EXECUTIVE SUMMARY
Demand for construction materials tends to slump through 2024 due to delays in the approval and disbursement of the fiscal budget, which has then held up progress on both megaprojects and general work on public utilities and infrastructure around the country. At the same time, work on private sector residential and commercial developments has been impacted by only weak growth in purchasing power, the run-up in the cost of living, and the recent high interest rates. The total market for construction materials is thus expected to contract by between -2.0% and -3.0% across the year. However, an uptick in spending on public sector construction and a brighter outlook for the economy will then boost the pace of work on both new private sector projects and repairs and renovations, and this should feed through into growth of 4.5-5.0% in 2025 and then of 5.0-5.5% in 2026.
Given this, manufacturers and distributors of construction materials will have to endure a poor outlook for 2024, but as demand is expected to record growth in 2025 and 2026, incomes will grow again. Going forward, major manufacturers will compete to invest in the advanced production technologies needed to cut their greenhouse gas emissions and meet the ESG goals. Distributors will increasingly adapt to the changing needs of digital consumers by leaning more heavily on online distribution channels. Nevertheless, manufacturers and distributors will likely face higher energy and transport costs, and increased pressure on sales due to low-cost imports that will come especially from China and Vietnam.
Krungsri Research view
Continuing weakness in consumer spending power and delays to work on government infrastructure projects will drag on the industry through 2024, but over 2025 and 2026, the outlook for the construction will improve thanks to: (i) an expansion in public sector construction in both Thailand and neighboring countries, especially for work on megaprojects; (ii) an acceleration in work on real estate developments, particularly in the Bangkok Metropolitan Region and in provincial centers; and (iii) a stronger outlook for the economy that will lift incomes and boost demand for the repair and renovation of residential properties.
Producers of construction materials:
-
Cement: Income growth will be depressed through 2024 but an expected increase in spending on construction in 2025 and 2026 will lift incomes, while some manufacturers will also look to move beyond their traditional export targets of the CLM countries by breaking into new markets in Australia and New Zealand
-
Construction steel (bar & section): Receipts will fall in 2024, and although these will recover in 2025, growth will remain limited due to pressure from low-cost imports from China and Vietnam.
-
Ceramic tile and sanitary ware: As with other segments, income will soften in 2024, but a rebound in real estate markets, especially for residential properties, should then drive recovery in sales. Nevertheless, the large backlog of unsold housing stock, the tightening of credit conditions by lenders (in particular for low- and middle-income borrowers) and competition with cheap Chinese imports will mean that growth will remain anemic.
Traders of construction materials:
-
Modern traders: Income will grow gradually, helped by: (i) improving spending on construction and overall economic outlook; (ii) an expansion in the reach of branch networks and an increasing reliance on using online platforms to distribute goods; (iii) growth in the number of house brand products that are on sale; and (iv) consumers’ increasing preference for shops that carry a wide and comprehensive range of choices and that offer after-sales services such as home repairs, renovations and extensions.
-
Traditional traders: For traditional wholesalers, although income will expand due to an increase in construction-related activity across the country, players will face obstacles in the form of rising competition from modern trade outlets and manufacturers selling directly to their customers. For traditional retailers, income will remain flat, although sales from these are generally of home decorations or goods used in home repairs and extensions, and these product categories may see some growth.
Overview
Construction supplies are a crucially important upstream component of the construction and real estate sectors, and because some 60% of all construction costs are for materials (Input-Output Table, 2015), the outlook for the construction supplies industry tends to move with these in a coordinated fashion (Figure 1). The most important product groups can be split into building materials (e.g., cement and construction steel), which account for 40% of the market for all construction materials, and home decorations (e.g., ceramic tile and sanitary ware), which represent another 10% of the market (Figure 2). With the exception of sanitary wares, sales of the main product categories are mostly into the domestic market (Figure 3).
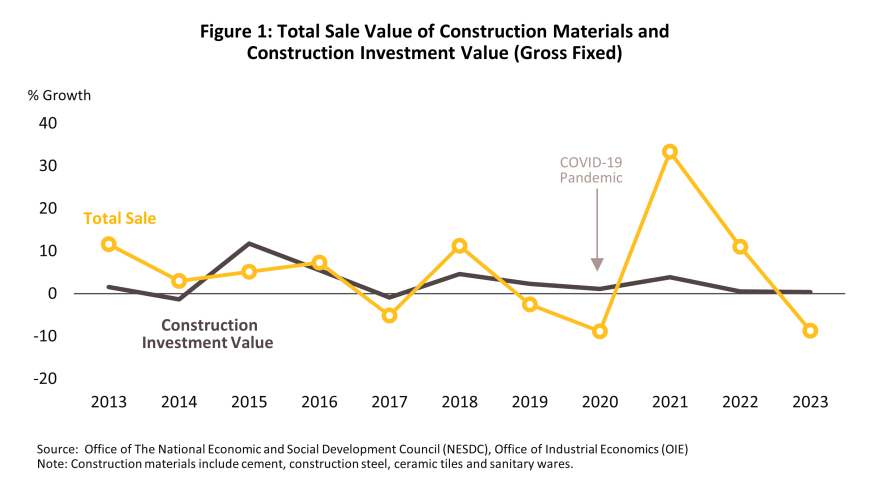

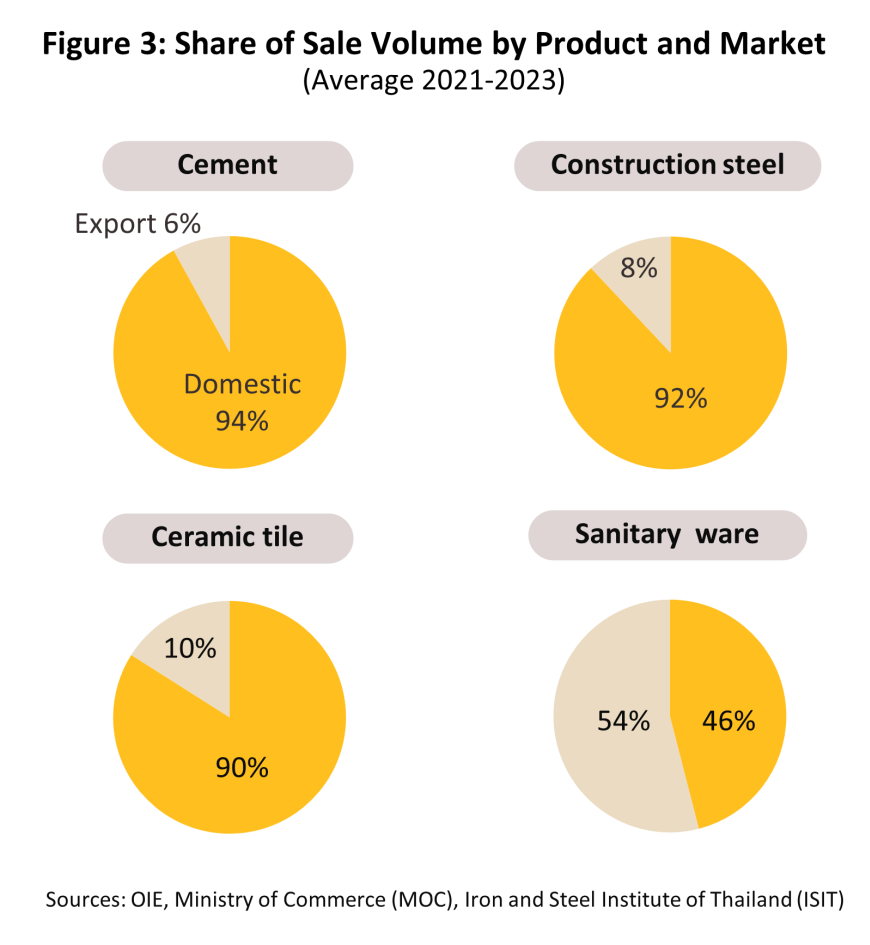
Industry structure
-
Producers: According to 2023 data, there were some 801 mid- and large-sized operators1/ registered in Thailand that were active in the construction materials industry. These enjoy advantages relative too smaller players in virtue of their stronger financial base, their better management of production processes, and their favorable bargaining position relative to suppliers with regard to, for example, price and deliveries of inputs. This then allows these players to mass produce goods more efficiently, which in turn generates economies of scale. In contrast, smaller operators, of which there were 2,153 players in the country, tend to be on a weaker financial footing and this then forces these to produce goods in smaller production runs, adding to marginal manufacturing costs. The structure of the manufacturing side of the industry is summarized in Table 1 below.
-
Traders: As of 2023, Thailand was home to 7,303 distributors of construction materials1/, split between 280 large players, 1,172 mid-sized operators, and 5,851 small companies. These can be further categorized according to the characteristics of each business.
-
Modern Traders are notable for their use of comprehensive management systems across their businesses, from sales floor to back-office services. These operations stock a wide range of construction materials and related goods under a single roof, and these generally cover the complete spread of consumer and trade needs, from basic construction materials through to home repairs, decorations and furniture. Players are generally medium- or large-scale operations, and these have advantages in terms of their capital base and their lower operating costs. Many of these are now in the process of expanding their customer bases in the provinces by extending their upcountry branch networks. One favored strategy for increasing contact points with customers is by offering after-sales services, such as those for home repair and the installation of appliances in and outside the home. Within Thailand, five large players dominate the market and as of 2023, these had a combined 31% share of all income going to retailers of construction materials. These are: The HomePro group (HomePro shops themselves are more oriented towards retail and home decorations, while MegaHome is focused on the wholesale and trade market), Thai Watsadu, Siam Global House, Dohome, and the Boonthavorn Group.
-
Traditional traders are operators in the construction sector using more old-fashioned management systems. Their operations emphasize the distribution of basic building materials, such as cement, sand and hardware (e.g., locks, nails, etc.) together with materials used in home repairs and decoration, and this is targeted at meeting consumer demand within the local area. However, in the face of rising competition from modern trade outlets, some players are also now beginning to raise their competitiveness by modernizing their operations and offering a more comprehensive set of services. This extends to giving their customers a wider range of choices that includes not just building materials but also home decorations, renovating their premises, using alternative distribution channels (especially by increasing their online presence), putting in place modern stock control systems, and offering organized delivery services. Nevertheless, traditional players remain at a disadvantage relative to modern trade outlets with regard to their finances, marketing, and the strength of their brand.
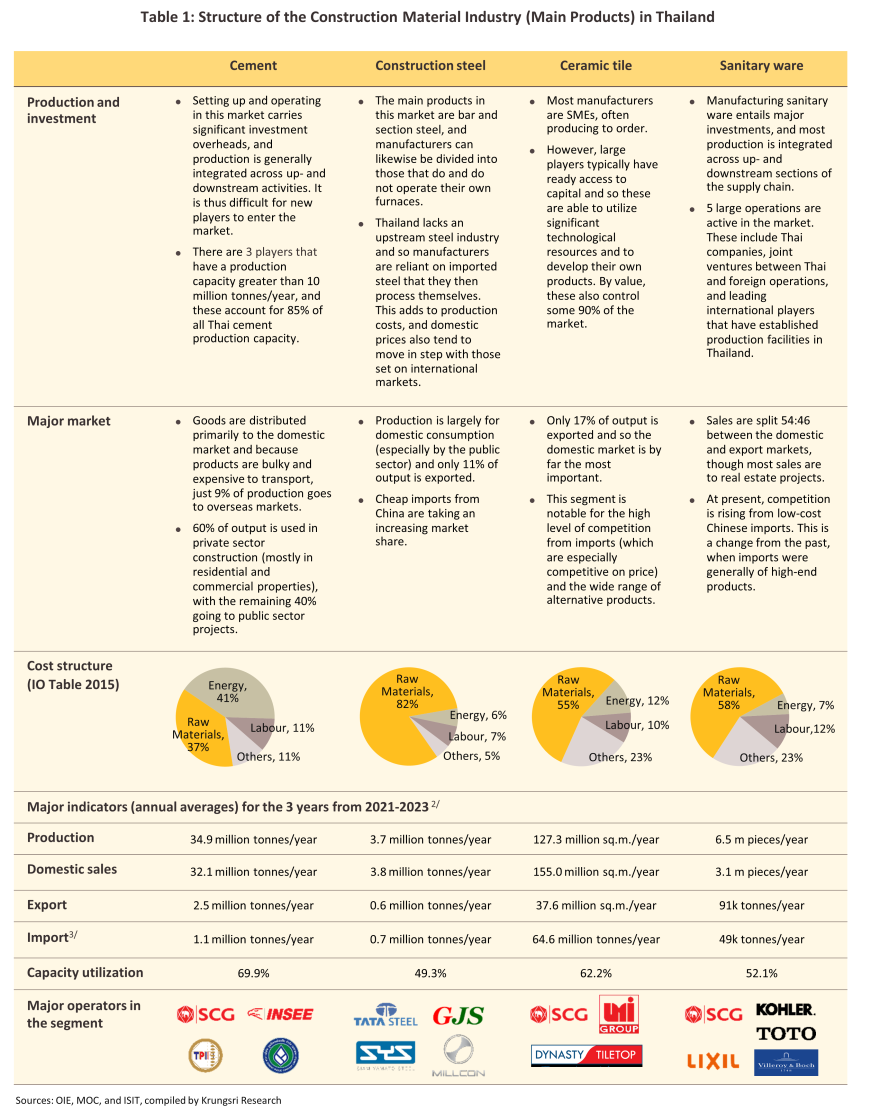
Situation
Producer
In 2023, depressed conditions in the construction sector undercut production and distribution in almost all the main product categories. This was principally the result of the only slow progress that was made on government infrastructure projects, which was itself a consequence of delays to the establishment of the new government and the start of budget disbursements. In addition, the private sector real estate market saw only relatively low levels of growth, and so overall spending on construction expanded by just 0.4% in the year, split between a -2.2% contraction in public sector investment and growth of 3.9% in private sector spending. Alongside this, exports also slipped4/ on the weaker economic outlook in core export markets, which then left importers with significant inventories of construction materials.
-
Cement
-
Production (portland and mixed cement) dropped -2.4% to 33.8 million tonnes, thus extending 2022’s -4.3% decline. Domestic sales also slipped, and having fallen -4.1% in 2022, this declined by another -2.5% to 31.1 million tonnes (Figure 4). Declines were driven by: (i) depressed demand, which was undercut by the drop-off in public sector construction work; and (ii) the run-up in energy prices, which then added to manufacturing and transportation costs.
-
Exports (not including clinker) slumped -21.8% by volume and -13.3% by value to totals of 1.7 million tonnes and THB 4.1 billion. Sales to Myanmar (mostly of Portland cement and comprising 49% of all Thai cement exports) dropped -8.9% as a result of the country’s ongoing political troubles and the impacts of this on both government and private sector construction projects (Figure 5). Exports to Cambodia (17% of the total) also crashed -43.1% on continuing weakness in the real estate sector. Export to Lao PDR (22% of all cement exports) jumped 66.1% on strong investment in SEZs across the country despite continuing risk factors on economy that include a fall in the value of the kip to a 20-year low, a public debt crisis, and rampant inflation.
-
In recent years, cement producers have begun to move the industry onto a more sustainable footing by investing in the development of new technology, including the production of hydraulic cement. Because production of the latter uses eco-friendly materials in place of clinker5/, this helps to cut CO2 emissions, and since hydraulic cement can be used instead of clinker-intensive portland cement, its widespread uptake has the potential to help make significant inroads into reducing construction-related carbon emissions (Figure 6). Over the past few years, Thai manufacturers have thus been stepping up production of this for distribution to both domestic and export markets (Figure 7). Players have also been experimenting with the use of biomass-derived energy in place of the coal that the industry has traditionally relied on, for example in trials using Napier grass that have been carried out in the Saraburi Sandbox6/.
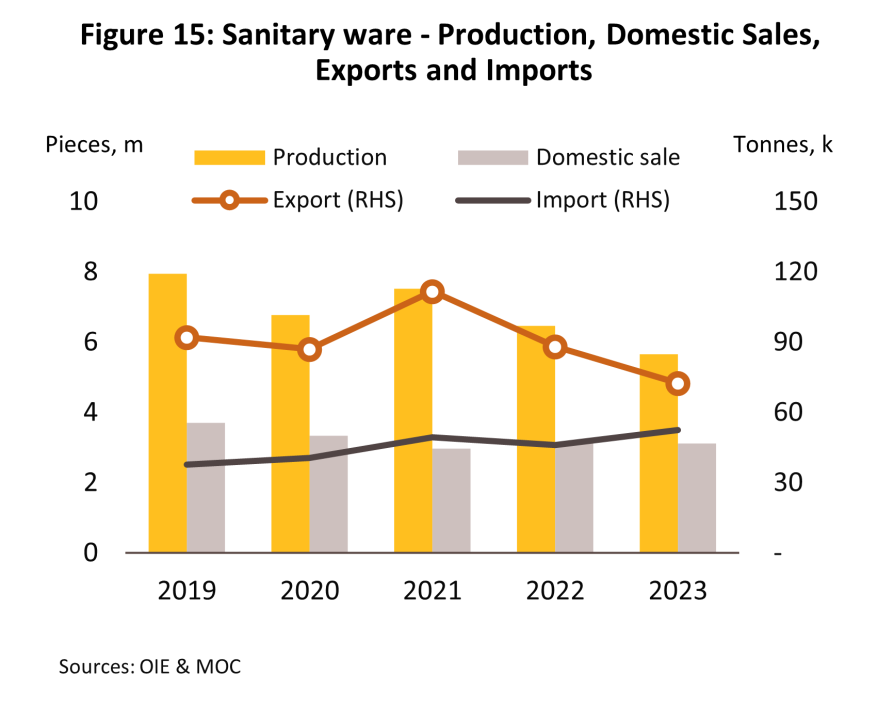
Construction Materials Price Index
The Construction Materials Price Index (CMPI) inched up 0.1% in the year, having risen 5.8% a year earlier. The index of construction steel prices (29% of the CMPI weighting) slipped -3.6% on delays to government budget disbursements that then disrupted work on building projects (Figure 16). Steel prices were also affected by the real estate crisis in China, which badly impacted domestic demand and forced Chinese producers to dump low-cost products on markets in Southeast Asia, and as such, both domestic and international steel prices came under pressure (Figure 17). However, the higher cost of inputs, in particular the 5.0% increase in the cost of gypsum, fed through into price rises for cement and concrete products (respectively 17% and 12% of the CMPI weighting) of 1.9% and 1.4% each. In particular, prices rose for ready-mixed concrete, lean concrete and concrete drainage pipes.
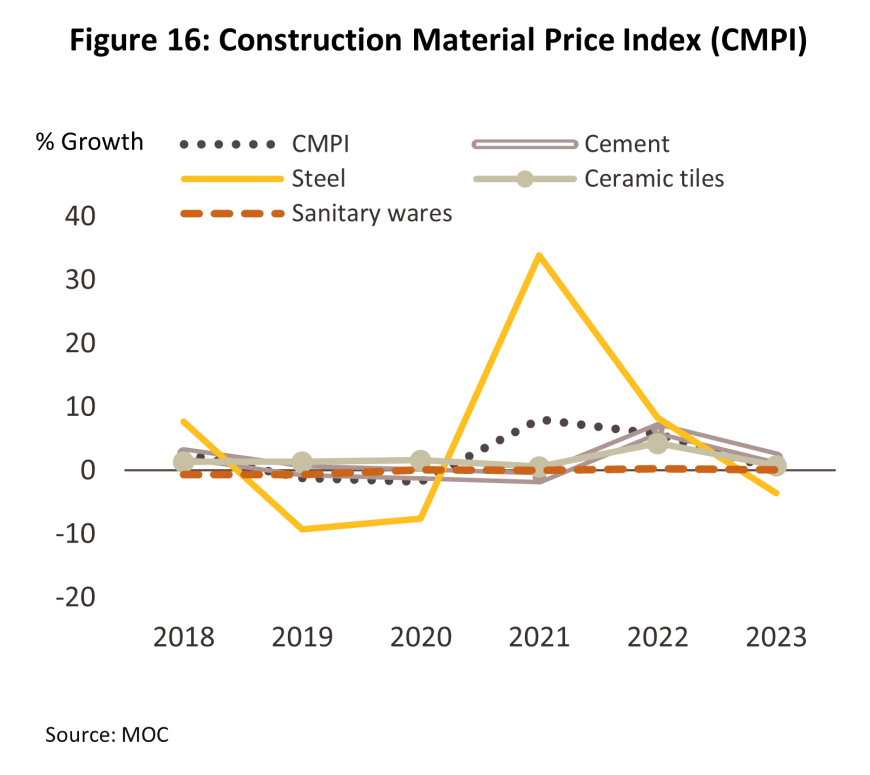
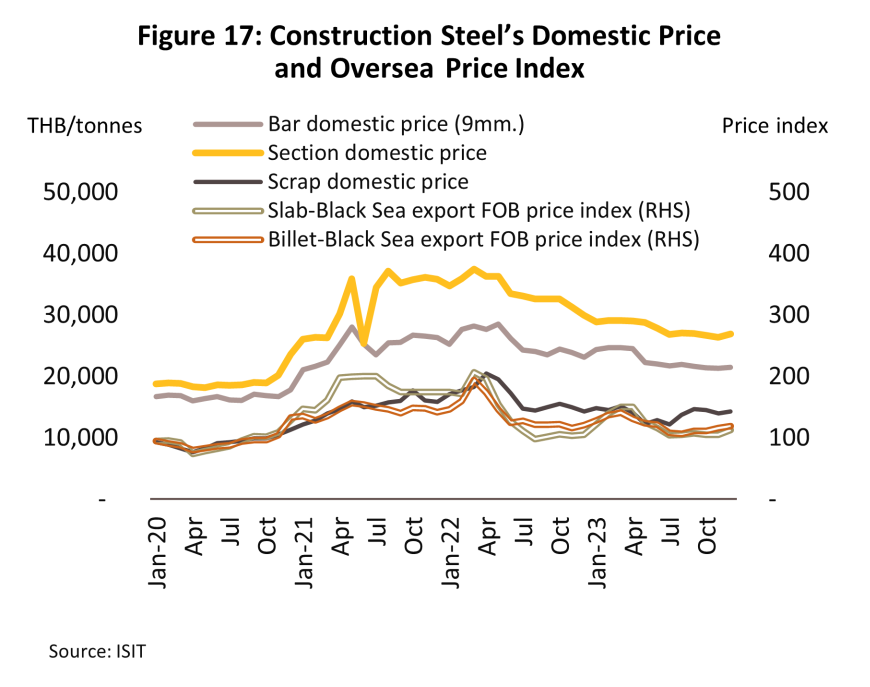
Situation in 1H24
Spending on construction contracted -11.2% YoY in 1H24 due to the delayed passing of the 2024 budget, which then triggered a -19.3% YoY slump in government spending, though this especially affected work on infrastructure megaprojects (down -23.2% YoY). This came despite the 1.2% increase in private-sector investment in non-residential properties (overall private-sector spending on construction rose 6.7% YoY) and so demand for construction materials remained depressed through the first half of the year.
-
Producer
-
Domestic sales: Over 1H24, sales of cement and construction steel fell by -12.2% YoY and -15.6% YoY respectively, while manufacturers and suppliers of tile and sanitary ware had to endure declines of -8.8% YoY and -11.1% YoY. Demand for construction materials was hurt by the rise in the cost of living and overall sluggishness in the economy. This then drained purchasing power from the markets for new homes (in particular for properties targeted at low- to middle-income buyers) and home renovations and improvements, and so in the period, overall private sector investment in residential accommodation dropped by -3.2% YoY, down from a 3.6% YoY expansion in 1H23. Alongside this, government spending on construction also remained very subdued.
-
Exports: Exports of most product categories softened in the period. For cement, overseas sales contracted -6.2% YoY to 0.82 million tonnes due to the continuing weakness of the Myanmar market (the source of 42% of export orders), where continuing political upheaval translated into a -17.8% YoY drop in sales. However, this was partly offset by the 81.5% YoY surge in exports of cement to Lao PDR (with a 33% market share by volume, Thailand’s second most important export target). Exports of tile and sanitary ware were also down by -14.9% YoY and -11.2% YoY (Table 2), again as a result of weaker demand from Myanmar that led to falls in sales of tiles and sanitary ware to the country of respectively -26.9% YoY and -41.1% YoY. Nevertheless, overseas sales of construction steel jumped 35.4% YoY in the period. Exports of steel bar were up 74.1% YoY to 0.17 million tonnes on firmer demand from buyers in the main markets of Canada, Lao PDR and Australia, while the strength of the Singaporean and Australian markets boosted exports of steel section by 12.2% YoY.
-
Imports: The depressed state of the construction industry weighed on imports, and so for construction steel, total import fell by -21.5% YoY because import from China contracted -38.3% YoY. However, while total imports of ceramic tile declined -0.3% YoY, imports from China rose 7.3%. Similarly, efforts by Chinese producers to run down their inventories led to a 5.4% YoY increase in imports of Chinese sanitary ware, and this then helped to lift overall imports of these by 6.5% YoY.
-
The Construction Materials Price Index fell back -0.7 % YoY on declines in prices in all the main product categories. Thus, with supply from China expanding, prices for steel and steel products were down -2.8% YoY, the stabilizing cost of coal helped to bring prices for cement goods down by -0.3% YoY, and prices for tile and sanitary ware softened by -0.1% YoY and -3.2% YoY on a combination of sluggishness in domestic residential property markets and the rise in interest rates.
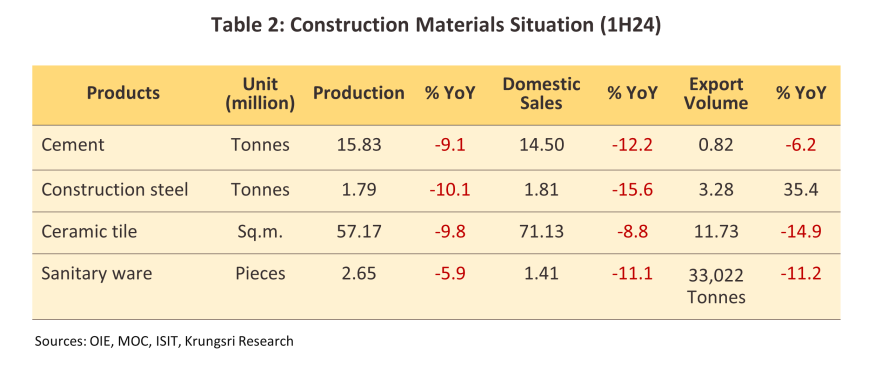
Outlook
Demand for construction materials is likely to contract through 2024. On the public sector side of the market, the delayed passing of the fiscal budget and the ensuing interruptions to disbursements have held up work on both megaprojects and general work on infrastructure and utilities around the country. Meanwhile, in the private sector, the increasing cost of living, the recent decade-high interest rates, and the slow and uneven growth in spending power have together dragged on both the residential and commercial property segments. Overall spending on construction is therefore forecast to slip by between -2.0% and -3.0% this year, though this should then rebound to growth of 4.5-5.0% in 2025 and 5.0-5.5% in 2026 as government funding flows back into the industry and consumer spending power rallies, thereby adding to demand for new housing developments and the repair and renovation of existing properties (Figure 18). This will naturally then provide a lift to sales of construction materials, although both producers and traders of these will remain exposed to risk arising from higher energy and transportation costs, and from increased pressure from imports of low-cost Chinese and Vietnamese goods.
Producers of construction materials: Overall income to the industry will decline in 2024 in line with reduced spending on construction. However, this will return to growth in 2025-2026 as the timetables set out in the Ministry of Transport’s Action Plan on Thailand Logistics Development for 2023-2027 come closer into view. This covers 77 projects with a budget of THB 337.8 billion, and so work on these both in the EEC and elsewhere in the country will accelerate. Progress on other megaprojects will also help to crowd in greater private-sector investment in construction in 2025 and 2026, though this will especially impact residential developments along metro lines and other new transport and logistic links, as well as factories and industrial estates in nearby areas.
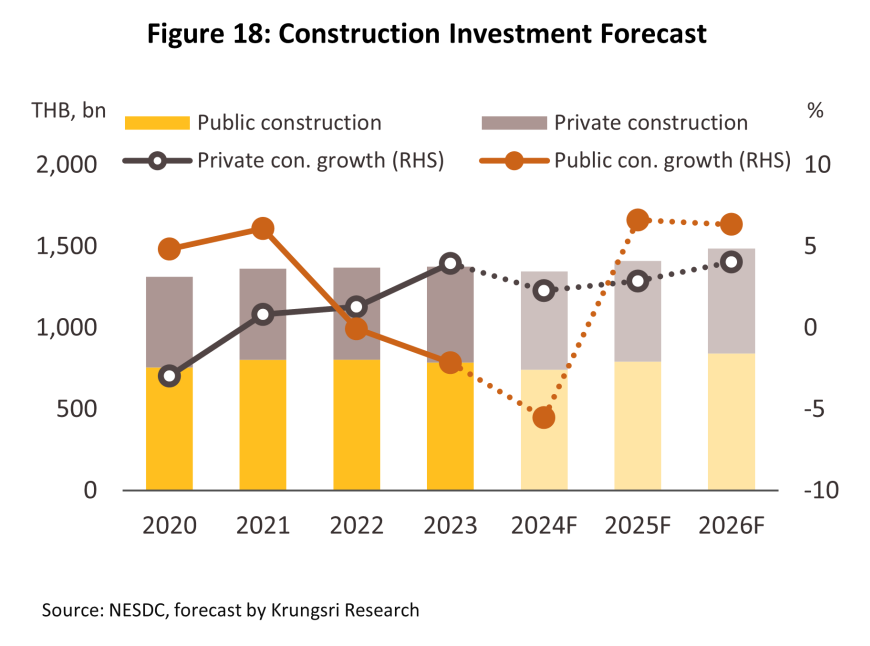
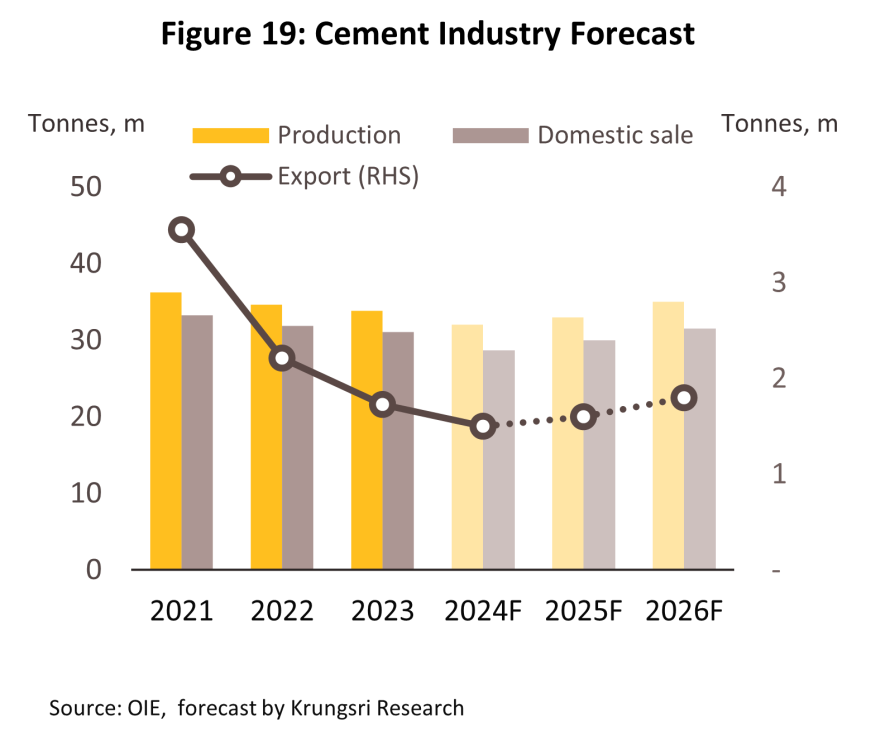
-
Cement: The quantity of domestic sales will slip by between -7.0% and -8.0% in 2024 but greater progress on infrastructure projects will bring this back to growth of 4.5-5.0% in 2025 and 2026 (Figure 19). Businesses will benefit from the increased demand for cement for use in the initial stages of construction, for example when building the new roads that will link to the EEC and laying the foundations for elevated metro lines. Exports will also remain depressed in 2024, but with the International Monetary Fund forecasting growth for the CLMV countries and the Philippines (Thailand’s five most important overseas markets for white Portland cement), rising investment and strengthening economies will lift work on infrastructure and real estate projects, and so exports will strengthen in 2025 and 2026. Players will also look to diversify export sales and reduce risk by breaking into new markets in Australia and New Zealand.
-
Construction steel (bar and section): Domestic sales will fall by -11.0% to -12.0% in 2024 before strengthening investment in public-sector infrastructure and private-sector property developments returns this to growth of 4.0-5.0% annually through the following two years (Figure 20). Exports will also strengthen steadily, helped by the post-COVID uptick in infrastructure investment seen in many countries, though given their status as major export targets for Thai producers, the likely increase in spending in the ASEAN nations will be especially important. This is in line with Worldsteel’s forecast that having grown 1.1% in 2023, demand for steel across the ASEAN zone will rise by 3.5% in 2024 and 4.3% in 2025 (Worldsteel, April 2024) (Figure 21). Likewise, imports will increase in step with stronger investment and growth in the construction sector, but overall, the Thai steel industry is coming under pressure from the broadening of supply to global markets, especially from Chinese players, against whom Thai producers are at a disadvantage with regard to their production costs and access to upstream inputs. Given this, capacity utilization is slipping, having fallen to just 29.3% over 1H24 (Federation of Thai Industries, August 2024).
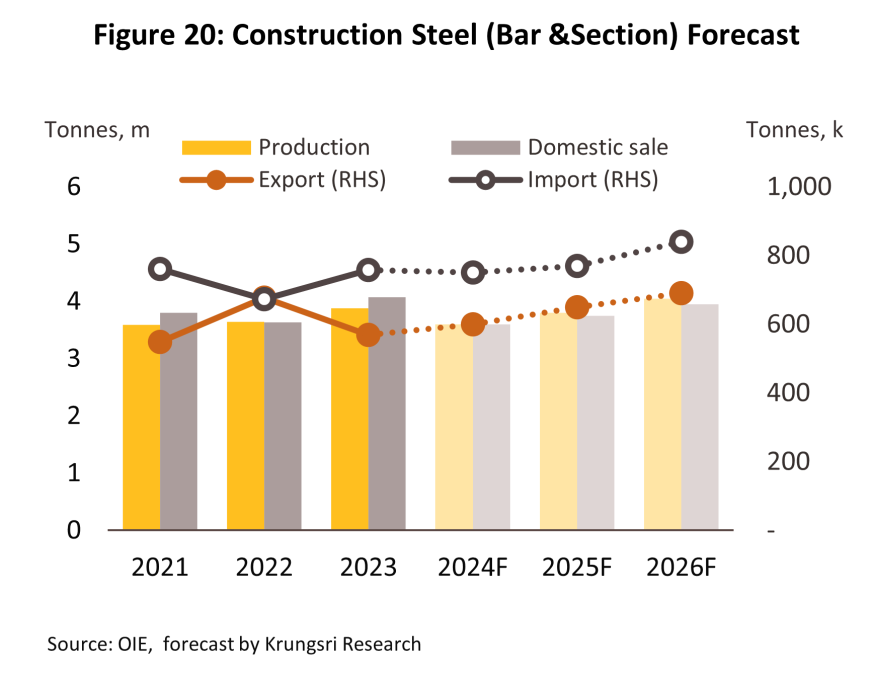
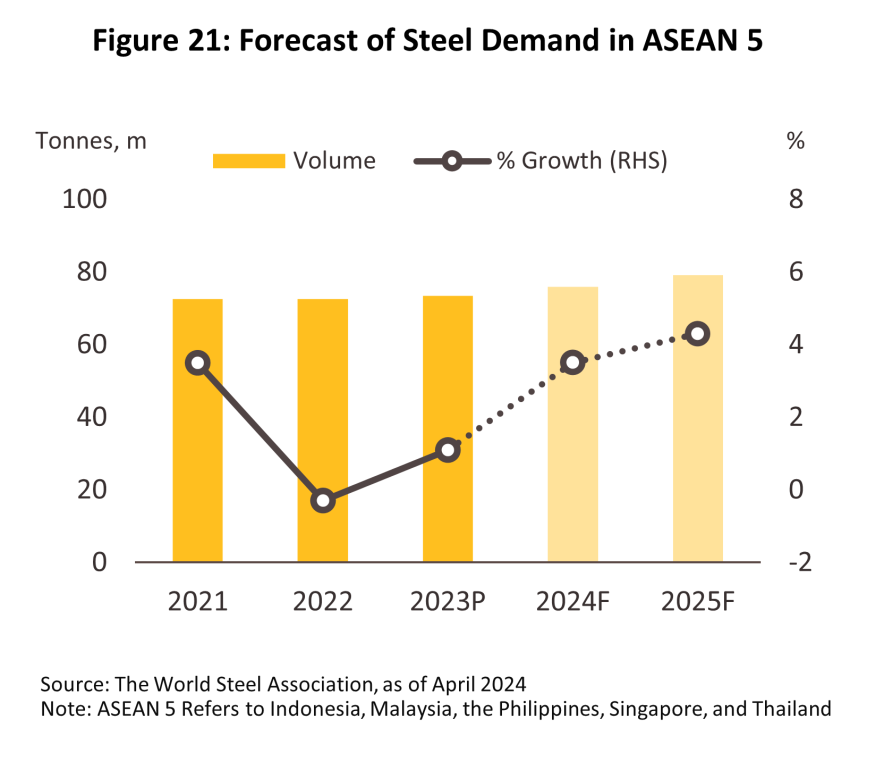
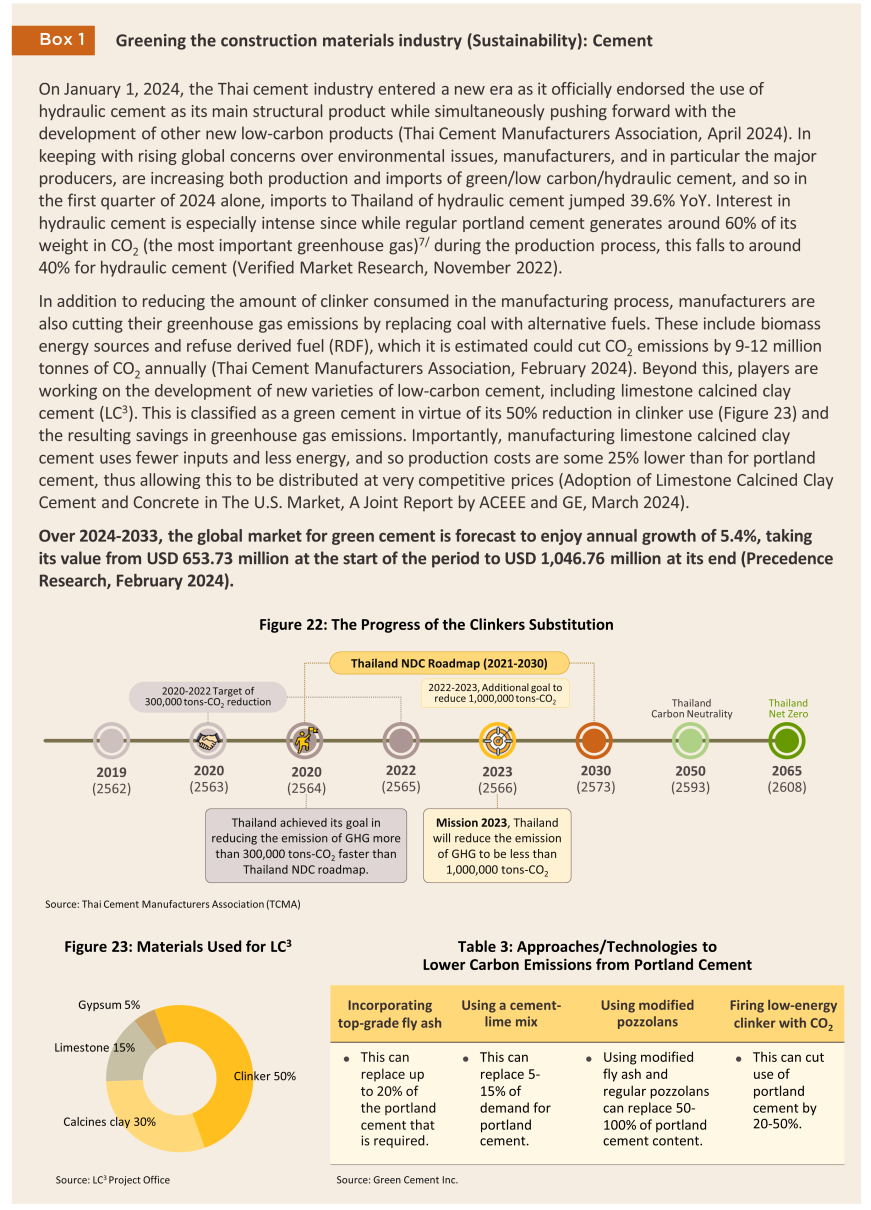
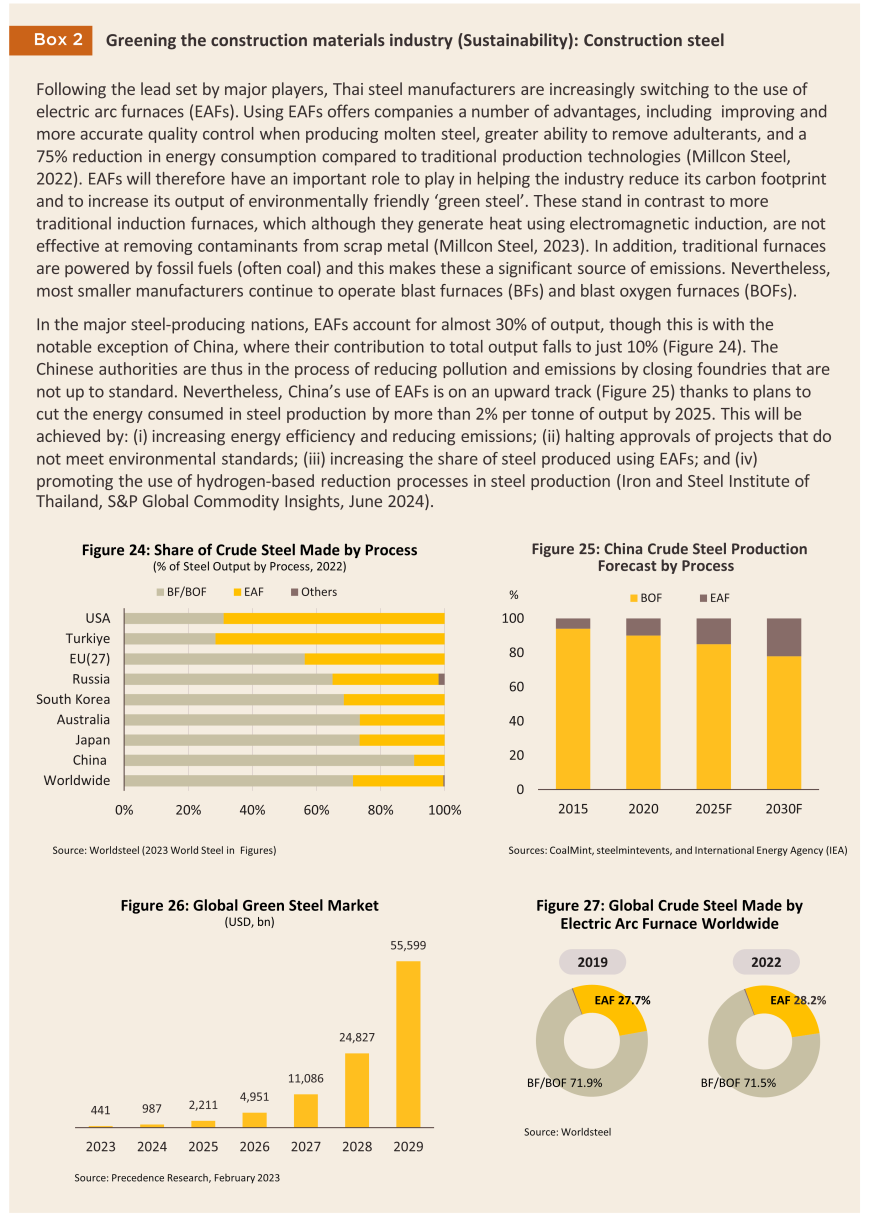
-
Ceramic tile and sanitary ware: The domestic market will remain depressed through 2024, and the quantity of tile and sanitary ware distributed to it is forecast to contract by between -8.0% and -9.0% in the year. However, an improving outlook for the economy and the ongoing recovery in the tourism sector (arrivals are forecast to return to their pre-COVID level in 2025) will lift consumer spending power and boost investment in residential and commercial properties including offices, hotels, and other types of accommodation. Given this, sales are expected to grow by 1.0%-2.0% over 2025 and 2026 (Figure 28 and Figure 29) as domestic real estate markets firm up. Similarly, exports of tile and sanitary ware will slump by -11.0% to -12.0% in 2024 before swinging back to growth of 2.0%-3.0% annually over 2025-2026, driven in particular by the strength of the Laotian and Cambodian markets. Data from 2021 (the latest available) show that Thailand accounted for respectively 40% and 50% of all imports of tiles and sanitary ware to Lao PDR due to the post-pandemic recovery in the real estate sector. At the same time, imports of tile and sanitary ware are expected to increase by respectively 1.5% and 1.2% per year as residential, commercial, and industrial real estate markets improve. These goods will largely be imported from China and Vietnam.
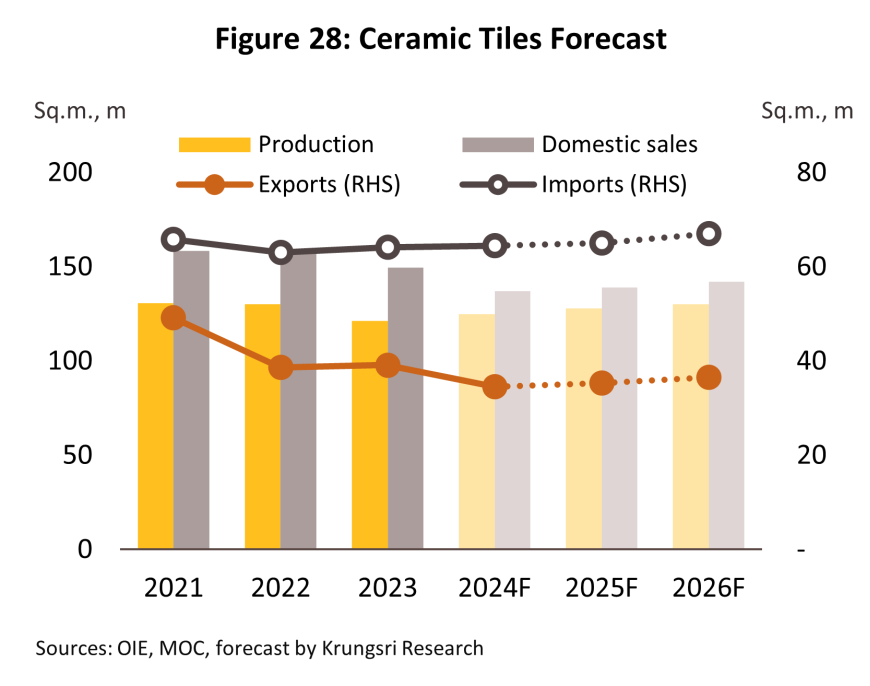
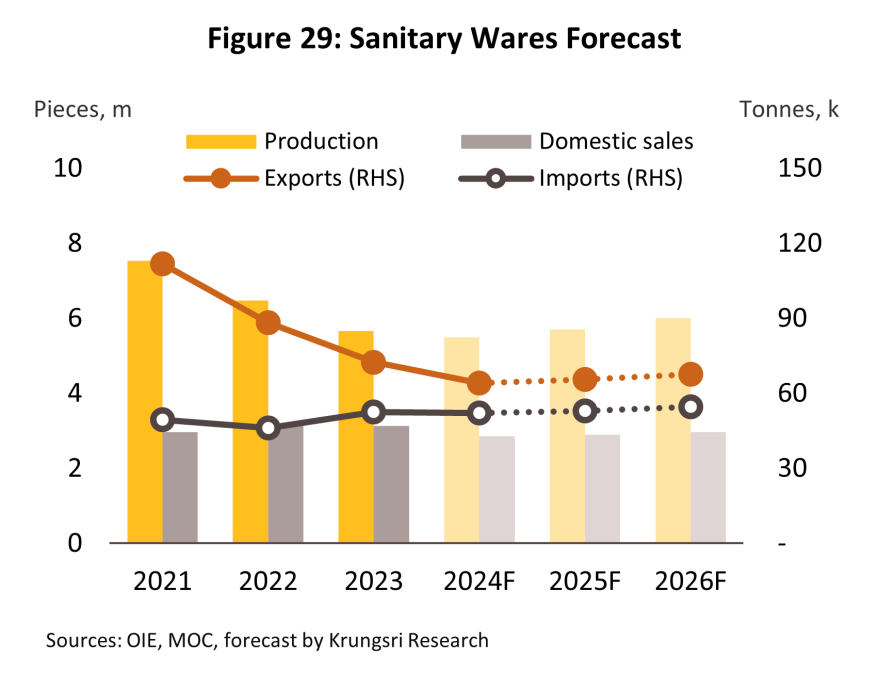
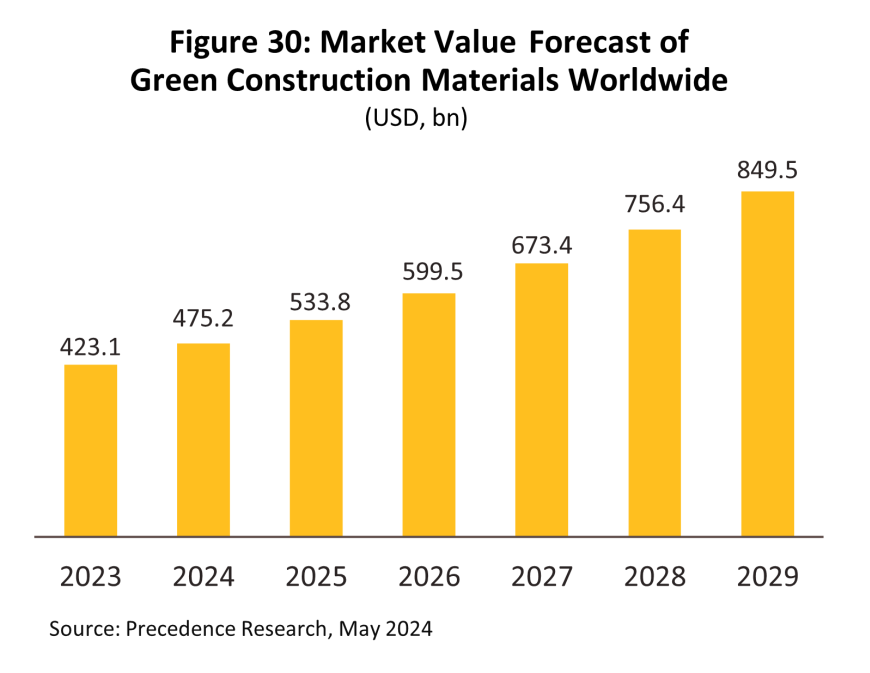
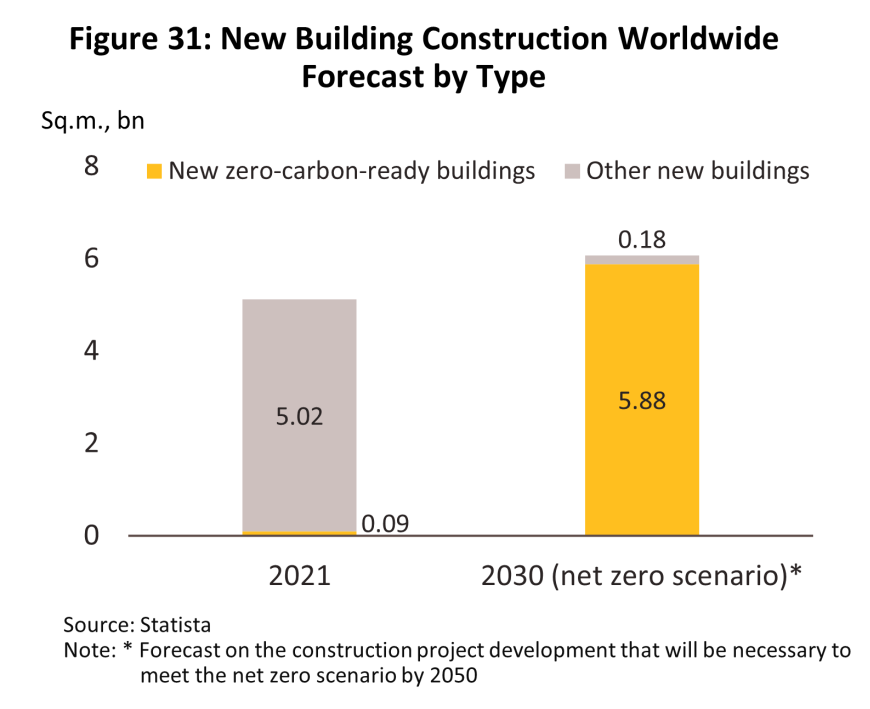
-
Over 2024 to 2026, several factors will help to keep construction material prices flat or push these up only slightly (Figure 32). (i) Having remained depressed in 2023-2024, greater public-sector spending on construction work will help to lift demand through 2025 and 2026. In addition, the post-COVID rebound in the business environment is supporting an increase in spending on infrastructure worldwide, and this is buoying demand for construction steel, even as major Chinese manufacturers are trimming output in the face of the as-yet unresolved crisis in the Chinese real estate sector. (ii) Companies will need to increase spending on the technologies and innovations needed to reduce the environmental impacts of their manufacturing processes. (iii) Geopolitical tensions will likely remain prolonged, and this will keep energy prices elevated, with knock-on effects for transportation costs. Nevertheless, overall price rises will be limited by only weak growth in domestic purchasing power, though this is particularly a problem for provincial markets, where the impacts of high household debt and tighter credit conditions are more pronounced. In addition, the cost of some inputs may fall. This should include prices for scrap and iron ore, which in the latter case the World Bank sees declining by -8.8% in 2024 and then by another -4.5% in 2025 (World Bank, April 2024).
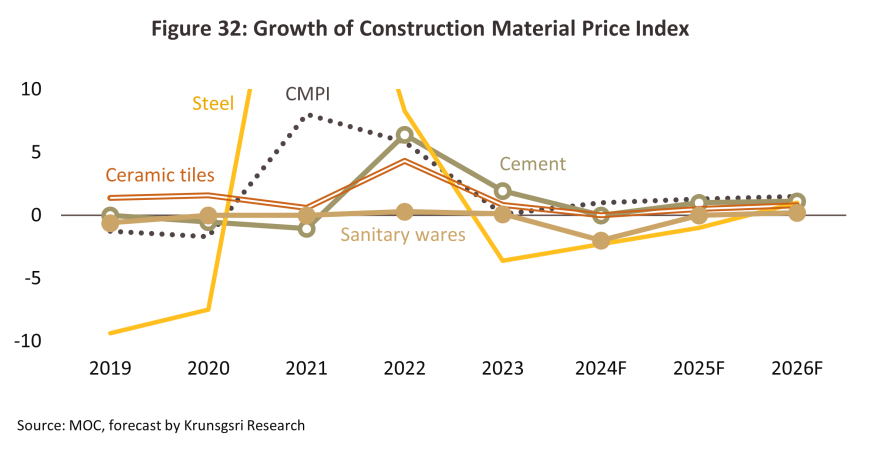
1/ This includes only companies that have submitted complete accounts for the years 2018-2023.
2/ Portland cement and mixed cement
3/ The move by Thai producers to establish production facilities overseas and then to reimport from there to Thailand has led to a large amount in the import figures.
4/ Exports are largely of cement, construction steel, ceramic tile, and sanitary ware.
5/ Exports are largely of cement, construction steel, ceramic tile, and sanitary ware.
Materials that are used in place of clinker include limestone (Thailand’s ample supplies of high-quality limestone mean that this is a common domestic option), lime, fly ash, pozzolan (e.g., silica fume, rice husk, and kaolin), and slag sourced from blast furnaces.
6/ A 100-rai pilot project has been initiated within the Saraburi Sandbox (Thailand’s first low-carbon city) to use Napier/elephant grass in cement production. This has the advantage of rapidly absorbing atmospheric carbon and also of providing a source of animal feed (Thai Cement Manufacturers Association, February 2024).
7/ The major greenhouse gases are: carbon dioxide (CO2), methane (CH4), nitrous oxide (N2O), and fluorinated gases, including the hydrofluorocarbons (HFCs), sulfur hexafluoride (SF6), perfluorochemicals (PFCs), nitrogen trifluoride (NF3), and the chlorofluorocarbons (CFCs).