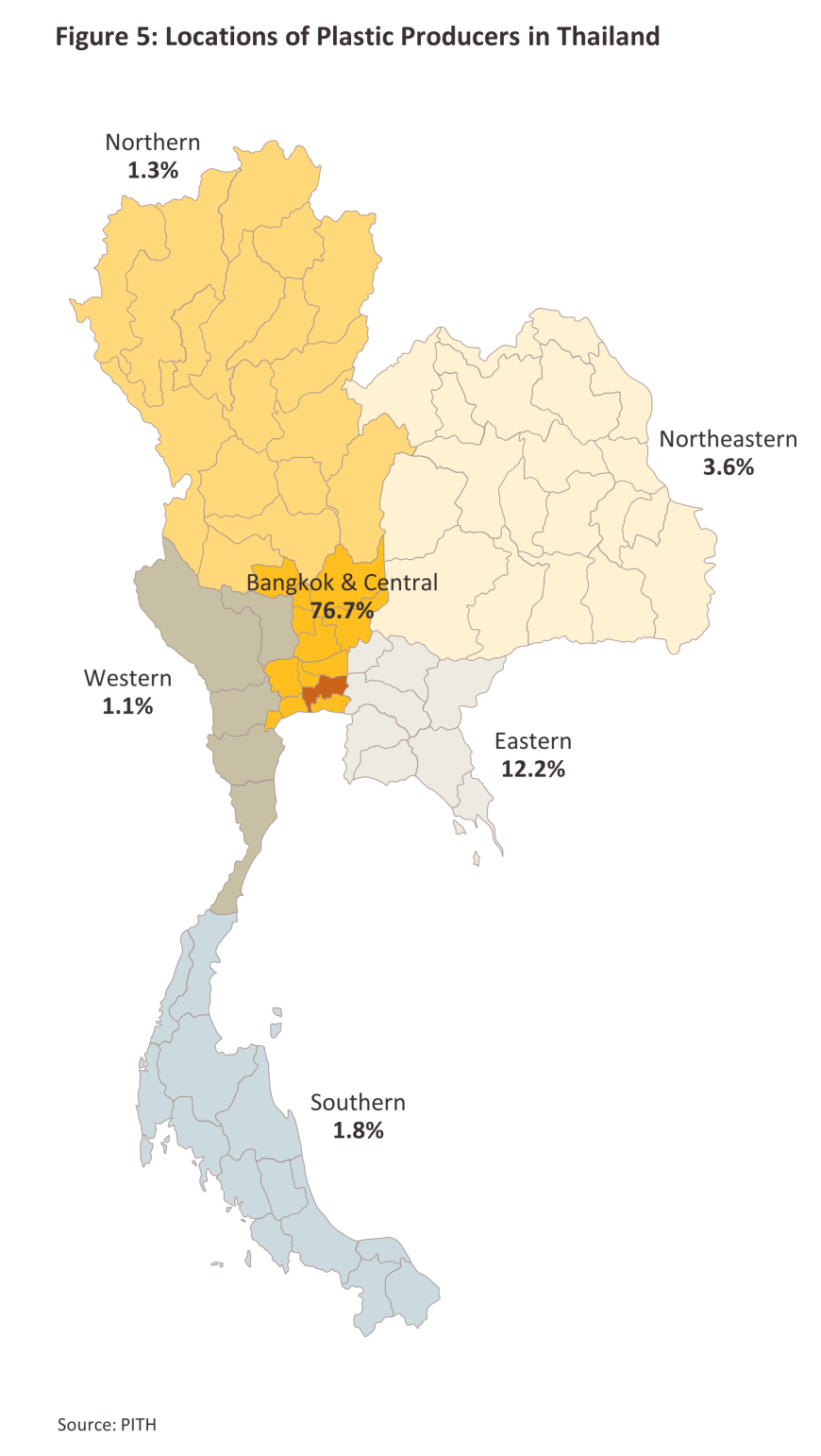
อุตสาหกรรมแปรรูปผลิตภัณฑ์พลาสติกของไทยเน้นผลิตเพื่อสนับสนุนตลาดในประเทศ (ประมาณ 80% ของมูลค่าตลาด) แบ่งเป็น (1) ผลิตภัณฑ์ที่ตอบสนองความต้องการของผู้บริโภคโดยตรง เช่น เครื่องใช้ในครัวเรือน ถุงและหลอดพลาสติก และ (2) ผลิตภัณฑ์เพื่อใช้ในอุตสาหกรรมต่อเนื่อง (End-use industries) โดยเฉพาะ 5 อุตสาหกรรมหลัก ได้แก่ บรรจุภัณฑ์พลาสติก เครื่องใช้ไฟฟ้าและอิเล็กทรอนิกส์ อุปกรณ์ก่อสร้าง ชิ้นส่วนยานยนต์ และเครื่องมือและอุปกรณ์การแพทย์ ที่เหลืออีก 20% เป็นการส่งออกไปตลาดต่างประเทศ ส่วนใหญ่เป็นผลิตภัณฑ์พลาสติกเกรดทั่วไป (Commodity product) ซึ่งมีมูลค่าต่อหน่วยต่ำ อาทิ บรรจุภัณฑ์พลาสติก (มูลค่าส่งออกมีสัดส่วนสูงที่สุด) แผ่นฟิล์มชนิด Non-cellular และ Cellular โดยตลาดส่งออกหลัก ได้แก่ อาเซียน (สัดส่วน 28.5% ของมูลค่าส่งออกผลิตภัณฑ์พลาสติกทั้งหมด) ญี่ปุ่น (18.1%) และสหรัฐฯ (19.0%) ด้านการนำเข้าผลิตภัณฑ์พลาสติก อาทิ บรรจุภัณฑ์ (สัดส่วน 15.7% ของมูลค่านำเข้าผลิตภัณฑ์พลาสติกทั้งหมด) แผ่นฟิล์มชนิด Non-cellular (12.8%) และแผ่นฟิล์มชนิด Self-adhesive (11.2%) แหล่งนำเข้าหลัก ได้แก่ จีน (สัดส่วน 47.7% ของมูลค่านำเข้าทั้งหมด) ญี่ปุ่น (15.2%) และอาเซียน (13.8%) (ภาพที่ 6)
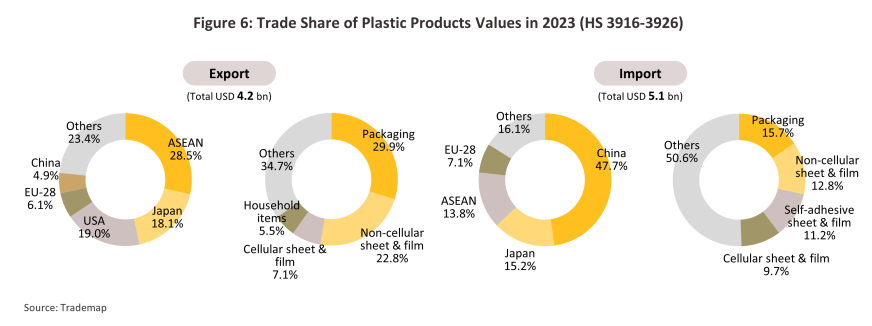
โดยทั่วไป โครงสร้างต้นทุนการผลิตของผลิตภัณฑ์พลาสติกประกอบด้วย วัตถุดิบ (เม็ดพลาสติก) 70% แรงงาน 10-15% พลังงาน 8% และอื่นๆ 7-12% สำหรับบรรจุภัณฑ์พลาสติก (มีมูลค่าการผลิตสูงที่สุด) มีต้นทุนหลัก ได้แก่ เม็ดพลาสติก (สัดส่วน 50-80% ของต้นทุนการผลิตทั้งหมด) ขณะที่ต้นทุนด้านพลังงานและแรงงานจะแตกต่างกันตามประเภทผลิตภัณฑ์และเม็ดพลาสติกที่ใช้ โดยบรรจุภัณฑ์พลาสติกที่ต้องใช้เทคโนโลยีการผลิตขั้นสูงและเครื่องจักรราคาแพง ต้นทุนค่าเสื่อมราคาและอัตราดอกเบี้ยจะมีสัดส่วนค่อนข้างสูง (ภาพที่ 7) สะท้อนว่าการเคลื่อนไหวของราคาน้ำมันดิบและก๊าซธรรมชาติจะส่งผลต่อโครงสร้างต้นทุนของผลิตภัณฑ์พลาสติกและความสามารถในการแข่งขันของอุตสาหกรรม
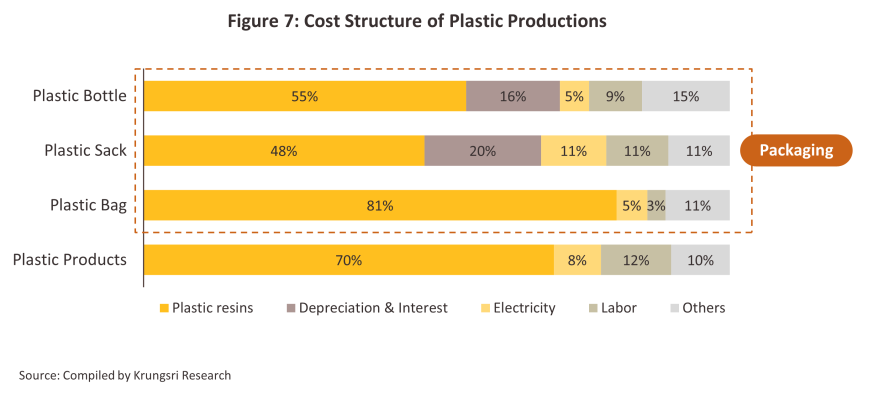
สถานการณ์ที่ผ่านมา
ปี 2567 อุตสาหกรรมพลาสติกของไทยเติบโตในอัตราชะลอตัว ตามภาวะเศรษฐกิจไทยที่ฟื้นตัวช้า (+2.5%) โดยความต้องการบริโภคผลิตภัณฑ์พลาสติกได้อานิสงส์จาก (1) การเติบโตของภาคบริการที่เกี่ยวเนื่องกับภาคท่องเที่ยว อาทิ กลุ่มโรงแรมและภัตตาคาร และการบริการด้านสุขภาพ (2) มาตรการกระตุ้นเศรษฐกิจจากภาครัฐ หนุนความเชื่อมั่นของผู้บริโภคเพิ่มขึ้น อาทิ นโยบาย Free-Visa ส่งผลให้จำนวนนักท่องเที่ยวต่างชาติเพิ่มขึ้น โครงการเงิน 10,000 บาท (เดือนกันยายน) และการเร่งเบิกจ่ายเงินงบประมาณภาครัฐ ช่วยเร่งการขยายตัวของเศรษฐกิจ (3) การขยายตัวของการค้าออนไลน์ โดยพฤติกรรมผู้บริโภคยังนิยมใช้บริการ Food delivery ส่งผลให้มีความต้องการสินค้าในกลุ่มอาหารและเครื่องดื่มต่อเนื่อง รวมถึงการซื้อสินค้าอุปโภคบริโภคที่จำเป็นต่อชีวิตประจำวันที่อุปสงค์ที่ขยายตัว หนุนความต้องการใช้ผลิตภัณฑ์พลาสติกโดยเฉพาะกลุ่มบรรจุภัณฑ์
อย่างไรก็ตาม ความต้องการใช้เม็ดพลาสติกและผลิตภัณฑ์พลาสติกของไทยถูกกดดันจากปัจจัย อาทิ (1) กำลังซื้อในประเทศฟื้นตัวช้าโดยเฉพาะกลุ่มครัวเรือนฐานราก ซึ่งเผชิญปัญหาหนี้ครัวเรือนสูง ทำให้ผู้บริโภคเพิ่มความระมัดระวังการใช้จ่าย โดยชะลอการซื้อสินค้าคงทน เช่น บ้านและยานพาหนะ (2) สินค้าราคาถูกจากจีนหลั่งไหลเข้ามาแข่งขันด้านราคาในประเทศจำนวนมาก (3) กิจกรรมทางเศรษฐกิจทั่วโลกฟื้นตัวช้า รวมถึงจีน ซึ่งเป็นตลาดส่งออกสำคัญของไทย กดดันการฟื้นตัวของอุตสาหกรรมต่อเนื่องของพลาสติก และ (4) กำลังการผลิตใหม่ของโรงงานปิโตร-เคมีที่เพิ่มขึ้นในเอเชียโดยเฉพาะจีน ทำให้มีภาวะอุปทานส่วนเกินของเม็ดพลาสติกบางผลิตภัณฑ์ (เช่น HDPE) มีผลให้ราคาปรับลดลง นอกจากนี้ ยังมีความไม่สงบในตะวันออกกลางซึ่งทำให้ราคาพลังงานผันผวนเป็นระยะกระทบต่อราคาต้นทุนวัตถุดิบ ทั้งยังทำให้การขนส่งสินค้ามีต้นทุนสูงขึ้น (ราคาน้ำมันดิบดูไบทรงตัวสูงที่ระดับเฉลี่ย 80 ดอลลาร์สหรัฐต่อบาร์เรล) (ภาพที่ 8) ปัจจัยข้างต้นนับเป็นข้อจำกัดการเติบโตของอุตสาหกรรม
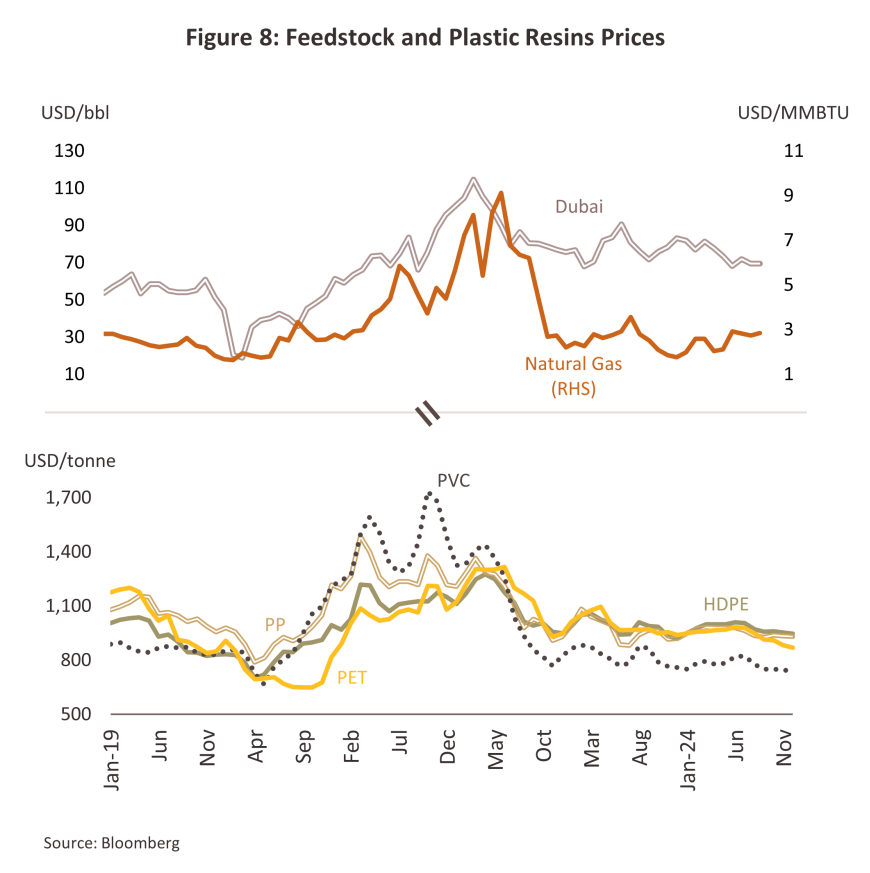
สำหรับสถานการณ์ของอุตสาหกรรมพลาสติกปี 2567 สามารถสรุปได้ดังนี้
-
ดัชนีผลผลิตเม็ดพลาสติกขยายตัวในระดับต่ำที่ 0.4% จากปี 2566 (ภาพที่ 9) แต่ยังคงสูงกว่าการขยายตัวของดัชนีฯ เฉลี่ยของอุตสาหกรรมโดยรวม (MPI) ที่หดตัวเฉลี่ย -1.8% ผลจากการผลิตเม็ดพลาสติกบางประเภท อาทิ Polyethylene terephthalate (PET) ขยายตัว 11.2% จากปี 2566 ตามความต้องการใช้บรรจุภัณฑ์อาหารและเครื่องดื่ม อย่างไรก็ตาม อุตสาหกรรมปลายน้ำของพลาสติกที่ค่อนข้างอ่อนแอ ทำให้ผู้ประกอบการมีการปรับลดกำลังการผลิตให้สอดคล้องกับอุปสงค์ อาทิ ปริมาณการผลิต Polyethylene (PE) และ Polypropylene (PP) ซึ่งเป็นวัตถุดิบตั้งต้นสำหรับการผลิตพลาสติกที่ใช้ในชิ้นส่วนยานยนต์ลดลง -1.9% และ -1.4% ตามลำดับ สอดคล้องกับ MPI ของอุตสาหกรรมยานยนต์ที่หดตัว -17% เมื่อผนวกกับความสามารถในการแข่งขันของสินค้าปิโตรเคมีไทยที่ปรับลดลงเมื่อเทียบกับผู้ประกอบการในจีน สหรัฐฯ และตะวันออกกลางซึ่งมีการขยายกำลังการผลิตต่อเนื่อง และมีต้นทุนการผลิตที่ต่ำกว่าไทย ส่งผลให้เม็ดพลาสติกของไทยเสียส่วนแบ่งตลาดบางส่วนให้กับผู้ผลิตจากประเทศดังกล่าว จึงกระทบต่อการผลิตเม็ดพลาสติกของไทยเป็นลำดับ
-
การผลิตผลิตภัณฑ์พลาสติกเพิ่มขึ้น 3.6% จากปี 2566 จากการผลิตบรรจุภัณฑ์ และผลิตภัณฑ์พลาสติกกึ่งสำเร็จรูปและสำเร็จรูป หลังจากผู้ประกอบการเร่งระบายสินค้าคงคลัง (Inventory destocking) ในช่วงหลายปีก่อนหน้า นอกจากนี้ การเร่งเบิกจ่ายเงินงบประมาณภาครัฐทำให้การลงทุนโครงสร้างพื้นฐานตามโครงการต่างๆ ดำเนินไปได้ต่อเนื่อง สะท้อนจากการก่อสร้างภาครัฐพลิกกลับมาเร่งตัวขึ้นอย่างมีนัยสำคัญในช่วงครึ่งหลังของปี 2567
-
ยอดขายผลิตภัณฑ์พลาสติกในประเทศเพิ่มขึ้นเล็กน้อย 0.7% จากปี 2566 จากการขยายตัวของผลิตภัณฑ์ อาทิ พลาสติกแผ่น (+13.6%) และแผ่นฟิล์มพลาสติก (+12.8%) ขณะที่ท่อและข้อต่อพลาสติกหดตัว -4.8% ส่วนหนึ่งเป็นผลจากการก่อสร้างภาคเอกชนที่ลดลง -1.7% นอกจากนี้ ยอดขายผลิตภัณฑ์พลาสติกยังได้รับผลกระทบจากมาตรการขึ้นภาษีสินค้านำเข้าจากประเทศที่เกินดุลการค้ากับสหรัฐฯ โดยเฉพาะจีน ทำให้มีสินค้าจากต่างประเทศบางส่วนเข้ามาสู่ไทยมากขึ้น เมื่อผนวกกับความต้องการของผู้บริโภคที่ชะลอลง ทำให้ยอดขายโดยรวมเติบโตอย่างจำกัด
-
ปริมาณส่งออกเม็ดพลาสติกและผลิตภัณฑ์พลาสติกขยายตัว 0.2% และ 12.2% ตามลำดับ โดยการส่งออกเม็ดพลาสติกเพิ่มขึ้นในกลุ่ม Polyacetal (POM) ซึ่งใช้ในการผลิตยานยนต์ มีการส่งออกเพิ่มขึ้น 14.7% สอดคล้องกับยอดขายรถยนต์ไฟฟ้าทั่วโลกปี 2567 ที่เพิ่มขึ้นถึง 25.0% ต่อเนื่องจากปี 2566 ที่เพิ่มขึ้น 35% สำหรับการส่งออกเม็ดพลาสติกหลัก เช่น Polyethylene (PE) หดตัว -4.1% จากปี 2566 ตามการชะลอตัวของเศรษฐกิจโลกและอุปทานใหม่ที่เพิ่มเข้ามาซึ่งมากกว่าครึ่งเป็นอุปทานที่มาจากจีน โดยปริมาณส่งออกไปตลาดหลัก อาทิ จีน (สัดส่วน 26.9% ของการส่งออกเม็ดพลาสติก) หดตัว -7.1% และอินเดีย หดตัว -6.0% ด้านปริมาณนำเข้าเม็ดพลาสติกอยู่ที่ 2.8 ล้านตัน เพิ่มขึ้น 11% จากปีก่อนหน้า (ภาพที่ 10) สำหรับปริมาณส่งออกผลิตภัณฑ์พลาสติกเพิ่มขึ้นในกลุ่มถุง กระสอบพลาสติก แผ่นฟิล์ม พลาสติกปูพื้น เครื่องใช้พลาสติกในครัวเรือน และบรรจุภัณฑ์พลาสติก โดยปริมาณการส่งออกไปตลาดหลัก ได้แก่ อาเซียน (สัดส่วน 27.9%) ขยายตัว 2.8% และญี่ปุ่น (สัดส่วน 12.9%) เพิ่มขึ้น 2.6% ด้านการนำเข้าอยู่ที่ 1.2 ล้านตัน เพิ่มขึ้น 18.7% จากปี 2566
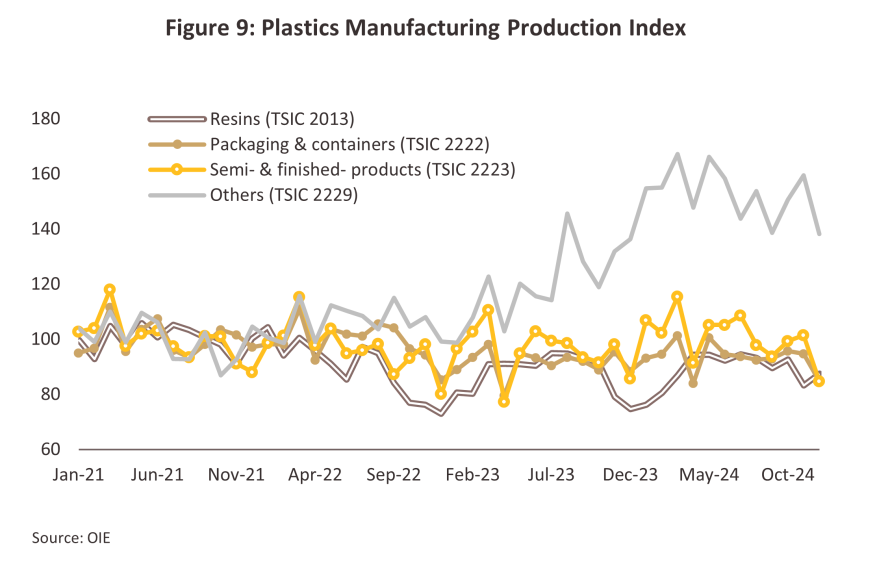
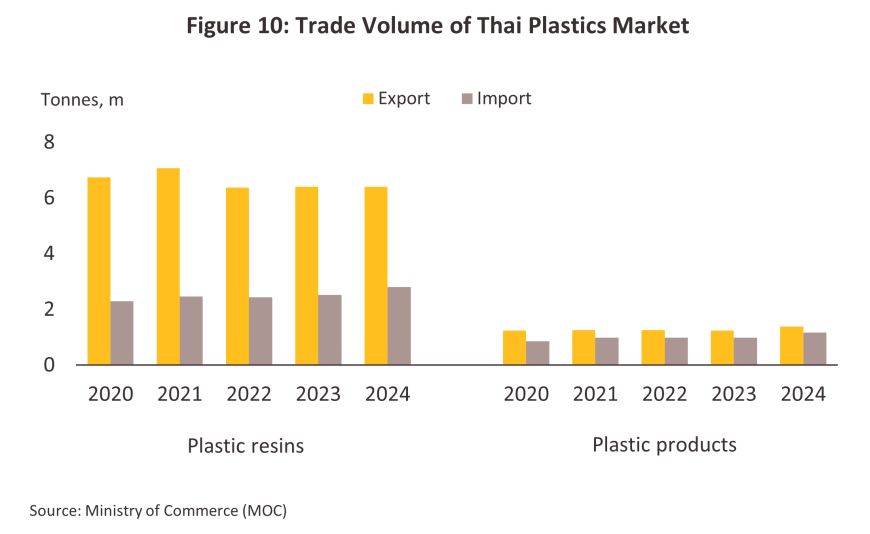
แนวโน้มอุตสาหกรรม
ปี 2568-2570 วิจัยกรุงศรีคาดว่าความต้องการใช้พลาสติกทั่วโลกจะเพิ่มขึ้นเฉลี่ย 2.0-3.0% ต่อปี โดยเศรษฐกิจโลกมีแนวโน้มเติบโตต่อเนื่องในระดับปานกลาง (IMF คาดจะอยู่ในช่วง 3.0-3.5% ต่อปี) ขณะที่ทางการจีนมีแผนออกมาตรการกระตุ้นเศรษฐกิจครั้งใหญ่ตั้งแต่ช่วงปลายปี 2567 ทำให้คาดว่าการบริโภคของจีนจะปรับตัวดีขึ้น อย่างไรก็ตาม เศรษฐกิจโลกยังมีแนวโน้มเติบโตต่ำกว่าช่วงก่อน COVID-19 (เฉลี่ย 3.7% ช่วงปี 2553-2562) และการขยายกำลังการผลิตเม็ดพลาสติกในภูมิภาคเอเชียทำให้มีอุปทานส่วนเกินเข้าสู่ตลาดเพิ่มขึ้น จะเป็นแรงกดดันให้ราคาเม็ดพลาสติกโดยรวมเพิ่มขึ้นได้ไม่มากนัก (ภาพที่ 11) สำหรับประเทศไทย คาดว่าเศรษฐกิจจะทยอยฟื้นตัวอย่างค่อยเป็นค่อยไป โดยมีแรงหนุนจากภาคท่องเที่ยว (คาดว่าจำนวนนักท่องเที่ยวจะทยอยเพิ่มขึ้นสู่ระดับก่อนเกิดวิกฤติ COVID-19 ในปี 2570) รวมถึงการฟื้นตัวของอุตสาหกรรมปลายทาง อาทิ อุตสาหกรรมผลิตบรรจุภัณฑ์ เครื่องใช้ไฟฟ้า อิเล็กทรอนิกส์ ชิ้นส่วนยานยนต์ ก่อสร้าง และเครื่องมือแพทย์ ซึ่งมีสัดส่วนรวมกันเกือบ 80% ของความต้องการใช้ผลิตภัณฑ์พลาสติกทั้งหมด ตลอดจนนโยบายส่งเสริมการลงทุนอุตสากรรมเป้าหมายของภาครัฐ จะมีส่วนสนับสนุนความต้องการใช้พลาสติกในห่วงโซ่อุปทาน อย่างไรก็ตาม อุตสาหกรรมพลาสติกไทยยังเผชิญความไม่แน่นอนจากหลายปัจจัยที่อาจกระทบการเติบโต โดยเฉพาะสงครามการค้าระหว่างสหรัฐฯ และจีนที่อาจทำให้ผลิตภัณฑ์พลาสติกหลั่งไหลเข้าสู่ไทยและประเทศคู่ค้าของไทย ทำให้การแข่งขันด้านราคากับสินค้าจีนจะรุนแรงขึ้นทั้งตลาดในและต่างประเทศ นอกจากนี้ กระแสรักษ์สิ่งแวดล้อมและความยั่งยืนส่งผลให้การผลิตสินค้าขั้นปลายบางประเภทมีแนวโน้มหันมาใช้วัตถุดิบที่เป็นมิตรกับสิ่งแวดล้อมมากขึ้น อีกทั้งความเสี่ยงด้านภูมิรัฐศาสตร์ (Geopolitical risks) ที่มีโอกาสตึงเครียดขึ้นเป็นระยะ จะกระทบราคาน้ำมันซึ่งเป็นวัตถุดิบหลัก ทำให้ต้นทุนการผลิตมีทิศทางปรับสูงขึ้น (กรณีฐาน คาดว่าราคาน้ำมันดิบดูไบจะเฉลี่ยในช่วง 75-80 ดอลลาร์สหรัฐ/บาร์เรล) จากปัจจัยข้างต้น วิจัยกรุงศรีจึงคาดว่าปี 2568-2570 ยอดขายผลิตภัณฑ์พลาสติกในประเทศและปริมาณส่งออกจะเพิ่มขึ้นในอัตราเฉลี่ย 2.0-3.0% ต่อปี (ภาพที่ 12) ซึ่งเป็นผลจากการฟื้นตัวของอุตสาหกรรมปลายทางที่มีความแตกต่างกัน สรุปได้ดังนี้
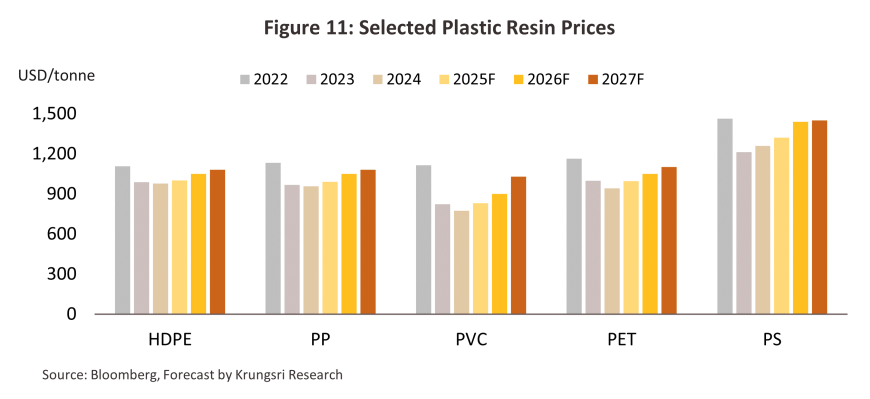
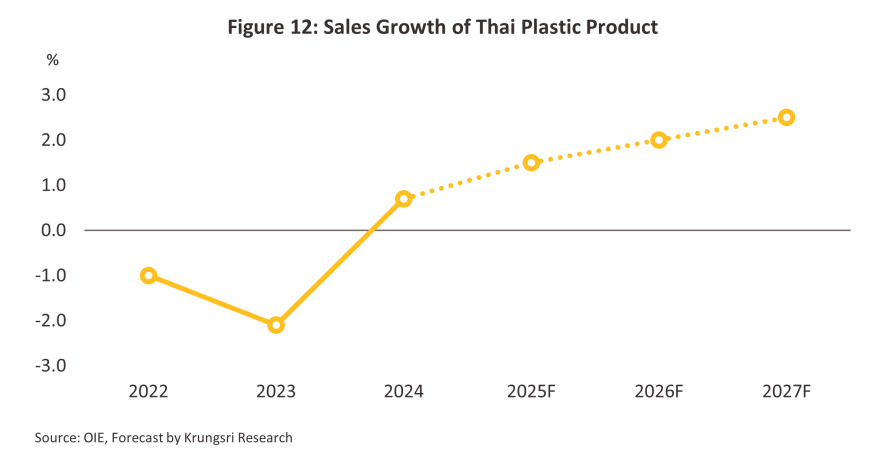
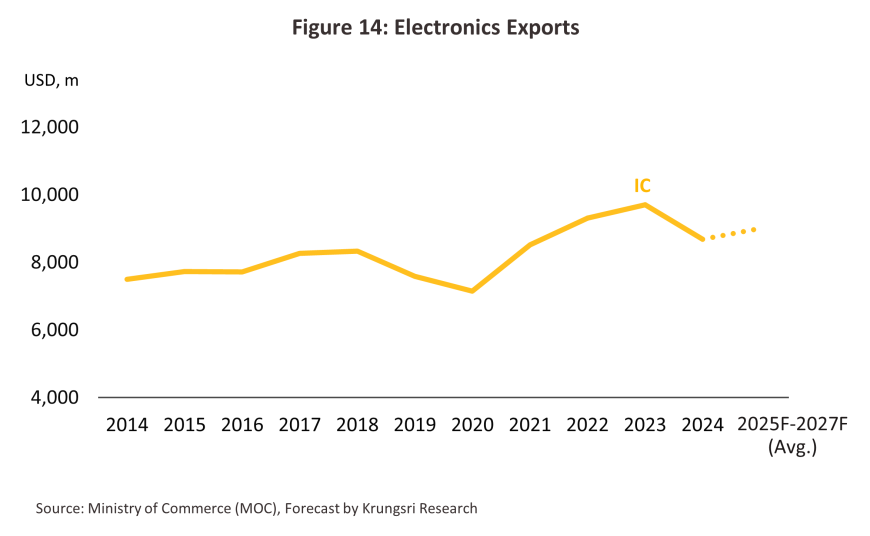
-
อุตสาหกรรมชิ้นส่วนยานยนต์: มีแนวโน้มชะลอตัวตามทิศทางการผลิตรถยนต์ โดยปี 2568-2570 คาดว่าการผลิตรถยนต์ในประเทศจะกระเตื้องขึ้นเล็กน้อยเฉลี่ยที่ 3.5% ถึง 4.5% ต่อปี (1.57-1.60 ล้านคันต่อปี) หลังจากหดตัวรุนแรง –20.2% ในปี 2567 (ภาพที่ 15) โดยปัจจัยที่จะหนุนอุปสงค์รถยนต์เพิ่มขึ้นมาจาก (1) กิจกรรมในภาคธุรกิจและการลงทุนจะปรับดีขึ้นตามการฟื้นตัวของเศรษฐกิจไทย โดยเฉพาะการเร่งลงทุนโครงสร้างพื้นฐานด้านการคมนาคมและการเติบโตของภาคท่องเที่ยว จะกระตุ้นความต้องการรถยนต์เพื่อการเดินทางและเพื่อการพาณิชย์เพิ่มขึ้น นอกจากนี้ ผลผลิตเกษตรที่มีแนวโน้มสูงขึ้น (คาดว่าปริมาณน้ำฝนจะเพิ่มขึ้นจากปรากฏการณ์ La Niña ในปี 2568 เอื้อต่อการเพาะปลูก) จะเพิ่มความต้องการใช้รถกระบะเพื่อบรรทุกพืชผลเกษตร (2) มาตรการสนับสนุนจากภาครัฐ อาทิ การปรับลดอัตราภาษีสรรพสามิตรถยนต์ HEV ในช่วงปี 2567-2570 และการผลิตรถยนต์ BEV ภายใต้มาตรการสนับสนุน EV 3.0 และ 3.5 จะเป็นปัจจัยบวกที่ทำให้ความต้องการใช้พลาสติกที่เกี่ยวข้องมีมากขึ้น เนื่องจากการผลิตรถ EV ใช้พลาสติกเป็นส่วนประกอบมากกว่า 50% ต่อคัน เพื่อลดน้ำหนักของรถ ซึ่งรวมถึงพลาสติกที่มีคุณสมบัติพิเศษ (Specialty) เช่น พีพีคอมพาวด์ (Polypropylene Compound) และ (3) ตลาดส่งออกรถยนต์มีแนวโน้มฟื้นตัวตามทิศทางการเติบโตทางเศรษฐกิจของประเทศคู่ค้า โดยเฉพาะตลาดในอาเซียน
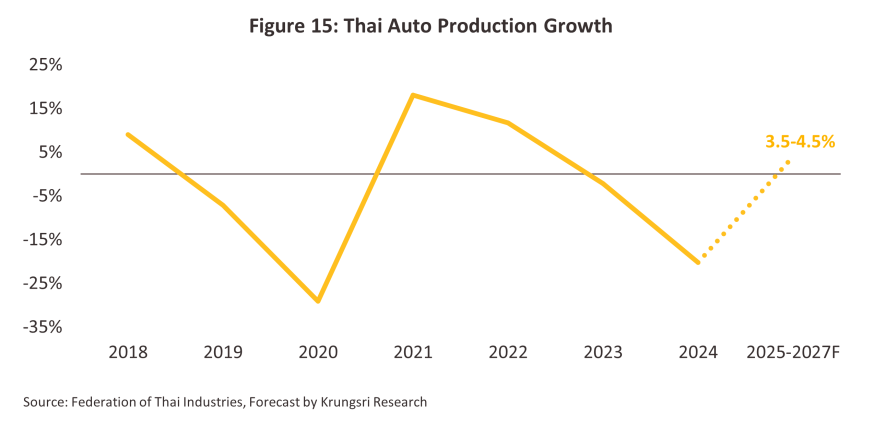
-
อุตสาหกรรมก่อสร้าง: มูลค่าการลงทุนก่อสร้างโดยรวมมีแนวโน้มขยายตัวเฉลี่ย 3.5-4.0% ต่อปี เทียบกับ 2.2% ปี 2567 โดยมีปัจจัยหนุนจากการที่ภาครัฐมีแนวโน้มเร่งดำเนินงานโครงสร้างพื้นฐานขนาดใหญ่โดยเฉพาะในเขตพัฒนาพิเศษภาคตะวันออก (Eastern Economic Corridor: EEC) ส่งผลให้งานก่อสร้างภาครัฐจะเติบโตที่ระดับ 4.0-4.5% ต่อปี ขณะที่งานก่อสร้างภาคเอกชนจะเติบโต 3.5-4.0% ต่อปี จากการพัฒนาโครงการอสังหาริมทรัพย์สำหรับที่อยู่อาศัยและโครงการเชิงพาณิชย์ (เช่น ศูนย์การค้าและอาคารสำนักงาน) ปัจจัยข้างต้นจะหนุนความต้องการใช้วัสดุก่อสร้างที่ทำจากพลาสติกหรือมีพลาสติกเป็นส่วนประกอบ อาทิ พีวีซี (Polyvinyl Chloride: ใช้ทำท่อประปา ท่อร้อยสายไฟ กรอบหน้าต่าง ประตู และพื้นไวนิล) โพลีคาร์บอเนต (Polycarbonate: ใช้ทำหลังคาโปร่งแสง กันสาด แผ่นกั้นห้อง และกระจกนิรภัย) พอลิโพรพิลีน (Polypropylene: ใช้ทำถังเก็บน้ำ ท่อระบายน้ำ และแผ่นกันซึม) (ภาพที่ 16) โดยแนวโน้มความต้องการใช้พลาสติกในภาคก่อสร้างจะเน้นวัสดุที่ทนทาน คุณภาพสูงและเป็นมิตรกับสิ่งแวดล้อมมากขึ้น
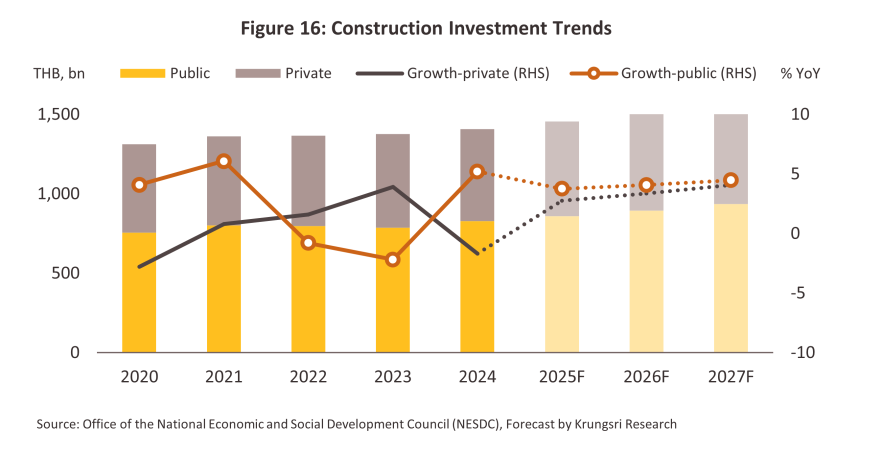
ระยะต่อไป คาดว่าจะมีการใช้พลาสติกในการผลิตเครื่องมือแพทย์แทนโลหะ เซรามิคและแก้วมากขึ้น เนื่องจากมีต้นทุนวัตถุดิบที่ต่ำกว่า ขณะที่มีคุณสมบัติเหมาะสม อาทิ ขึ้นรูปได้ง่าย สามารถปรับรูปร่างให้ตรงกับความต้องการ มีน้ำหนักเบา ทนต่อสารเคมีและกระบวนการฆ่าเชื้อด้วยรังสี ทำให้ไม่เกิดสารปนเปื้อนจากการกัดกร่อนเหมือนโลหะ ทั้งยังสามารถนำไปผสมกับวัสดุอื่น เช่น ยางหรือสารเคมีชีวภาพ ทำให้ได้วัสดุเชิงประกอบ (Composite) ที่มีประสิทธิภาพ ปลอดภัยและมีคุณสมบัติตรงตามความต้องการ โดยเฉพาะเม็ดพลาสติกชนิดพิเศษที่สามารถผลิต Smart material และอุปกรณ์การแพทย์ประเภทสอดใส่ในร่างกายผู้ป่วย เช่น โครงสร้างลิ้นหัวใจเทียม
ผู้ประกอบการไทยที่มีศักยภาพมีแนวโน้มเร่งปรับตัวเพื่อรักษาระดับการเติบโต โดยการพัฒนาผลิตภัณฑ์พลาสติกที่มีมูลค่าเพิ่มสูงเพื่อตอบรับการเติบโตของอุตสาหกรรมที่ต้องการวัสดุคุณภาพสูง (อาทิ ยานยนต์ไฟฟ้า เครื่องมือแพทย์ หุ่นยนต์ และอากาศยาน ) รวมถึงการผลิตพลาสติกทางเลือกที่เป็นมิตรต่อสิ่งแวดล้อมหรือ “พลาสติกชีวภาพ (Bio-plastic)” (อาทิ Sustainable Polypropylene Products การพัฒนาเม็ดพลาสติก PE100RC เพื่อใช้ผลิตท่อ HDPE สำหรับงานโครงสร้างพื้นฐาน และการผลิตฟิล์มยืดจากเม็ดพลาสติกรีไซเคิล (Post-Consumer-Recycled resin: PCR) ตามนโยบายสนับสนุนภาครัฐ ซึ่งมีการปรับกฏระเบียบให้เอื้อต่อการพัฒนาอุตสาหกรรม (อาทิ การอนุญาตให้โรงงานที่ใช้อ้อยเป็นวัตถุดิบ เช่น โรงงานเคมีชีวภาพและโรงงานเอทานอล สามารถตั้งในบริเวณใกล้กับโรงงานน้ำตาลได้ จากเดิมต้องมีระยะห่างการตั้งโรงงานที่ 50 กิโลเมตร และมาตรการลดหย่อนภาษีนิติบุคคลเป็นจำนวน 25% ของรายจ่ายเพื่อซื้อผลิตภัณฑ์พลาสติกที่ย่อยสลายได้ทางชีวภาพ (ปี 2565-2567) เมื่อผนวกกับการเป็นแหล่งผลิตวัตถุดิบตั้งต้น (อาทิ อ้อย มันสำปะหลังและข้าวโพด) จึงส่งผลให้ไทยเป็นผู้ส่งออกรายสำคัญของอุตสาหกรรมพลาสติกชีวภาพในตลาดโลก โดยสมาคมอุตสาหกรรมพลาสติกชีวภาพแห่งประเทศไทย (TBIA) คาดว่าการผลิตเม็ดพลาสติกชีวภาพจะเพิ่มขึ้นเป็น 375,000-400,000 ตันต่อปีในระยะข้างหน้า จากศักยภาพกำลังการผลิตปัจจุบันที่ 95,000 ตันต่อปี ขณะที่ภาคเอกชนรายใหญ่ของไทยมีการร่วมทุนกับผู้ประกอบการรายใหญ่จากต่างประเทศ (อาทิ NatureWorks บริษัทร่วมทุนระหว่าง Cargill ของสหรัฐฯ และ PTT Global Chemical (GC) ของไทย ผลิตพลาสติก PLA ด้วยกำลังการผลิต 75,000 ตันต่อปี คาดจะเริ่มการผลิตในปี 2568 และ Braskem ผู้ประกอบการรายใหญ่ด้านพลาสติกชีวภาพของบราซิลและ SCG Chemicals ของไทย จะตั้งโรงงานผลิตเอทิลีนชีวภาพ (Green-Ethylene) เพื่อเป็นวัตถุดิบสำหรับผลิตเม็ดพลาสติกชีวภาพ (Green-Polyethylene) ทั้งนี้ เพื่อตอบรับความต้องการพลาสติกที่เป็นมิตรกับสิ่งแวดล้อม ซึ่งมีทิศทางเติบโตต่อเนื่องในตลาดโลกโดยเฉพาะเอเชียและยุโรป และนำมาซึ่งโอกาสใหม่ๆ ให้แก่ภาคธุรกิจในระยะข้างหน้า
ความท้าทายของอุตสาหกรรมในระยะข้างหน้า จะมาจาก (1) กำลังซื้อทั้งในและต่างประเทศที่ฟื้นตัวค่อนข้างช้า ขณะที่จีนมีการลงทุนทำนิคมอุตสาหกรรมปิโตรเคมีขนาดใหญ่ในประเทศในช่วงที่ผ่านมา ทำให้การนำเข้าเม็ดพลาสติกจากไทยมีแนวโน้มลดลงเป็นลำดับ (2) กฎระเบียบด้านสิ่งแวดล้อมที่มีความเข้มงวดมากขึ้นในต่างประเทศ โดยเฉพาะสหภาพยุโรป อาทิ EU Bottle Cap Regulation กำหนดให้ฝาขวดพลาสติกทั้งหมดหลังจากเปิดแล้ว ต้องผูกติดอยู่กับภาชนะที่มีความจุน้อยกว่า 3 ลิตร โดยบังคับใช้อย่างเป็นทางการเมื่อ 3 กรกฏาคม 2567 และ CBAM (Carbon Border Adjustment Mechanism) ซึ่งแม้พลาสติกยังไม่ได้อยู่ในกลุ่มสินค้าที่ต้องรายงานการปล่อยคาร์บอน แต่อาจได้รับผลกระทบในระยะต่อไป เนื่องจากมีการปล่อยก๊าซเรือนกระจกสูงในกระบวนการผลิต ผู้ผลิตพลาสติกจึงต้องเตรียมพร้อมสำหรับมาตรการที่อาจเข้มงวดขึ้นในอนาคต และ (3) การมุ่งพัฒนาการผลิตพลาสติกให้มีความยั่งยืนและมีประสิทธิภาพ ทั้งด้านการใช้พลังงาน และการเพิ่มความสามารถในการแข่งขัน รวมถึงการเตรียมพร้อมด้านการมีส่วนรับผิดชอบในการบริหารทรัพยากรขยะและของเสียที่เกิดขึ้นจากการผลิตและการใช้งานของผู้บริโภค (EPR: Extended Producer Responsibility) ซึ่งจะกำหนดเป็นกฎหมายในอีก 2-3 ปีข้างหน้า
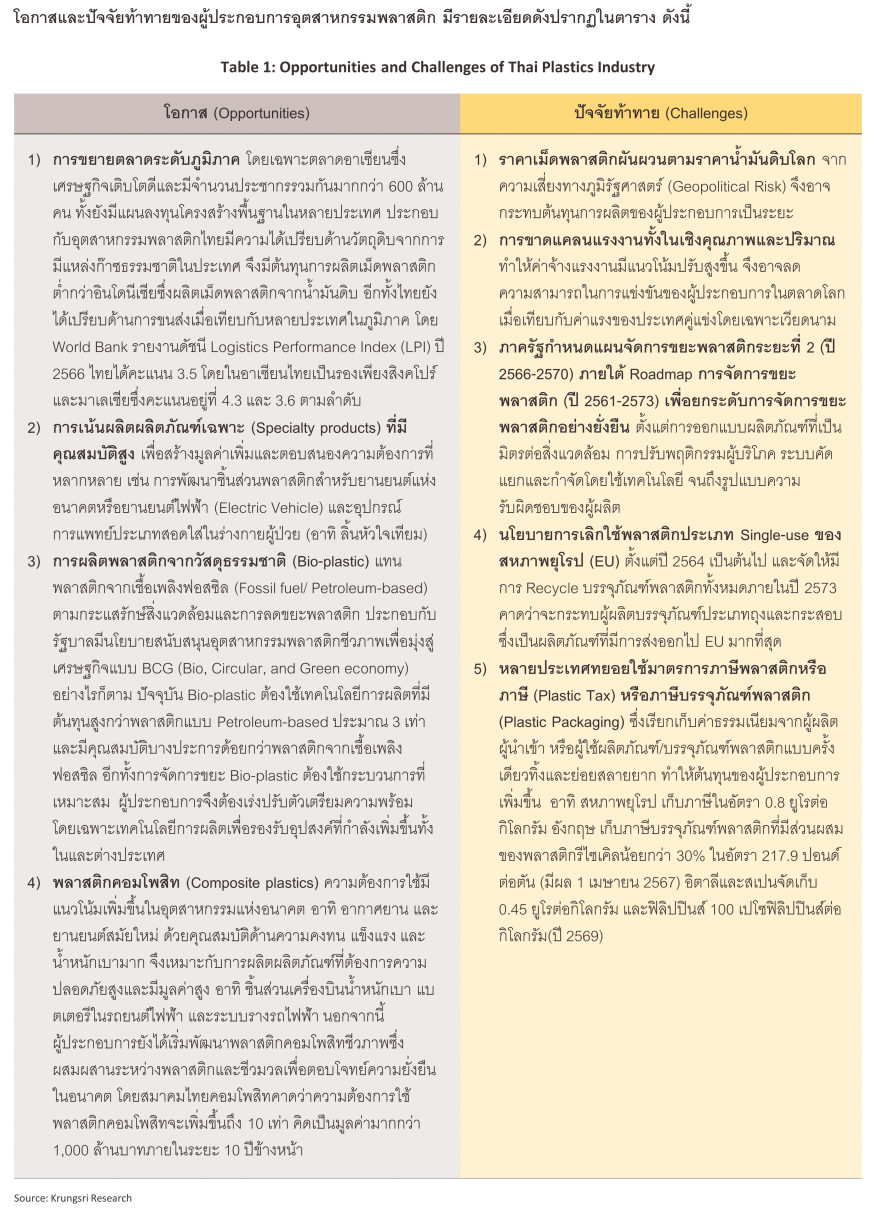
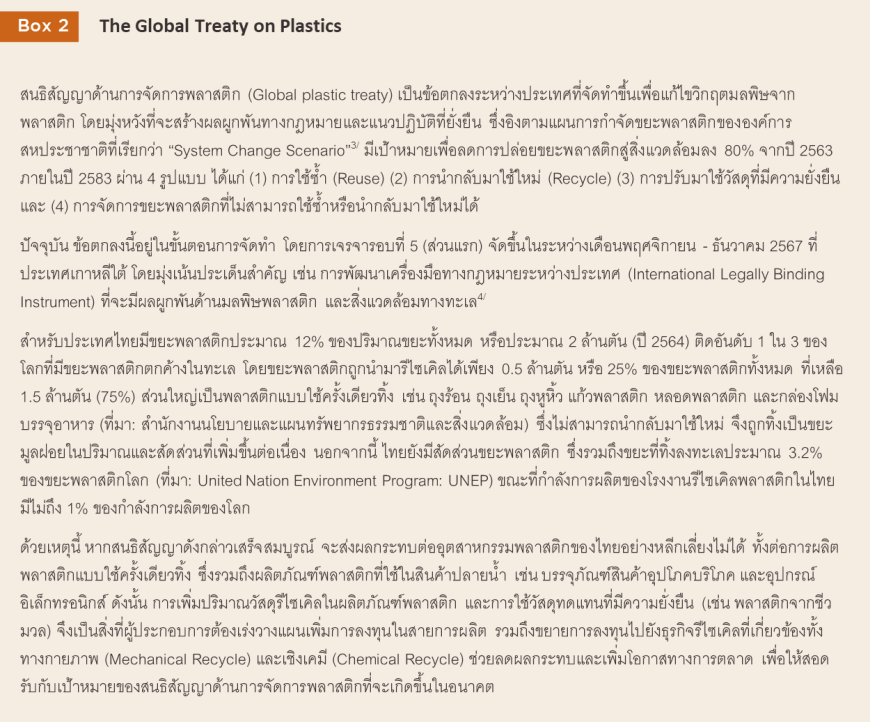
1/ สำรวจผู้ประกอบการ 3,065 ราย หรือประมาณ 64.8% ของผู้ประกอบการในอุตสาหกรรม โดยผู้ประกอบการแต่ละรายอาจมีวิธีการผลิตมากกว่า 1 วิธี
2/ ที่มา: Statista
3/ ข้อมูลเกี่ยวกับ”System change scenario” ขององค์การสหประชาชาติสามารถศึกษารายละเอียดเพิ่มเติมได้ที่ https://wedocs.unep.org/bitstream/handle/20.500.11822/42277/Plastic_pollution.pdf?sequence=3
4/ ข้อมูลเกี่ยวกับการเจรจาสนธิสัญญาด้านการจัดการพลาสติกรอบที่ 4 สามารถศึกษารายละเอียดเพิ่มเติมได้ที่ https://www.unep.org/news-and-stories/press-release/decisive-fifth-session-negotiations-global-plastic-pollution-treaty