ปี 2563 อุตสาหกรรมชิ้นส่วนยานยนต์ไทยมีแนวโน้มหดตัวตามอุตสาหกรรมการผลิตยานยนต์ โดยเฉพาะชิ้นส่วนเพื่อประกอบยานยนต์ (OEM) ผลจากการแพร่ระบาดของไวรัส COVID-19 ทำให้กิจกรรมการผลิตในห่วงโซ่ยานยนต์สะดุดลงในช่วงครึ่งแรกปี 2563 ท่ามกลางกำลังซื้อทั่วโลกรวมถึงไทยที่หดตัวรุนแรง อย่างไรก็ตาม ความต้องการชิ้นส่วนเพื่อการทดแทน (REM) ยังคงขยายตัวได้ตามการเพิ่มขึ้นของจำนวนยานยนต์สะสม ประกอบกับผู้บริโภคบางส่วนมีแนวโน้มซ่อม/บำรุงยานยนต์เก่าเพื่อยืดเวลาการซื้อยานยนต์ใหม่ออกไป สำหรับปี 2564-2565 คาดว่าการผลิตยานยนต์ในประเทศจะฟื้นตัวโดยเพิ่มขึ้นเฉลี่ย 3-4% ต่อปี ซึ่งเป็นไปในทิศทางเดียวกับอุตสาหกรรมการผลิตยานยนต์โลก
ประเด็นท้าทายที่ต้องติดตามใกล้ชิด ได้แก่ การใช้มาตรการปกป้องทางการค้าในหลายประเทศ โดยเฉพาะกรณีสอบสวนการทุ่มตลาดยางรถยนต์ส่งออกจากไทยไปสหรัฐฯ และข้อตกลงยกเว้นภาษีนำเข้าระหว่างกันสำหรับรถยนต์ที่ใช้ชิ้นส่วนฯ ภายในกลุ่มประเทศสมาชิก (สหรัฐฯ เม็กซิโก และแคนาดา) ซึ่งอาจกระทบการส่งออกชิ้นส่วนฯ จากไทยไปยังประเทศดังกล่าว
ข้อมูลพื้นฐาน
อุตสาหกรรมชิ้นส่วนยานยนต์ได้รับการส่งเสริมจากรัฐบาลไทยอย่างต่อเนื่องนับจากปี 2506 1/ โดยระยะเริ่มแรก ภาครัฐเน้นออกมาตรการเพื่อสนับสนุนการลงทุนผลิตและใช้ชิ้นส่วนยานยนต์ในประเทศ โดยเฉพาะการปรับขึ้นภาษีนำเข้ารถยนต์สำเร็จรูป (Complete Built-Up: CBU) และชิ้นส่วนครบชุดสมบูรณ์ (Complete Knock-Down: CKD) ต่อมาคณะกรรมการส่งเสริมการลงทุน (Board of Investment: BOI) ได้ออกมาตรการส่งเสริมการลงทุน อาทิ การยกเว้นภาษีเงินได้นิติบุคคล และการยกเว้นอากรขาเข้าเครื่องจักร เพื่อดึงดูดนักลงทุนต่างชาติให้เข้ามาตั้งฐานการผลิตในไทย นอกจากนี้ ภาครัฐกำหนดสัดส่วนบังคับใช้ชิ้นส่วนยานยนต์ที่ผลิตในประเทศ (Local Content Requirements: LCR) ในการผลิตยานยนต์ ซึ่งปัจจุบันข้อกำหนดดังกล่าวได้ถูกยกเลิกแล้ว 2/ อย่างไรก็ดี การผลิตรถยนต์นั่งในไทยยังคงใช้ชิ้นส่วนที่ผลิตในประเทศคิดเป็นสัดส่วน 60-80% ของมูลค่าชิ้นส่วนยานยนต์ทั้งหมด ขณะที่รถยนต์นั่งประเภท Eco-car และรถปิกอัพใช้ชิ้นส่วนที่ผลิตในประเทศ 90% ส่วนรถจักรยานยนต์ใช้ชิ้นส่วนในประเทศเกือบทั้งหมด ในปัจจุบัน มีการทำข้อตกลงการค้าเสรีระหว่างไทยกับประเทศต่างๆ อาทิ ความตกลงการค้าเสรีอาเซียน (AFTA) ความตกลงหุ้นส่วนเศรษฐกิจไทย-ญี่ปุ่น (JTEPA) และความตกลงการค้าเสรีไทย-ออสเตรีย (TAFTA) ส่งผลให้อัตราภาษีนำเข้า CBU และ CKD ปรับลดลง
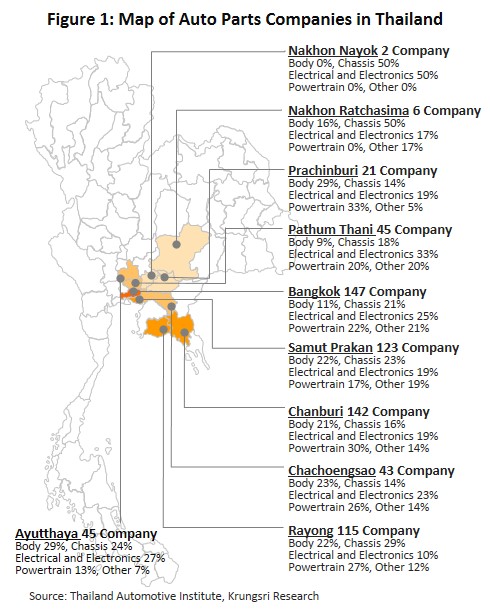
มาตรการสนับสนุนต่างๆ ดังกล่าวส่งผลให้นักลงทุนทั้งไทยและต่างชาติเข้ามาลงทุนอุตสาหกรรมชิ้นส่วนฯ ในไทยอย่างต่อเนื่อง บริษัทสัญชาติไทยและบริษัทร่วมทุนที่สำคัญ ได้แก่ บจ.ไทยซัมมิท ออโต้พาร์ท บจ.สามมิตรโอโตพาร์ท บมจ. สมบูรณ์ แอ๊ดวานซ์ เทคโนโลยี และบจ.ไทยออโต้ เพรสพาร์ท ส่วนบริษัทข้ามชาติรายใหญ่ของโลกที่เข้ามาตั้งฐานผลิตในไทย อาทิ Robert Bosch, Denso, Magna, Continental, ZF, Aisin Seiki สำหรับบริษัทสัญชาติญี่ปุ่นที่เป็นผู้ผลิตชิ้นส่วนฯ ของค่ายรถญี่ปุ่น (ตารางที่ 1) ส่วนใหญ่เข้ามาลงทุนผลิตชิ้นส่วนฯ ที่ได้รับการส่งเสริมจากภาครัฐ ได้แก่ (1) กลุ่มชิ้นส่วนฯ ที่ผลิตจากยางพารา (อาศัยความพร้อมด้านวัตถุดิบยางพาราในประเทศ) ได้แก่ ท่อยาง สายพาน ยางขอบกระจก และยางยานพาหนะที่ต้องใช้เทคโนโลยีการผลิตระดับสูง (2) กลุ่มชิ้นส่วน
ระบบส่งกำลัง (Powertrain) และเครื่องยนต์ ซึ่งมีห่วงโซ่อุปทานที่ซับซ้อน 3/ และมีมูลค่าสูงกว่า 1 ใน 3 ของต้นทุนการผลิตรถยนต์ระบบสันดาปภายใน (Internal Combustion Engine: ICE) ทั้งยังเป็นกลุ่มที่ภาครัฐให้การส่งเสริมการผลิตตลอดทั้งห่วงโซ่อุปทาน อาทิ หม้อน้ำ ท่อไอเสีย ระบบจ่ายน้ำมัน ถังน้ำมัน ระบบจุดระเบิด และเกียร์ เป็นต้น และ (3) กลุ่มชิ้นส่วนประกอบรถยนต์ไฟฟ้า (Electric Vehicles: EVs) รัฐบาลส่งเสริมการลงทุนในลักษณะแผนงานรวม (Package)4/ ปัจจุบันมีผู้ผลิตรถยนต์ทยอยขอรับส่งเสริมการลงทุนผลิตรถยนต์ไฟฟ้าและชิ้นส่วนฯ อย่างต่อเนื่อง 5/ โดยเฉพาะแบตเตอรี่ซึ่งถือเป็นชิ้นส่วนฯ สำคัญในรถยนต์ไฟฟ้า (มูลค่าสูงกว่า 30% ของต้นทุนการผลิตรถยนต์ไฟฟ้า) อีกทั้งยังออกนโยบายเร่งรัดการลงทุนผลิตรถยนต์ไฟฟ้าทั้งแบบแบตเตอรี่ (Battery Electric Vehicle: BEV) และแบบไฮบริด (Hybrid Electric Vehicle: HEV) โดยกำหนดให้ผู้ขอรับส่งเสริมการลงทุนผลิตรถ BEV สามารถขอรับส่งเสริมการลงทุนผลิตรถ HEV ได้ (ยื่นภายใน 31 ธันวาคม 2562) ภายใต้เงื่อนไข คือ (1) การผลิตรถ HEV ต้องผลิตพร้อมชิ้นส่วนสำคัญของรถอย่างน้อย 1 ชิ้น ภายใน 3 ปีนับตั้งแต่วันที่ออกบัตรส่งเสริมฯ และต้องผลิตชิ้นส่วนสำคัญอย่างน้อย 4 ชิ้นภายในปีที่ 3 หลังเริ่มผลิตรถ HEV และ (2) การผลิตรถ BEV ต้องผลิตพร้อมชิ้นส่วนสำคัญอย่างน้อย 1 ชิ้น ภายในปีที่ 3 นับจากวันผลิตรถ HEV โดยชิ้นส่วนฯ สำคัญ ได้แก่ Battery, Traction motor, Drive Control Unit (DCU) และ Battery Management System (BMS)
ด้านโครงสร้างตลาด ตลาดในประเทศเป็นตลาดหลักมีสัดส่วน 60-70% ของรายรับรวมในอุตสาหกรรมการผลิตชิ้นส่วนฯ แบ่งเป็น ตลาดชิ้นส่วนฯ เพื่อการประกอบยานยนต์ (Original Equipment Manufacturer: OEM) และตลาดชิ้นส่วนฯ เพื่อการทดแทนหรืออะไหล่ยานยนต์ (Replacement Equipment Manufacturer: REM) โดยมีรายละเอียด ดังนี้
- ชิ้นส่วนฯ OEM: มูลค่าตลาดมีสัดส่วน 30-40% ของตลาดชิ้นส่วนฯ รวมในประเทศ ขยายตัวตามปริมาณการผลิตยานยนต์ โดยมากกว่า 80% เป็นการใช้ชิ้นส่วนฯ ที่ผลิตในประเทศ ส่วนที่เหลือเป็นชิ้นส่วนฯ ที่ต้องใช้เทคโนโลยีขั้นสูงจากบริษัทแม่หรือซัพพลายเออร์ของบริษัทแม่ในต่างประเทศ เช่น ชิ้นส่วนอิเล็กทรอนิกส์ที่ใช้ในระบบควบคุมยานยนต์ (Microcontroller Chips: MCUs) จากญี่ปุ่น นอกจากนี้ ยังมีการนำเข้าชิ้นส่วนรถบรรทุกและรถโดยสารขนาดใหญ่จากจีนเพื่อรองรับการตั้งฐานการผลิตรถยนต์ในไทย อาทิ รถยนต์นั่ง “MG” (บริษัท SAIC Motor-CP) รถบรรทุก “DFSK” (บริษัท ตงฟง มอเตอร์ส) และรถโดยสาร “Golden Dragon” (เบสท์ริน กรุ๊ป) เป็นต้น
- ชิ้นส่วนฯ REM: มูลค่าตลาดคิดเป็น 60-70% ของตลาดชิ้นส่วนฯ รวมในประเทศ เติบโตในทิศทางเดียวกับจำนวนยานยนต์จดทะเบียนสะสมในประเทศ จากความต้องการเปลี่ยนชิ้นส่วนฯ (อะไหล่) ตามระยะเวลาการใช้งานและ/หรือระยะทาง ช่องทางการจำหน่ายมีหลากหลาย ทั้งศูนย์บริการซ่อมบำรุงของผู้จำหน่าย/ดีลเลอร์ยานยนต์ ร้านค้าส่ง-ค้าปลีกอะไหล่ยานยนต์ ตลอดจนอู่ซ่อมทั่วไป ด้านมูลค่านำเข้าชิ้นส่วนฯ REM มีสัดส่วน 10-20% ของมูลค่าการนำเข้าชิ้นส่วนทั้งหมด ส่วนใหญ่นำเข้ามาจากญี่ปุ่น (สัดส่วน 43% ของมูลค่าการนำเข้าชิ้นส่วนฯ REM ทั้งหมด) และจีน (17%) รวมถึงสหรัฐฯ (8%) ที่เข้ามารุกตลาดไทยมากขึ้น
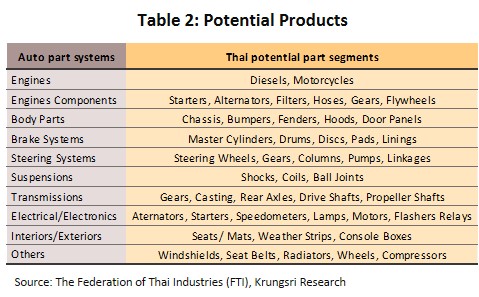
การส่งออกชิ้นส่วนฯ มีสัดส่วน 30-40% ของรายรับรวมในอุตสาหกรรมการผลิตชิ้นส่วนฯ แบ่งเป็น ชิ้นส่วนฯ OEM (สัดส่วน 80-85% ของมูลค่าส่งออกรวม) และชิ้นส่วนฯ REM (สัดส่วน 15-20%) ชิ้นส่วนฯ ที่ไทยส่งออกเป็นหลัก ได้แก่ เครื่องยนต์ ชุดสายไฟ ตัวถัง กระจก ชุดเกียร์ ยางรถยนต์ และชิ้นส่วนฯ ที่ผลิตจากยางพารา ไทยถือเป็นประเทศที่มีศักยภาพการแข่งขันสูงในตลาดโลก อาศัยความได้เปรียบจากความพร้อมด้านห่วงโซ่อุปทานก่อให้เกิดการประหยัดต่อขนาด และสามารถผลิตชิ้นส่วนฯ ที่มีคุณภาพเป็นที่ยอมรับของผู้ผลิตยานยนต์ นอกจากนี้ ไทยมีความได้เปรียบด้านทำเลที่ตั้ง เอื้อสำหรับการเป็นศูนย์กลางการผลิตชิ้นส่วนฯ ในภูมิภาคอาเซียน6/ ส่งผลให้ไทยเป็นหนึ่งในแหล่งผลิตชิ้นส่วนฯ ที่สำคัญของโลก (Global Sourcing) สะท้อนจากปี 2562 ไทยส่งออกชิ้นส่วนฯ (ทุกประเภท) เป็นอันดับ 1 ของอาเซียน และอันดับ 14 ของโลก ขณะเดียวกัน เป็นอันดับ 3 ด้านการส่งออกยางยานพาหนะ อันดับ 4 ด้านชิ้นส่วนรถจักรยานยนต์ (ไม่รวมเครื่องยนต์และยางยานพาหนะ) อันดับ 11 ด้านเครื่องยนต์ และอันดับ 16 ด้านชิ้นส่วนรถยนต์ (ไม่รวมเครื่องยนต์และยางยานพาหนะ) ส่วนใหญ่ส่งออกไปยังฐานการผลิตยานยนต์ในอาเซียน ได้แก่ อินโดนีเซีย มาเลเซีย เวียดนามและฟิลิปปินส์ สัดส่วนรวมกันคิดเป็น 25% ของมูลค่าส่งออกชิ้นส่วนฯ รวม รองลงมา คือ สหรัฐฯ (สัดส่วน 18%) และญี่ปุ่น (สัดส่วน 10%) อย่างไรก็ตาม ไทยมีต้นทุนแรงงานค่อนข้างสูงเมื่อเทียบกับอินโดนีเซียและเวียดนาม ขณะที่การวิจัยและพัฒนาด้อยกว่ามาเลเซีย (ภาพที่ 3)
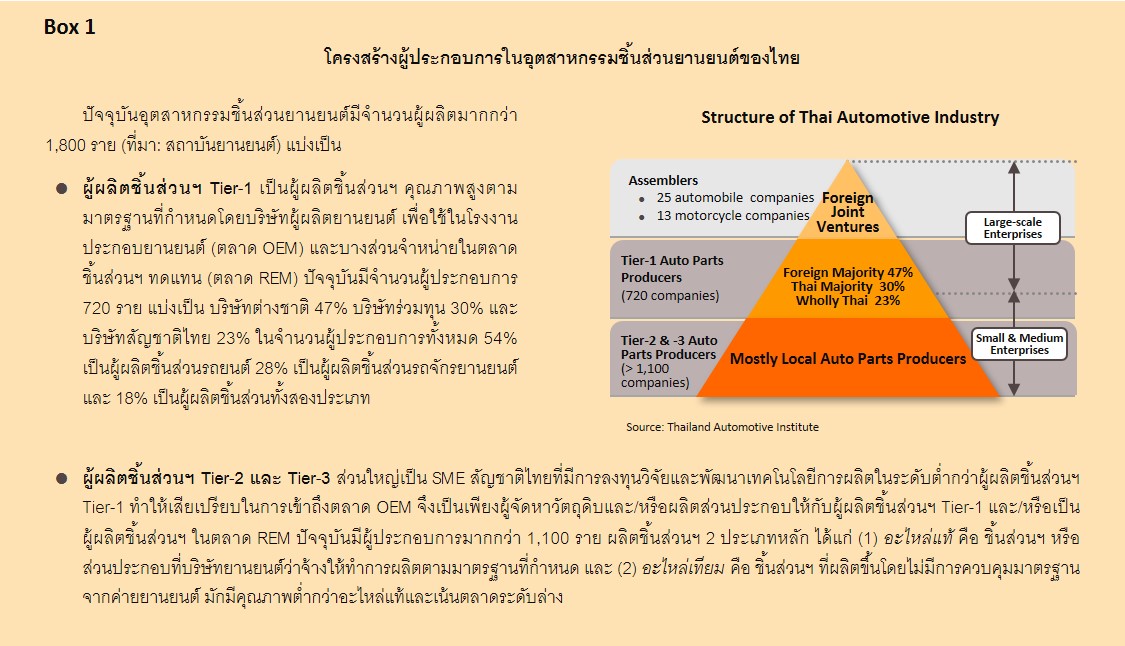
สถานการณ์ที่ผ่านมา
อุตสาหกรรมชิ้นส่วนยานยนต์ของไทยเติบโตในทิศทางเดียวกับอุตสาหกรรมยานยนต์ โดยช่วงปี 2555-2561 ตลาดชิ้นส่วนฯ ผันผวนตามภาวะเศรษฐกิจ ขณะที่การส่งออกชิ้นส่วนฯ เติบโตชะลอลงตามเศรษฐกิจประเทศคู่ค้า อย่างไรก็ตาม อานิสงส์จากการลงทุน/ขยายกำลังการผลิตของผู้ผลิตต่างชาติ โดยเฉพาะญี่ปุ่น ซึ่งใช้ไทยเป็นฐานการผลิตชิ้นส่วนฯ เพื่อนำไปผลิตต่อ/ประกอบยานยนต์ในกลุ่มประเทศอาเซียน ส่งผลให้อุตสาหกรรมชิ้นส่วนฯ โดยรวมยังขยายตัวได้ สามารถสรุปได้ดังนี้
- ปี 2555-2556 ปริมาณการผลิตยานยนต์เติบโตอย่างมีนัยสำคัญ อานิสงส์จากโครงการรถคันแรก ขณะเดียวกัน การผลิตรถจักรยานยนต์เติบโตอย่างรวดเร็ว จากมาตรการกระตุ้นเศรษฐกิจรากหญ้าของรัฐบาลที่หนุนกำลังซื้อในต่างจังหวัด ส่งผลให้ความต้องการใช้ชิ้นส่วนฯ OEM สูงสุดเป็นประวัติการณ์ สะท้อนจากรายได้ (ในรูปเงินบาท) ที่เติบโตถึง 27.8% ในปี 2555 ก่อนชะลอลงมาอยู่ที่ 6.1% ในปี 2556
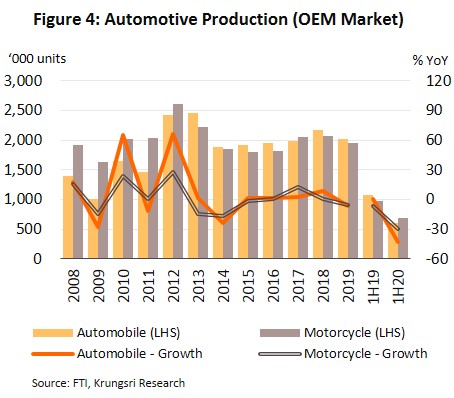
- ปี 2557 ความต้องการใช้ชิ้นส่วนฯ OEM ลดลงอย่างมาก หลังสิ้นสุดโครงการรถคันแรก ผลจากอุปสงค์รถยนต์ถูกใช้ไปล่วงหน้า ประกอบกับภาคเกษตรเผชิญภาวะภัยแล้งและราคาสินค้าเกษตรตกต่ำ รวมถึงปัญหาการเมืองในประเทศ ทำให้กำลังซื้อของผู้บริโภคซบเซา ส่งผลให้ยอดจำหน่ายรถยนต์และรถจักรยานยนต์ในประเทศหดตัว 33.7% และ 15.1% ตามลำดับ อย่างไรก็ดี การส่งออกรถยนต์และรถจักรยานยนต์เติบโตต่อเนื่องตามเศรษฐกิจประเทศคู่ค้า ด้านตลาด REM เติบโตชะลอลง เนื่องจากผู้บริโภคชะลอการเปลี่ยนอะไหล่บางประเภท เช่น ยางรถยนต์ ประกอบกับความต้องการเปลี่ยนอะไหล่ของรถยนต์ในโครงการรถคันแรกยังมีเฉพาะอะไหล่สึกหรอบางรายการ อาทิ ไส้กรองน้ำมันเครื่อง ไส้กรองอากาศ หลอดไฟ หัวเทียน ใบปัดน้ำฝน และผ้าเบรก ปัจจัยข้างต้นส่งผลให้รายได้ของผู้ประกอบการโดยรวมหดตัว 7.3%
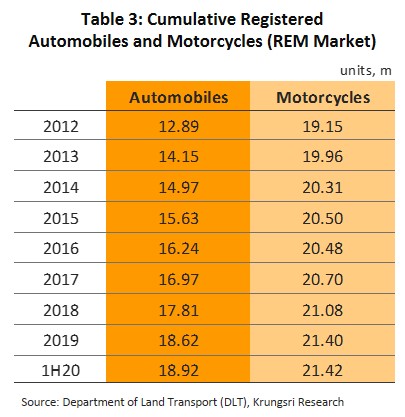
- ปี 2558-2561 ตลาดชิ้นส่วนฯ ในประเทศฟื้นตัวอย่างค่อยเป็นค่อยไป โดยความต้องการชิ้นส่วนฯ OEM เพิ่มขึ้นตามปริมาณการผลิตยานยนต์ที่กลับมาขยายตัวเร่งขึ้น ขณะที่ผู้ประกอบการขยายการลงทุน/กำลังการผลิตชิ้นส่วนฯ เพื่อส่งออกอย่างต่อเนื่อง ยกตัวอย่างเช่น บจ.สยามโตโยต้าอุตสาหกรรมขยายกำลังการผลิตเครื่องยนต์ดีเซล โรงงานผลิตชิ้นส่วนฯ ของค่าย Honda ผลิตเครื่องยนต์เบนซินขนาด 1.8 ลิตรและเครื่องยนต์ VTEC TURBO ขนาด 1.5 ลิตร บจ.มาสด้า พาวเวอร์เทรน เมนูแฟคเจอริ่ง ขยายกำลังการผลิตเครื่องยนต์สกายแอคทีฟเบนซินขนาด 1.3 ลิตรและ 2 ลิตร และ บจ.ดาน่า โฮลดิ้ง คอร์ปอเรชั่น ขยายกำลังการผลิตเกียร์ เพลา และเพลาขับ ด้านผู้ประกอบการสัญชาติจีนเร่งขยายการลงทุนผลิตยางยานพาหนะเพื่อส่งออก อาทิ Sentury Tire, Huayi Group และ Dadi Group สำหรับตลาดชิ้นส่วนฯ REM อุปสงค์เติบโตดี ปัจจัยหนุนจากความต้องการเปลี่ยนอะไหล่รถยนต์ในโครงการรถคันแรก (รถยนต์ที่มีอายุใช้งานครบ 3-5 ปี จะทยอยเปลี่ยนชิ้นส่วนฯ ที่มีมูลค่าสูง ตามระยะทางการใช้งาน อาทิ แบตเตอรี่และยางยานพาหนะ) ส่งผลให้รายได้รวมของอุตสาหกรรมชิ้นส่วนฯ เพิ่มขึ้นเฉลี่ย 6.0% ต่อปี (ภาพที่ 5)
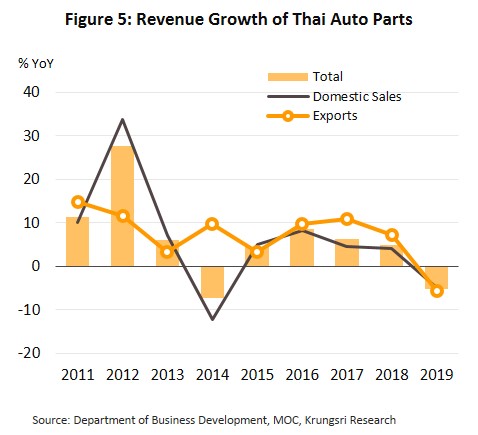
ปี 2562 ปริมาณการผลิตชิ้นส่วนฯ หดตัวเป็นครั้งแรกในรอบ 5 ปี ผลจากภาวะเศรษฐกิจชะลอตัวกดดันกำลังซื้อ โดยดัชนีผลผลิตอุตสาหกรรมชิ้นส่วนยานยนต์ (MPI) หดตัว 5.1% จากปี 2561 (ภาพที่ 6) ทั้งนี้ ความต้องการชิ้นส่วน OEM ลดลงตามปริมาณการผลิตยานยนต์ในประเทศ ขณะที่ความต้องการชิ้นส่วน REM เติบโตตามจำนวนยานยนต์สะสมที่เพิ่มขึ้นต่อเนื่อง ด้านตลาดส่งออกชิ้นส่วนฯ หดตัวตามการผลิตยานยนต์ของประเทศคู่ค้าที่ชะลอตัว ผลจากสงครามการค้าระหว่างสหรัฐฯ และจีน ส่งผลให้รายได้ (ในรูปเงินบาท) ของผู้ประกอบการอุตสาหกรรมชิ้นส่วนฯ หดตัว 5.2% โดยมีรายละเอียด ดังนี้
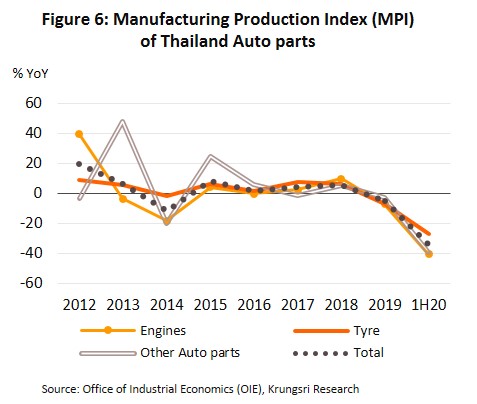
- ตลาดในประเทศ: ความต้องการชิ้นส่วนฯ OEM ปี 2562 ปรับลดตามการหดตัวของปริมาณการผลิตรถยนต์ (-7.1% อยู่ที่ 2.01 ล้านคัน) และรถจักรยานยนต์ (-5.6% อยู่ที่ 1.95 ล้านคัน) ผลจากเศรษฐกิจไทยชะลอตัว อีกทั้งรายได้เกษตรกรทรงตัวในระดับต่ำกดดันกำลังซื้อผู้บริโภคในจังหวัดภูมิภาค นอกจากนี้ สถาบันการเงินเข้มงวดในการอนุมัติสินเชื่อรถยนต์ รวมถึงผู้บริโภคบางส่วนยืดอายุการใช้งานรถเพื่อชะลอการซื้อใหม่ (วิจัยกรุงศรีประเมินอายุการใช้งานรถยนต์นั่งและรถปิกอัพอยู่ที่ 8.8 ปี และ 12.1 ปี ในปี 2562 เพิ่มขึ้นจาก 8.7 ปีและ 11.9 ปี ในปี 2561) ความต้องการ ชิ้นส่วนฯ REM เติบโตต่อเนื่องตามจำนวนยานยนต์จดทะเบียนสะสมที่เพิ่มขึ้น 2.9% (ตารางที่ 3) โดยเฉพาะรถยนต์และรถจักรยานยนต์ที่มีอายุมากกว่า 5 ปีมีจำนวนสะสม 12.9 ล้านคัน และ 12.0 ล้านคัน ตามลำดับ ทั้งยังได้อานิสงส์จากโครงการช้อปช่วยชาติ 7/ ที่ให้นำค่าใช้จ่ายในการซื้อยางยานพาหนะมาหักลดหย่อนภาษี จึงมีส่วนหนุนให้เกิดความต้องการเปลี่ยนยางอะไหล่เพิ่มขึ้น มูลค่าการนำเข้าชิ้นส่วนฯ หดตัว 4.4% อยู่ที่ 1.7 หมื่นล้านดอลลาร์สหรัฐฯ (ตารางที่ 4) โดยแหล่งนำเข้าหลักหดตัวแรง ได้แก่ ญี่ปุ่น (-5.4%) จีน (-12.1%)8/ และอาเซียน (-4.5%)
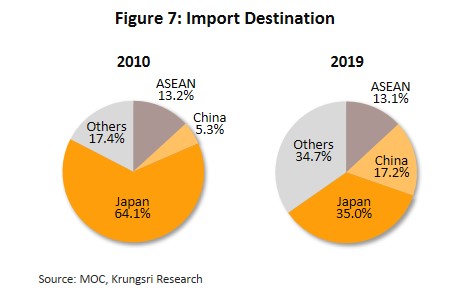
- ตลาดส่งออก: ปี 2562 หดตัว 2.3% อยู่ที่ 2.1 หมื่นล้านดอลลาร์สหรัฐฯ (ตารางที่ 5) ประกอบด้วย
- เครื่องยนต์ (Engines): มูลค่าส่งออกหดตัว 14.5% เป็นครั้งแรกในรอบ 5 ปี สอดคล้องกับการผลิตรถยนต์โลกที่ลดลง 5.2% ต่อเนื่องเป็นปีที่ 2 ผลจากภาวะเศรษฐกิจประเทศคู่ค้าชะลอตัว อีกทั้งเป็นช่วงเปลี่ยนผ่านเทคโนโลยีจากยานยนต์เครื่องยนต์สันดาปภายในเป็นยานยนต์ไฟฟ้า การผลิตรถยนต์ในญี่ปุ่นและอาเซียน 9/ (ตลาดส่งออกหลักของไทย มีสัดส่วนรวมกัน 40.3% ของมูลค่าส่งออกเครื่องยนต์ทั้งหมดของไทย) มีปริมาณการผลิตรวมกัน 11.8 ล้านคัน หดตัว 0.7% จากปี 2561
- ยางยานพาหนะ (Tyre): ปี 2562 มูลค่าส่งออกขยายตัว 13.1% อยู่ที่ 5.8 พันล้านดอลลาร์สหรัฐฯ ปัจจัยหนุนมาจาก (1) บจ. สยามมิชลิน เปิดสายการผลิตใหม่สำหรับยางรถ OFF-ROAD เพื่อจำหน่ายในไทยและส่งออกไปยังตลาดเอเชีย แอฟริกา และตะวันออกกลาง รวมถึงผลิตให้กับโรงงานรถยนต์ อาทิ ฟอร์ด อีซูซุ มาสด้า และโตโยต้า และ (2) สงครามการค้าระหว่างสหรัฐฯ และจีน ทำให้ผู้ประกอบการจากจีนย้ายฐานการผลิตยางยานพาหนะมาที่ไทยอย่างต่อเนื่อง10/ ส่งผลให้ไทยส่งออกยางยานพาหนะไปยังสหรัฐฯ เพิ่มขึ้น โดยปี 2562 นับเป็นครั้งแรกที่ไทยเป็นผู้ส่งออกยางยานพาหนะอันดับหนึ่งของสหรัฐฯ ด้วยส่วนแบ่งตลาด 18.8% ของมูลค่านำเข้ายางยานพาหนะทั้งหมดของสหรัฐฯ แทนที่จีนซึ่งเคยรั้งอันดับหนึ่งมาโดยตลอด (ปี 2562 จีนมีส่วนแบ่งตลาดในสหรัฐฯ 8.5% ลดลงเกือบครึ่งจาก 16.7% ปี 2561) นอกจากนี้ ไทยยังเป็นผู้ส่งออกยางยานพาหนะอันดับ 3 ของโลก มีส่วนแบ่งตลาด 7.0% ของมูลค่าส่งออกยางยานพาหนะทั้งหมดของโลก รองจากจีน (18.7%) และเยอรมนี (7.2%) ทั้งนี้ ตลาดส่งออกยางยานพาหนะที่สำคัญของไทย ได้แก่ สหรัฐฯ (สัดส่วน 46.2% ของมูลค่าส่งออกยางยานพาหนะทั้งหมดของไทย) อาเซียน (13.9%) และสหภาพยุโรป (8.9%)
- ชิ้นส่วนฯ อื่นๆ (Other auto parts): ปี 2562 มูลค่าส่งออกหดตัว 3.7% อยู่ที่ 1.0 หมื่นล้านดอลลาร์สหรัฐฯ แบ่งเป็น (1) กลุ่มชิ้นส่วนรถยนต์ อาทิ ชิ้นส่วนครบชุดสมบูรณ์ (CKDs) กระปุกเกียร์ ระบบเบรก ถุงลมนิรภัย เพลาขับ และแชสซีส์ มูลค่าส่งออกหดตัว 4.7% เป็นครั้งแรกในรอบ 10 ปี อยู่ที่ 9.5 พันล้านดอลลาร์สหรัฐฯ และ (2) กลุ่มชิ้นส่วนรถจักรยานยนต์ อาทิ CKDs ล้อรถ ระบบเบรก อานรถ และคันเหยียบ มูลค่าส่งออกขยายตัว 9.1% อยู่ที่ 835.5 ล้านดอลลาร์สหรัฐฯ อานิสงส์จากการที่กลุ่มผู้ผลิตย้ายฐานการผลิตมาไทยมากขึ้น ทำให้ความต้องการชิ้นส่วนรถจักรยานยนต์ยังคงเติบโตต่อเนื่อง แม้ว่าการผลิตรถจักรยานยนต์โลกหดตัว 2.6% สำหรับตลาดส่งออก11/ อินโดนีเซีย มาเลเซีย เวียดนาม และฟิลิปปินส์ เป็นตลาดส่งออกหลักของไทย มีสัดส่วนรวมกัน 30.3% ของมูลค่าส่งออกชิ้นส่วนฯ อื่นๆ ทั้งหมดของไทย รองลงมาได้แก่ ญี่ปุ่น (13.7%) และสหรัฐฯ (7.9%)
ในช่วงครึ่งแรกของปี 2563 ดัชนีผลผลิตอุตสาหกรรมชิ้นส่วนยานยนต์หดตัว 34.7% YoY ผลจากการแพร่ระบาดของไวรัส COVID-19 ทำให้กิจกรรมการผลิตในห่วงโซ่ยานยนต์หยุดชะงัก ขณะเดียวกัน ความต้องการชิ้นส่วนฯ ทั้งในประเทศและตลาดส่งออกลดลง โดยมีรายละเอียดดังนี้
- ตลาดในประเทศ: ความต้องการชิ้นส่วนฯ OEM มีทิศทางหดตัวตามปริมาณการผลิตรถยนต์ (-43.1% YoY อยู่ที่ 6.1 แสนคัน) และรถจักรยานยนต์ (-30.0% YoY อยู่ที่ 6.8 แสนคัน) ขณะที่ความต้องการชิ้นส่วนฯ REM ยังคงขยายตัว เนื่องจากผู้บริโภคบางส่วนชะลอการซื้อยานยนต์ใหม่ และหันมาซ่อม/บำรุงยานยนต์เก่า จากปัจจัยเศรษฐกิจที่ไม่เอื้ออำนวย ด้านการนำเข้าชิ้นส่วนฯ โดยรวมหดตัว 22.8% YoY มูลค่า 6.5 พันล้านดอลลาร์สหรัฐฯ โดยแหล่งนำเข้าหลักหดตัวรุนแรง ได้แก่ ญี่ปุ่น (สัดส่วน 33.3%) หดตัว 26.4% YoY มูลค่า 2.2 พันล้านดอลลาร์ และจีน (สัดส่วน 18.5%) หดตัว 17.3% YoY มูลค่า 1.2 พันล้านดอลลาร์ อย่างไรก็ตาม การนำเข้าจากสหรัฐฯ (สัดส่วน 10.6%) เพิ่มขึ้น 13.5% YoY มูลค่า 685.2 ล้านดอลลาร์ ส่วนใหญ่เป็นการนำเข้าชิ้นส่วนรถจักรยานยนต์เพื่อผลิตรถจักรยานยนต์ขนาดใหญ่สัญชาติสหรัฐฯ แบรนด์ ‘Harley-Davidson’
- ตลาดส่งออก: ภาวะเศรษฐกิจโลกหดตัว และการหยุดกิจกรรมการผลิตยานยนต์ชั่วคราวในหลายประเทศ ทำให้มูลค่าส่งออกชิ้นส่วนฯ โดยรวมหดตัว 20.3% YoY อยู่ที่ 8.1 พันล้านดอลลาร์สหรัฐฯ แบ่งเป็น
- เครื่องยนต์: มูลค่าส่งออกหดตัว 16.2% YoY อยู่ที่ 1.9 พันล้านดอลลาร์ ตามการหดตัวของตลาดหลักเช่น อาเซียน (-26.5% YoY มูลค่า 517.6 ล้านดอลลาร์) และญี่ปุ่น (-35.8% YoY มูลค่า 123.4 ล้านดอลลาร์) อย่างไรก็ตาม ตลาดจีนขยายตัว 54.6% YoY อยู่ที่ 279.7 ล้านดอลลาร์ อานิสงส์จากห่วงโซ่การผลิตในจีนที่หยุดชะงัก (Supply Chain Disruption) ซึ่งส่วนใหญ่เป็นการส่งออกของค่ายรถสัญชาติญี่ปุ่น ได้แก่ Honda, Mitsubishi, Suzuki, Nissan และ Yamaha
- ยางยานพาหนะ: มูลค่าส่งออกหดตัว 14.3% YoY อยู่ที่ 2.4 พันล้านดอลลาร์ เป็นการหดตัวเกือบทุกตลาดหลัก ได้แก่ สหรัฐฯ (-7.5% YoY มูลค่า 1.1 พันล้านดอลลาร์) อาเซียน (-24.5% YoY มูลค่า 307.6 ล้านดอลลาร์) และสหภาพยุโรป (-30.2% YoY มูลค่า 182.9 ล้านดอลลาร์)
- ชิ้นส่วนฯ อื่นๆ: มูลค่าส่งออกหดตัว 25.4% YoY อยู่ที่ 3.8 พันล้านดอลลาร์ ประกอบด้วย ชิ้นส่วนรถยนต์หดตัว 26.4% YoY มูลค่า 3.5 พันล้านดอลลาร์ โดยหดตัวในตลาดอาเซียน (-33.1% YoY) ญี่ปุ่น (-17.8%) และสหภาพยุโรป (-19.9%) ชิ้นส่วนรถจักรยานยนต์หดตัว 12.9% YoY มูลค่า 340.1 ล้านดอลลาร์ เป็นการหดตัวในเกือบทุกตลาด อาทิ อาเซียน (-26.3% YoY) ญี่ปุ่น (-2.8%) สหรัฐฯ (-16.1%) และสหภาพยุโรป (-18.3%)
แนวโน้มอุตสาหกรรม
ปี 2563 การผลิตชิ้นส่วนยานยนต์มีแนวโน้มหดตัวต่อเนื่องจากปีก่อน การแพร่ระบาดของไวรัส COVID-19 ทำให้กำลังซื้อซบเซารุนแรง ประกอบกับมีการปิดสายพานการผลิตยานยนต์ทั่วโลกในช่วงครึ่งแรกของปี ทำให้ความต้องการชิ้นส่วนฯ OEM หดตัวตาม อย่างไรก็ตาม คาดว่าความต้องการชิ้นส่วนฯ REM จะเติบโตต่อเนื่อง ช่วยพยุงรายได้ของผู้ประกอบการไม่ให้ทรุดหนัก สำหรับปี 2564-2565 คาดว่าความต้องการชิ้นส่วนฯ จะทยอยฟื้นตัวตามภาวะเศรษฐกิจ ช่วยหนุนผลประกอบการของอุตสาหกรรมกระเตื้องขึ้นอย่างค่อยเป็นค่อยไป
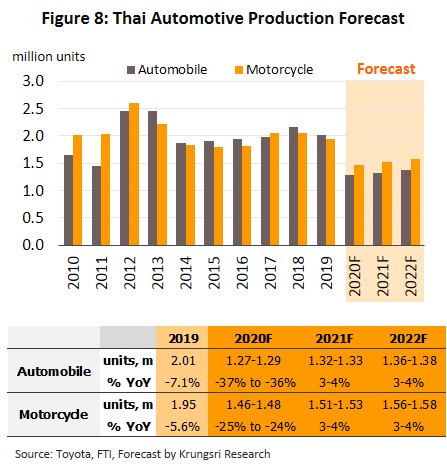
ตลาดในประเทศ: ปี 2563 การผลิตชิ้นส่วนฯ มีแนวโน้มหดตัวก่อนกระเตื้องขึ้นในปี 2564-2565 ตามทิศทางการฟื้นตัวของการผลิตยานยนต์ ซึ่งจะกระตุ้นความต้องการชิ้นส่วนฯ OEM (ภาพที่ 8) โดยวิจัยกรุงศรีคาดว่าปี 2563 ปริมาณการผลิตรถยนต์จะหดตัว 36-37% หนักที่สุดในรอบ 21 ปี และรถจักรยานยนต์จะหดตัว 24-25% มากเป็นประวัติการณ์ ผลจากกำลังซื้อซบเซาตามการหดตัวของเศรษฐกิจโลก (-5.0%) และไทย (-10.3%) ประกอบกับสถาบันการเงินเพิ่มความเข้มงวดในการอนุมัติสินเชื่อ สำหรับปี 2564-2565 คาดว่าการผลิตรถยนต์และรถจักรยานยนต์จะฟื้นตัวเฉลี่ย 3-4% ต่อปี ปัจจัยหนุนจากภาวะเศรษฐกิจที่ทยอยฟื้นตัว และความต้องการเปลี่ยนรถยนต์ โดยเฉพาะรถยนต์ในโครงการรถคันแรกซึ่งมีอายุการใช้งานเฉลี่ย 8-9 ปี ตลอดจนการเร่งผลิตรถยนต์ตามแผนส่งเสริมการลงทุน Eco-car ซึ่งรวมถึงรถยนต์ไฟฟ้าที่ขอรับสิทธิประโยชน์ สำหรับชิ้นส่วนฯ REM คาดว่าความต้องการจะเติบโตต่อเนื่อง หนุนโดยจำนวนรถยนต์สะสมที่มีอายุมากกว่า 5 ปีมีแนวโน้มเพิ่มขึ้นเฉลี่ย 6% ต่อปี โดยเฉพาะรถยนต์ในโครงการรถคันแรกจำเป็นต้องเปลี่ยนชิ้นส่วนฯ ตามอายุและระยะทางการใช้งาน ขณะที่ชิ้นส่วนฯ เพื่อการตกแต่งจะเติบโตไม่มากนัก เนื่องจากจำนวนรถยนต์สะสมที่อายุน้อยกว่า 5 ปี มีทิศทางลดลงต่อเนื่อง (ภาพที่ 9)
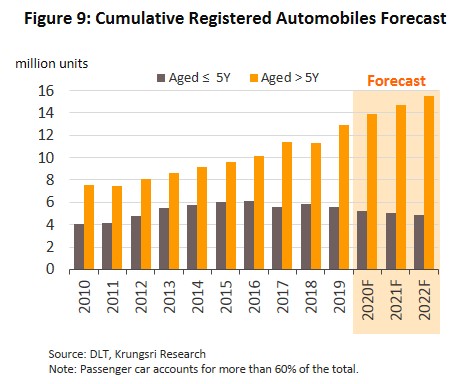
ตลาดส่งออก: ปี 2563 มูลค่าส่งออกมีแนวโน้มหดตัวตามการผลิตยานยนต์โลก แต่ในปี 2564-2565 คาดว่าจะทยอยฟื้นตัวตามทิศทางเศรษฐกิจโลก ส่งผลให้ความต้องการชิ้นส่วนฯ ปรับเพิ่มขึ้นอย่างค่อยเป็นค่อยไป อีกทั้งความไม่แน่นอนของนโยบายการค้าระหว่างสหรัฐฯ และจีน อาจส่งผลบวกต่อการส่งออกชิ้นส่วนฯ ของไทย อานิสงส์จากการโยกย้ายคำสั่งซื้อระหว่างกัน (Trade diversion) นอกจากนี้ การแพร่ระบาดของไวรัส COVID-19 อาจทำให้อุตสาหกรรมชิ้นส่วนฯ ของไทยได้ประโยชน์จากการย้ายฐานการผลิตของผู้ประกอบการต่างชาติมาที่ไทยในระยะต่อไป เพื่อลดความเสี่ยงจากการพึ่งพิงฐานการผลิตเพียงแห่งเดียวซึ่งอาจนำมาสู่การขาดแคลนชิ้นส่วนฯ ในภาวะวิกฤติ ส่งผลให้อุตสาหกรรมชิ้นส่วนฯ ของไทยมีโอกาสยกระดับคุณภาพและเทคโนโลยีการผลิต รวมถึงการขยายตลาดส่งออกในอนาคต
อุตสาหกรรมอาจเผชิญปัจจัยท้าทาย ได้แก่ (1) การยกเว้นภาษีรถยนต์นำเข้าภายในกลุ่มประเทศสมาชิกข้อตกลงการค้าสหรัฐฯ เม็กซิโก และแคนาดา (USMCA) ซึ่งมีเงื่อนไขต้องใช้ชิ้นส่วนฯ ภายในกลุ่มไม่ต่ำกว่า 75% ของชิ้นส่วนรถยนต์ทั้งหมด (มีผล 1 กรกฏาคม 2563) อาจทำให้ไทยส่งออกชิ้นส่วนฯ ไปกลุ่มประเทศดังกล่าวได้ลดลง (สัดส่วนรวมกัน 21.2% ของมูลค่าส่งออกชิ้นส่วนทั้งหมดของไทย) (2) สหรัฐฯ อาจใช้มาตรการตอบโต้การทุ่มตลาด (Anti-dumping: AD) และการอุดหนุน (Countervailing Duty: CVD) ยางรถยนต์นำเข้าจากไทย จากเดิมเก็บภาษีนำเข้ากรณีไม่ใช้สิทธิ GSP ที่อัตรา 3.7% (ปัจจุบันอยู่ระหว่างไต่สวน คาดว่าจะรู้ผลในช่วงเดือนพฤศจิกายน 2563 ถึงพฤษภาคม 2564) อาจทำให้ไทยเสียโอกาสส่งออกยางรถยนต์ไปตลาดสหรัฐฯ และอาจมีการหาแหล่งผลิตใหม่มาทดแทนไทย และ (3) ผู้ประกอบการชิ้นส่วนฯ REM (ผู้ประกอบการสัญชาติไทยมากกว่า 1,100 ราย และส่วนใหญ่เป็นผู้ผลิตชิ้นส่วนฯ Tier 2 และ Tier 3) เผชิญการแข่งขันที่รุนแรงขึ้น ทั้งจากผู้ผลิตต่างชาติที่ย้ายฐานการผลิตมาไทยมากขึ้น และจากผู้ผลิตชิ้นส่วนฯ Tier 1 (ส่วนใหญ่ผลิตชิ้นส่วนฯ OEM) อาจกระจายความเสี่ยงโดยเพิ่มสัดส่วนการผลิตชิ้นส่วนฯ REM ซึ่งตลาดมีความผันผวนไม่มากนัก
ในระยะยาว ผู้ผลิตชิ้นส่วนฯ ของไทยอาจได้รับผลกระทบจากนโยบายภาครัฐที่ส่งเสริมการลงทุนผลิตรถยนต์ไฟฟ้าแบตเตอรี่และรถยนต์ไฮบริด ซึ่งรัฐบาลวางเป้าหมายจำนวนรถยนต์ไฟฟ้าจดทะเบียนสะสมอยู่ที่ 1.2 ล้านคันภายในปี 2579 อย่างไรก็ดี ในระยะแรกคาดว่าตลาดรถยนต์ไฟฟ้าของไทยจะเติบโตอย่างค่อยเป็นค่อยไป โดยส่วนใหญ่จะเป็นรถยนต์ไฮบริด (Hybrid Electric Vehicle: HEV) และรถยนต์ไฟฟ้าปลั๊กอินไฮบริด (Plug-in Hybrid Electric Vehicle: PHEV) ส่งผลให้ในช่วงปี 2563-2565 ผู้ผลิตชิ้นส่วนฯ OEM จะได้รับผลกระทบไม่มากนัก เนื่องจากความต้องการใช้ชิ้นส่วนฯ สำหรับผลิตรถยนต์ระบบสันดาปภายใน (ICE) ยังคงมีอยู่ จากนั้นภายในระยะเวลา 4-6 ปีข้างหน้า คาดว่าตลาดรถยนต์ไฟฟ้าแบบแบตเตอรี่ (Battery Electric Vehicle: BEV) จะมีสัดส่วนเพิ่มขึ้นอย่างรวดเร็ว ผลจากการพัฒนาแบตเตอรี่ลิเทียมไอออนทำให้ราคาปรับลดลงต่อเนื่อง 12/ (ปี 2563 ราคาแบตเตอรี่ลิเทียมไอออนอยู่ที่ 156 USD/kWh ลดลงจาก 1,200 USD/kWh ปี 2553) โดย Bloomberg คาดว่าภายในปี 2565 ราคารถยนต์ไฟฟ้า BEV จะเริ่มใกล้เคียงรถยนต์ ICE13/ (เทียบขนาดรถยนต์ที่ใกล้เคียงกัน) แนวโน้มการเติบโตของตลาดรถยนต์ไฟฟ้า BEV ดังกล่าวจะเป็นจุดเปลี่ยนสำคัญของอุตสาหกรรมชิ้นส่วนฯ ในไทย ซึ่งผู้ประกอบการต้องเร่งปรับตัว เนื่องจากในช่วงที่ผ่านมาเน้นพัฒนาห่วงโซ่อุปทานสำหรับเครื่องยนต์สันดาปภายในมาโดยตลอด ขณะที่การผลิตรถยนต์ไฟฟ้า BEV จะใช้ชิ้นส่วนฯ ลดลงอย่างมาก ยกตัวอย่างเช่น ระบบส่งกำลัง ใช้ชิ้นส่วนฯ ประมาณ 20 ชิ้น เทียบกับรถยนต์ ICE ที่ใช้มากกว่า 2,000 ชิ้น นอกจากนี้ แบตเตอรี่จะกลายเป็นชิ้นส่วนฯ หลักแทนเครื่องยนต์ คิดเป็นสัดส่วน 30% ของต้นทุนการผลิตรถยนต์ไฟฟ้า BEV
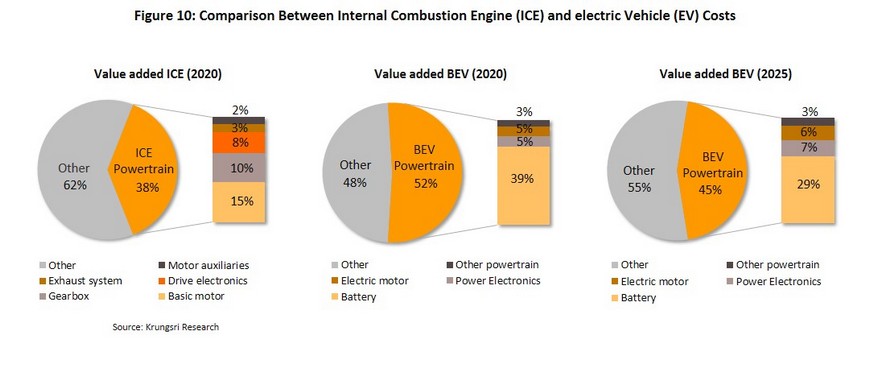
ปัจจุบันเริ่มมีการลงทุนชิ้นส่วนฯ สำหรับรถยนต์ไฟฟ้าในไทยโดยเฉพาะแบตเตอรี่ อาทิ โตโยต้าผลิตแบตเตอรี่นิเกิลเมทัลไฮดราย และ BMW ผลิตแบตเตอรี่แบบลิเทียมไอออน สถานการณ์เช่นนี้จะลดความต้องการใช้ชิ้นส่วนฯ OEM บางประเภทในระยะยาว อาทิ เครื่องยนต์ หม้อน้ำ ท่อไอเสีย ระบบจ่ายน้ำมัน ถังน้ำมัน ระบบจุดระเบิด และเกียร์ ขณะที่ชิ้นส่วนฯ อาทิ ชิ้นส่วนช่วงล่าง (Suspension) ตัวถัง ระบบส่องสว่าง และอุปกรณ์ภายในรถ เป็นชิ้นส่วนฯ จำเป็นที่ยังมีความต้องการต่อเนื่อง ขณะเดียวกัน รถยนต์ไฟฟ้า BEV ควบคุมการทำงานด้วยระบบอิเล็กทรอนิกส์จึงช่วยยืดอายุการใช้งานชิ้นส่วนฯ บางประเภท ทำให้ความถี่ในการเปลี่ยนชิ้นส่วนฯ ลดลง อาทิ ยางรถยนต์ และผ้าเบรก นอกจากนี้ รถยนต์ในอนาคตจะมีระบบช่วยในการขับขี่ให้ปลอดภัยมากขึ้น ซึ่งอาจช่วยลดอัตราการเกิดอุบัติเหตุ และทำให้ความต้องการชิ้นส่วนฯ REM ลดลงไปด้วย
ในระยะต่อไป รถยนต์ไฟฟ้ามีแนวโน้มทวีบทบาทมากขึ้นในอุตสาหกรรมรถยนต์ของไทย ทำให้ห่วงโซ่อุปทานของอุตสาหกรรมรถยนต์เปลี่ยนแปลงไป จากเดิมที่มีลักษณะความสัมพันธ์แบบเส้นตรง (Linear Supply Chain) ซึ่งมีการส่งผ่านการผลิตชิ้นส่วนฯ แต่ละกลุ่มต่อไปเป็นลำดับ (ภาพที่ 11) ประกอบด้วย ผู้ผลิตชิ้นส่วนฯ Tier 1 คือ ผู้ผลิตชิ้นส่วนฯ ที่มีมาตรฐานการผลิตตามที่ผู้ประกอบรถยนต์กำหนด และจัดส่งให้ผู้ประกอบยานยนต์โดยตรง ผู้ผลิตชิ้นส่วนฯ Tier 2 คือ ผู้ผลิตชิ้นส่วนประกอบเพื่อจัดส่งให้แก่ผู้ผลิต Tier 1 อาจได้รับการถ่ายทอดเทคโนโลยีจากผู้ผลิต Tier 1 และผู้ผลิตชิ้นส่วนฯ Tier 3 คือ ผู้ผลิตชิ้นส่วนย่อยเพื่อจัดส่งให้แก่ผู้ผลิตชิ้นส่วนฯ Tier 1 และ Tier 2 ทั้งนี้ ห่วงโซ่อุปทานแบบเส้นตรงจะใช้เวลาค่อนข้างนานกว่าที่คำสั่งซื้อสินค้าจะถึงต้นทางของวัตถุดิบ ผู้ผลิตชิ้นส่วนฯ จึงจำเป็นต้องสต็อกสินค้าให้เพียงพอเพื่อส่งมอบให้ทันเวลาตามคำสั่งซื้อของผู้ประกอบยานยนต์ จึงเหมาะกับการผลิต
ยานยนต์จำนวนมากเนื่องจากทำให้เกิดการประหยัดต่อขนาด (Economies of Scales) ขณะที่การผลิตรถยนต์ไฟฟ้าจำเป็นต้องพึ่งพาหุ่นยนต์และระบบการทำงานอัตโนมัติมากขึ้นเพื่อเพิ่มความแม่นยำในกระบวนการผลิต รวมถึงมีระบบเทคโนโลยีที่ทันสมัย อาทิ ระบบให้ความช่วยเหลือผู้ขับขี่ ระบบป้องกันการชนรอบด้าน ระบบควบคุมความเร็วอัตโนมัติ รวมถึงระบบเชื่อมต่ออินเตอร์เน็ตเพื่อเชื่อมโยงข้อมูลเพื่อช่วยให้การขับขี่สะดวกสบายมากขึ้น (เช่น ระบบเชื่อมต่อข้อมูลสภาพอากาศ สภาพถนน สภาพการจราจร และแผนที่การเดินทาง เป็นต้น) อีกทั้งสามารถต่อยอดไปสู่ระบบขับเคลื่อนอัตโนมัติได้ในระดับที่สูงขึ้น (ภาพที่ 12) ห่วงโซ่อุปทานรถยนต์ไฟฟ้าจึงมีลักษณะเครือข่ายแบบวงกลม (Circular Supply Chain) (ภาพที่ 13) ประกอบด้วย ผู้ผลิตชิ้นส่วนฯ และอุปกรณ์ (Auto parts Supplier) ผู้ผลิตอุปกรณ์เชื่อมต่อสัญญาณ (Device Manufactures) ผู้ให้บริการเครือข่ายโทรคมนาคม (Telecom Companies) ผู้ให้บริการระบบออนไลน์ (Online players) และผู้ให้บริการด้าน IT (IT Suppliers) ซึ่งมีความสัมพันธ์เชื่อมโยงถึงกันโดยไม่มีการแบ่งลำดับ ทำให้การผลิตมีความยืดหยุ่น รวดเร็ว และไม่จำเป็นต้องสต็อกสินค้าเป็นจำนวนมาก ทั้งยังสามารถรองรับการผลิตที่มีความหลากหลายมากขึ้น
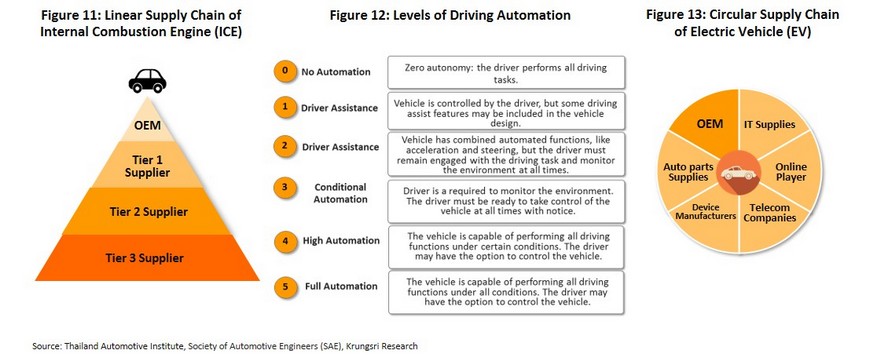
มุมมองวิจัยกรุงศรี:
ปี 2563 รายได้ของผู้ผลิตชิ้นส่วนยานยนต์มีแนวโน้มหดตัวรุนแรง ผลจากกำลังซื้อซบเซาทั้งในและต่างประเทศ ทำให้ความต้องการ ชิ้นส่วนฯ OEM ปรับลดลง อย่างไรก็ตาม อุปสงค์ชิ้นส่วนฯ REM มีแนวโน้มเติบโตต่อเนื่องตามการเพิ่มขึ้นของจำนวนรถยนต์สะสม ซึ่งจะช่วยพยุงรายได้ของผู้ประกอบการไม่ให้ทรุดหนัก สำหรับปี 2564-2565 คาดว่ารายรับของผู้ผลิตชิ้นส่วนยานยนต์จะค่อยๆ กระเตื้องขึ้น ตามการฟื้นตัวของเศรษฐกิจ
- ผู้ผลิตส่วนประกอบและชิ้นส่วนยานยนต์: ผลประกอบการปี 2563 มีแนวโน้มหดตัวแรงจากภาวะเศรษฐกิจถดถอยทั่วโลก แต่จะฟื้นตัวในปี 2564-2565 โดยความต้องการชิ้นส่วนฯ OEM จะเติบโตตามปริมาณการผลิตยานยนต์ในประเทศที่แนวโน้มขยายตัว 3-4% ต่อปี ขณะที่ตลาด REM จะเติบโตตามปริมาณยานยนต์สะสมที่เพิ่มขึ้นต่อเนื่อง อย่างไรก็ตาม ตลาดส่งออกยังมีความเสี่ยงจากข้อตกลง USMCA ที่จะยกเว้นภาษีนำเข้ารถยนต์ที่ใช้ชิ้นส่วนฯ ภายในประเทศสหรัฐฯ เม็กซิโกและแคนาดา (มีผล 1 กรกฏาคม 2563) อาจทำให้ไทยส่งออกไปยังกลุ่มประเทศดังกล่าวได้ลดลง อีกทั้งภาวะตึงเครียดทางการค้าระหว่างสหรัฐฯ และจีน อาจทำให้เศรษฐกิจประเทศคู่ค้าของไทยชะลอตัวต่อเนื่อง
- ผู้ผลิตยางรถยนต์: ผู้ประกอบการมีความเสี่ยงจากการที่สหรัฐฯ อาจใช้มาตรการตอบโต้การทุ่มตลาด ซึ่งอาจเกิดขึ้นในปี 2564 อย่างไรก็ตาม คาดว่าผู้ผลิตยางรถยนต์สัญชาติสหรัฐฯ ในไทย (ได้แก่ Goodyear และ Dunlop) อาจได้รับผลกระทบไม่มากนัก ขณะที่ผู้ผลิตสัญชาติอื่น (รวมถึงไทย) อาจเสียโอกาสส่งออกไปตลาดสหรัฐฯ ด้านตลาด REM ยังเติบโตได้ตามจำนวนรถจดทะเบียนสะสมที่เพิ่มขึ้นต่อเนื่อง
- ผู้จำหน่ายชิ้นส่วนและอุปกรณ์เสริมของยานยนต์: คาดว่ารายได้จะเติบโตตามจำนวนยานยนต์จดทะเบียนสะสม อย่างไรก็ดี ธุรกิจเผชิญภาวะการแข่งขันที่รุนแรงและความเสี่ยงจากการบริหารจัดการสต็อก
- ผู้ขายส่ง/ขายปลีกชิ้นส่วนและอุปกรณ์เสริมใหม่ของยานยนต์: คาดว่าความต้องการชิ้นส่วน/อะไหล่กลุ่มประดับยนต์และชิ้นส่วนฯ ประเภทที่มีอายุการใช้งานสั้นจะเติบโตตามยอดขายยานยนต์ใหม่ ขณะที่จำนวนยานยนต์สะสมที่เพิ่มขึ้นจะหนุนความต้องการใช้ชิ้นส่วนฯ เพื่อซ่อมแซม/บำรุงรักษาตามอายุการใช้งาน อย่างไรก็ตาม ผู้ประกอบการที่มีอยู่มากรายจะทำให้การแข่งขันด้านราคาค่อนข้างรุนแรง
- ผู้จำหน่ายชิ้นส่วนและอุปกรณ์เสริมเก่าของยานยนต์ (เซียงกง): มีแนวโน้มเติบโตต่อเนื่องตามจำนวนยานยนต์จดทะเบียนสะสม โดยเฉพาะยานยนต์ที่มีอายุมากกว่า 5 ปี ซึ่งเป็นกลุ่มเป้าหมายที่มีความต้องการใช้ชิ้นส่วนฯ เก่าเพื่อการซ่อมแซม/บำรุงรักษา อย่างไรก็ตาม ลักษณะธุรกิจที่มีการลงทุนค่อนข้างสูงในการสต็อกสินค้าที่หลากหลาย อาจมีความเสี่ยงจากการเสื่อมมูลค่าของสินค้าที่ล้าสมัยและต้นทุนจากการบริหารจัดการสต็อก
[1] การพัฒนาอุตสาหกรรมการผลิตยานยนต์ในไทยช่วงแรกยังมีการนำเข้าชิ้นส่วนครบชุดสมบูรณ์ (Complete Knock-Down: CKD) จากบริษัทแม่หรือผู้ผลิตชิ้นส่วนฯ ในเครือบริษัทยานยนต์ข้ามชาติ เพื่อประกอบเป็นยานยนต์ สำเร็จรูป (Complete Built-Up: CBU)
[2] องค์การการค้าโลก (WTO) ห้ามประเทศสมาชิก (รวมไทย) กำหนดสัดส่วนการใช้วัตถุดิบในประเทศเป็นการเฉพาะ ส่งผลให้รัฐบาลไทยยกเลิกข้อกำหนดดังกล่าวตั้งแต่ 1 มกราคม 2543
[3] การผลิตเครื่องยนต์ใช้ชิ้นส่วนฯ หรือส่วนประกอบมากกว่า 2,000 ชิ้น
[4] ทั้งด้านการประกอบรถยนต์และการผลิตชิ้นส่วนสำคัญ ประกอบด้วย แบตเตอรี่สำหรับยานยนต์ไฟฟ้า, Traction Motor, ระบบปรับอากาศด้วยระบบไฟฟ้าและส่วนประกอบ, ระบบบริหารจัดการแบตเตอรี่, ระบบควบคุมการขับขี่, On-Board Charger, สายชาร์จแบตเตอรี่พร้อมเต้ารับ-เต้าเสียบ, DC/DC Converter, Inverter, Portable Electric Vehicle Charger, Electrical Circuit Breaker, คานหน้า/คานหลังสำหรับรถโดยสารไฟฟ้า และกิจการพัฒนาระบบอัดประจุไฟฟ้าอัจฉริยะ (EV Smart Charging System)
[5] ผู้เข้าร่วมโครงการขอรับส่งเสริมการลงทุนผลิตรถยนต์ไฟฟ้าและชิ้นส่วนฯ (ข้อมูลล่าสุด ณ พ.ค. 63) มีดังนี้ รถยนต์ไฮบริด (Hybrid Electric Vehicle: HEVs) ได้แก่ Toyota, Honda, Mazda, Nissan, Suzuki รถยนต์ไฟฟ้าปลั๊กอินไฮบริด (Plug-In Hybrid Electric Vehicle: PHEVs) ได้แก่ Mercedes-Benz, BMW, Toyota, Mitsubishi, MG, และ Audi รถยนต์ไฟฟ้าแบตเตอรี่ (Battery Electric Vehicle: BEVs) ได้แก่ Mercedes-Benz, MG, FOMM, Mine, Toyota, Honda, Audi, Mitsubishi, Nissan, Sky well, Takano Auto และ
ทรัพย์ละออ แบตเตอรี่สำหรับรถยนต์ไฟฟ้า อาทิ Toyota, Honda, Mercedes-Benz, BMW, Global Power Synergy
[6] อ้างอิงจากบทวิเคราะห์ของสถาบันวิจัย ADB Institute เรื่อง “Thailand’s Economic Integration with Neighboring Countries and Possible Connectivity with South Asia”
[7] “โครงการช้อปช่วยชาติ” กำหนดให้บุคคลธรรมดานำค่าใช้จ่ายซื้อสินค้าในช่วง 15 ธันวาคม 2561 ถึง 16 มกราคม 2562 ได้แก่ ยางยานพาหนะ (เฉพาะผู้ผลิตที่ซื้อวัตถุดิบยางพาราจากการยางแห่งประเทศไทยในช่วง 1 ธันวาคม 2561 ถึง 16 มกราคม 2562) หนังสือและสินค้าโอทอป มาหักลดหย่อนภาษีตามจำนวนที่จ่ายจริงแต่ไม่เกิน 15,000 บาทภายใน 2 ปีภาษี
[8] ไทยมีสัดส่วนการนำเข้าชิ้นส่วนฯ จากจีนเพิ่มขึ้นอย่างก้าวกระโดด จาก 5.3% ของมูลค่านำเข้าชิ้นส่วนฯ ทั้งหมดในปี 2550 เป็น 17.2% ในปี 2562
[9] ประเทศที่เป็นฐานการผลิตรถยนต์สัญชาติญี่ปุ่นในอาเซียน ได้แก่ อินโดนีเซีย ฟิลิปปินส์ มาเลเซีย และเวียดนาม
[10] ผู้ผลิตยางยานพาหนะสัญชาติจีนที่เข้ามาลงทุนในไทย อาทิ Hang Zhou Zhong Ce Rubber, Shandong Linglong Tire, Sentury Tire, Huayi Group (ภายใต้แบรนด์ ‘Double Coin’ และ ‘Strong Man’), Dadi Group (ภายใต้แบรนด์ ‘Shenzhou’ brand) เป็นต้น หลังสหรัฐฯ ขึ้นภาษีตอบโต้การทุ่มตลาดยางรถยนต์นั่งส่วนบุคคล และยางรถบรรทุกขนาดเล็กที่นำเข้าจากจีนเป็นเวลา 3 ปี (ตั้งแต่ 26 กันยายน 2552 ถึง 25 กันยายน 2555) โดยอัตราภาษีอยู่ที่ 35% ในปีที่ 1 อัตรา 30% ในปีที่ 2 และ 25% ในปีที่ 3 จากเดิมอยู่ที่ 3.4-4.0%
ทั้งนี้ สหรัฐฯ ปรับขึ้นภาษีนำเข้ายางรถยนตต์จากจีนอีกครั้งเมื่อ 24 กันยายน 2561 ในอัตรา 10% และเพิ่มขึ้นเป็น 25% ในวันที่ 1 มกราคม 2562
[11] ไทยยังเป็นฐานการผลิตชิ้นส่วนยานยนต์หลักในภูมิภาคอาเซียนของค่ายรถญี่ปุ่น เพื่อนำไปผลิตต่อในอุตสาหกรรมประกอบยานยนต์ในประเทศเพื่อนบ้าน แม้ค่ายรถญี่ปุ่นมีนโยบาย “Thailand-Plus-One” เพื่อกระจายการลงทุนไปยังประเทศอื่นๆ ในอาเซียนควบคู่กับไทย อาทิ อินโดนีเซีย (ฐานผลิตรถยนต์) และเวียดนาม (ฐานผลิตรถจักรยานยนต์)
[12] กระทรวงพลังงานและสถาบันวิทยสิริเมธี (วิสเทค) ร่วมกันวิจัยแบตเตอรี่สำหรับรถยนต์ไฟฟ้า และอุปกรณ์กักเก็บไฟฟ้าในโรงไฟฟ้าพลังงาแสงอาทิตย์ โดยใช้งบประมาณจากกองทุนเพื่อส่งเสริมการอนุรักษ์พลังงาน 180 ล้านบาท ได้คิดค้นแบตเตอรี่ลิเทียมซัลเฟอร์ซึ่งเป็นสิทธิบัตรของวิสเทค สามารถเก็บไฟฟ้าได้มากกว่าแบตเตอรี่ลิเทียมไอออนถึง 3-5 เท่า น้ำหนักเบากว่า และสามารถวิ่งได้ระยะทาง 800 กม./การชาร์จ 1 ครั้ง เทียบกับแบตเตอรี่ลิเทียมไอออนที่วิ่งได้ 400-500 กม./การชาร์จ 1 ครั้ง และราคาถูกลงเนื่องจากต้นทุนแร่ซัลเฟอร์ถูกกว่าแร่ลิเทียมเกือบ 200 เท่า แต่มีอายุการใช้งานเพียง 2-3 ปี เทียบกับแบตฯ ลิเทียมไอออนซึ่งมีอายุการใช้งาน 10 ปี วิสเทคคาดว่าจะผลิตแบตฯ แบบใหม่ในเชิงพาณิชย์ได้ประมาณปี 2564-2565
[13] Bloomberg ประเมินว่า ราคารถยนต์ไฟฟ้าแบบแบตเตอรี่ (BEV) จะใกล้เคียงกับรถยนต์เครื่องยนต์สันดาปภายใน (ICE) เมื่อราคาแบตเตอรี่ลิเทียมไอออนอยู่ที่ระดับ 125 USD/kWh