The phenomenon of global warming, resulting from the substantial release of greenhouse gases into the Earth's atmosphere, has prompted countries worldwide to establish agreements for planning to reduce greenhouse gas emissions. This is achieved through setting targets to achieve carbon neutrality and net zero emissions1/, aiming to halt or slow down the escalating impacts of global warming.
To achieve the net zero goals, the petrochemical industry will therefore need to develop comprehensive plans for reducing carbon dioxide emissions throughout its supply chains. However, due to the inherent structure of the petrochemical industry, heavily reliant on fossil fuels as raw materials, carbon is often embedded in products. This results in carbon dioxide emissions not being limited solely to the energy-intensive production phase but also encompassing emissions throughout the entire life cycle, including the usage and end-of-life disposal of petrochemical products. This poses a challenge for both industry players and government bodies to collaborate in reducing carbon dioxide emissions across the entire product life cycle of the petrochemical industry.
Possible pathways to decarbonization for the petrochemical industry
As petrochemical products entail carbon emissions throughout their life cycle, addressing the challenge of decarbonizing the industry will necessitate not only continued development of ways to improve energy efficiency but also the integration of a broad range of additional technologies. A comprehensive approach to achieving these goals will depend on: (i) deploying carbon capture, utilization, and storage (CCUS) technologies; (ii) using biomass-based feedstocks; (iii) incorporating green hydrogen as an additional feedstock; and (iv) more widespread adoption of principles related to the 'circular economy'.
I.Carbon capture, utilization and storage (CCUS) technologies
‘Carbon capture, utilization, and storage' encompass a suite of technologies designed to reduce carbon dioxide emissions at the source or capture it directly from the atmosphere. This is achieved by separating carbon dioxide from other gases present in the atmosphere, either through point-source capture—removing carbon dioxide from exhaust gases produced at an industrial facility (such as a petrochemical plant)—or through direct air capture4/, extracting it from the atmosphere after those exhaust gases have already been released. After the gas has been captured by either means, it is compressed and transported by pipeline to sites where it will either be utilized in a commercial process or stored in some type of geological facility (Figure 5).
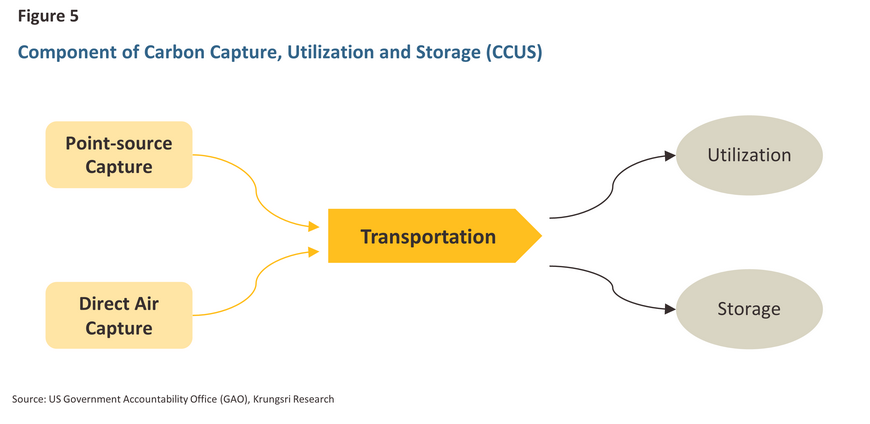
The industrial processes at the core of the petrochemical industry typically require high temperatures, usually achieved through the combustion of fossil fuels. Fossil fuel burning constitutes approximately two-thirds of all carbon dioxide emissions generated during petrochemical production, with the remaining emissions resulting from the chemical reactions that occur during these processes. On a global scale, emissions from petrochemical production reach around 1.1 gigatonnes annually, accounting for almost half of all direct carbon dioxide emissions from the industrial sector.
The application of CCUS technologies to the industry would therefore involve capturing carbon dioxide emissions from the waste gases produced on-site. This captured gas would then be piped to a second site where, if possible, it could be utilized in commercial processes to generate value; if not, it would be prepared for secure subsurface storage. In theory, by 2050, CCUS could be employed to capture around three-quarters of emissions from fossil fuel combustion. These technologies, therefore, have significant potential to make substantial progress towards the decarbonization of the industry.
Key advantages of this pathway:
-
It is possible to integrate CCUS with the industry's existing technologies and infrastructure, and its implementation would not necessitate substantial overhauls of manufacturing processes. In this regard, CCUS differs from alternative pathways and technologies, such as transitioning to the use of green hydrogen, which would require the development of entirely new supply chains.
-
CCUS may be deployed alongside other pathways and technologies, including the use of biomass feedstocks and the adoption of the circular economy. This enhances the potential and broadens the scope of reducing carbon dioxide emissions across industrial supply chains, extending beyond the sole focus on the petrochemical production process. For instance, it could be applied during the process of converting plastic waste into energy (Waste to Energy), further aiding in the reduction of carbon dioxide emissions from petrochemical products.
Challenges hindering widespread adoption: Despite its considerable potential for reducing carbon dioxide emissions, there are currently only approximately 20 commercial large-scale carbon capture and storage facilities operating worldwide, processing about 50 million tonnes of carbon dioxide annually. In contrast, the CCS Institute estimates that meeting global net zero goals will require more than 2,000 large-scale facilities.
One of the most significant obstacles to be overcome before CCUS can achieve widespread adoption involves successfully making the business case for investment. Developing CCUS facilities requires investment in long-lived assets. In addition to the technology required for capturing carbon dioxide from the air, companies will also need to heavily invest in developing other physical infrastructure, including the necessary transport pipelines and geological storage facilities where captured emissions will be pumped. Building out this network will necessitate significant financial investments and have extended construction timelines, posing a crucial financial challenge for businesses venturing into the widespread application of CCUS technology.
The applications of carbon capture and utilization technologies are currently limited, as are the associated profits. The industry is largely restricted to use cases involving the employment of captured carbon dioxide in a non-converted form, particularly by the oil and gas industry, where it is utilized in enhanced oil recovery (EOR). This process entails injecting gases into existing fields to improve extraction rates, with the added advantage that the gases used will then be sequestered. Approximately 70% of the currently captured carbon dioxide is utilized in EOR (Figure 6).
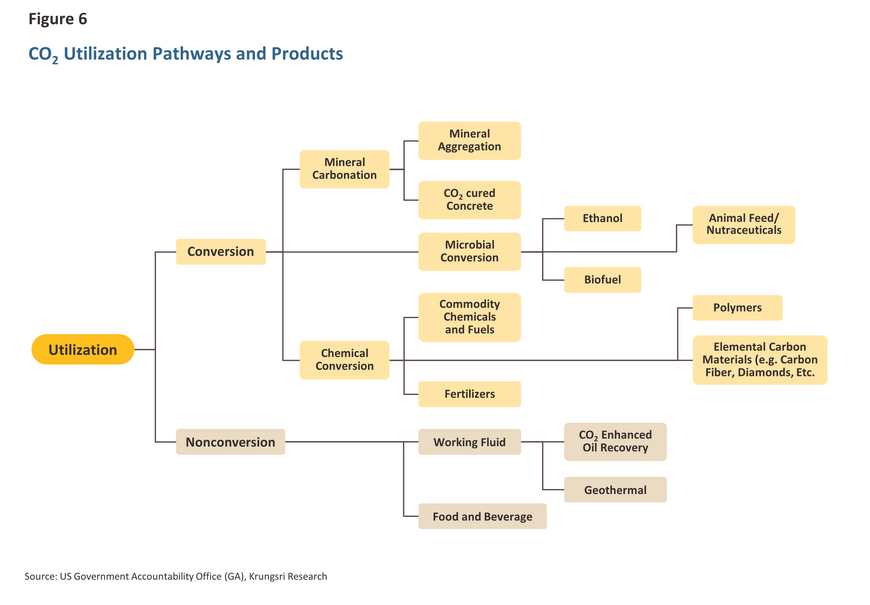
In practice, the use of carbon dioxide captured from the petrochemical industry therefore tends to be confined to related sectors of the economy, such as petroleum extraction. A notable example is the Chinese Qilu Petrochemical-Shengli Oilfield CCUS, which integrates the petrochemical industry, oil extraction, and carbon capture technology. The Qilu production facilities employ carbon capture technologies to extract carbon dioxide from emissions, subsequently utilized in the Shengli oilfield to enhance extraction rates.
The combination of high upfront investment costs and limited applications poses a major obstacle to the broader adoption of CCUS technologies by petrochemical producers.
Opportunities: A key factor that could significantly boost the widespread use of CCUS technologies is the conversion of captured carbon dioxide into various valuable products, a pathway that is currently not widely explored. With a very low proportion of carbon dioxide utilization at present, there is significant potential for growth. Lux Research estimates that the market value of CO2-based products will surge from their current value of around USD 1 billion to a total of USD 70 billion by 2030, translating into a compound annual growth rate of 53%. Products derived from carbon dioxide fall into four main categories: (i) synthetic mineral aggregates, such as chalk and limestone; (ii) CO2-cured concrete, which uses water rather than carbon dioxide as the curing agent; (iii) commodity chemicals and fuels; and (iv) polymers such as plastics and synthetic rubbers (large-chain molecules produced from monomers)5/. For the petrochemical industry, captured carbon dioxide in petrochemical production is a crucial feedstock for manufacturing petrochemical products, such as methanol and ethylene, through the green hydrogen pathway (described below).
II.Switching to biomass feedstocks
This approach involves using various types of biomass as feedstocks to replace fossil fuels in the production of petrochemical products. For example, the production of bio-polyethylene plastics (Bio-PE) can be based on (i) food crops such as sugarcane, corn, and cassava, or (ii) lignocellulose derived from agricultural residues like rice straw, bagasse, or grass. These materials can then undergo biological processes in a biorefinery for conversion into bioethanol, which may subsequently be used as an input into the production of bio-polyethylene plastics in a petrochemical plant.
Using biomass feedstocks in petrochemical production processes has the potential to help reduce carbon dioxide emissions. Plants used as raw materials can absorb carbon dioxide from the atmosphere during their growth, and the carbon dioxide is then sequestered in the petrochemical products throughout their life cycle. After their use, through processes like incineration or landfill, the released carbon dioxide is offset by the absorption from the plants used as raw materials, returning to the cycle as biogenic carbon. This differs from current petrochemical production, which relies on fossil fuels like naphtha and lacks this mechanism, resulting in the continuous release of new carbon dioxide into the atmosphere (Figure 7).
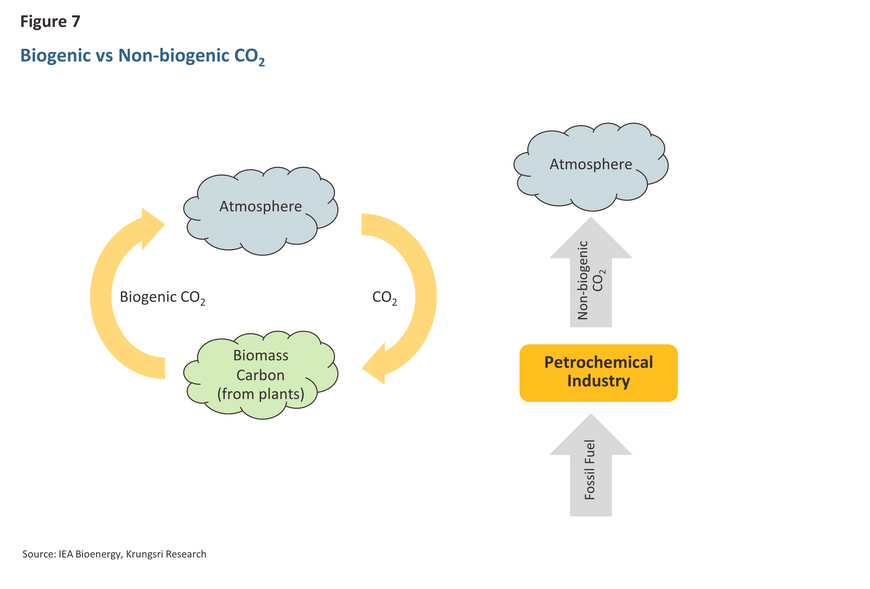
Key advantages of this pathway: There are two primary benefits to using biomass feedstocks.
-
Producers can switch to the use of biomass feedstocks while also adopting complementary technologies. For example, CCUS technologies could be employed to capture and sequester carbon dioxide released during the combustion of biomass or biomass-derived fuels. This process is referred to as 'bioenergy with carbon capture and storage' or BECCS6/, which is essentially a subset of the general category of technologies and processes grouped together under the heading of CCUS. Unlike the use of biomass feedstocks, which stabilizes the release of atmospheric carbon, BECCS reduces the total concentration of atmospheric carbon dioxide, so deploying these two processes in tandem has the potential to dramatically increase the impact of decarbonization efforts (Figure 8).
-
Using BECCS in this context may be more cost-effective than deploying the technology elsewhere in the economy. In particular, incorporating BECCS into bioethanol production could prove highly cost-effective, as the waste gases generated during the ethanol manufacturing process have a high carbon dioxide concentration compared to other processes used in, for example, the iron and steel, cement, and electricity generation sectors, making per-unit costs relatively low.
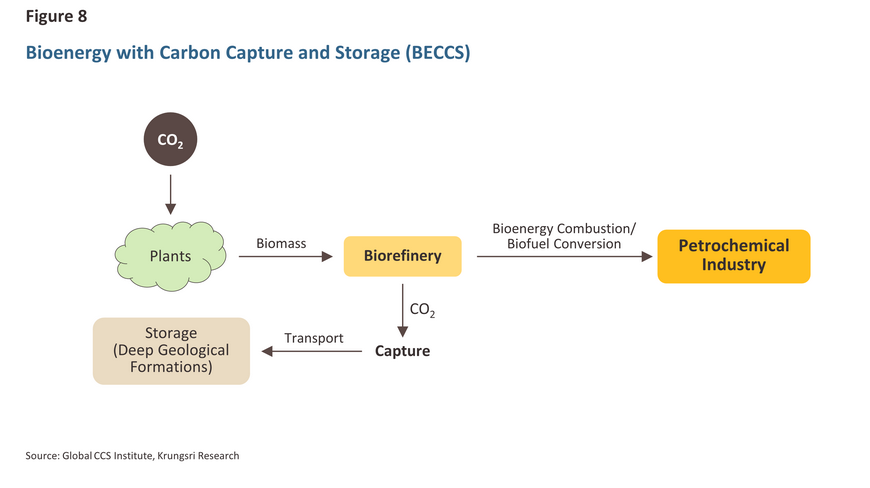
Challenges hindering widespread adoption: Currently, bioplastics represent just 2% of all plastics production, amounting to around 2.2 million tonnes annually (as of 2022). However, to meet net zero commitments, bioplastics production will need to expand to approximately 20% of output by 2050, requiring about 1.2 billion tonnes of biomass annually—roughly equal to the total current bioenergy production capacity of the United States. This expansion will undoubtedly strain supplies, raising concerns about the availability of sustainable biomass feedstocks. Furthermore, for the petrochemical industry to successfully transition to a much greater reliance on biomass and bioplastics, it must navigate intense competition for inputs from other industries that also plan to increase their consumption of agricultural crops for the production of food and biofuels. This includes the transport and power sectors, as well as other manufacturing industries aiming to use biofuels as an energy source. As the global population grows and environmental concerns intensify, these challenges are likely to worsen. It may well be the case that available biomass inputs are insufficient to meet plans for their use in reducing greenhouse gas emissions.
Opportunities: Bioplastics exhibit very similar chemical properties to the fossil fuel-derived plastics currently manufactured by petrochemical producers. Consequently, the latter can readily be substituted with the former in numerous downstream industries (see Figure 9). The markets for biomass feedstocks and bioplastics hold substantial growth potential, especially considering their current modest 2% share of overall output. Braskem, a major player in the international petrochemical market, has indicated that in the future, the supply of biomass may be redirected from bioplastics production to other sectors of the economy. While this shift might impact growth at some point down the line, its effects are unlikely to be felt for several years. In the present business landscape, the use of biomass feedstocks remains a promising pathway for reducing greenhouse gas emissions in the industry.
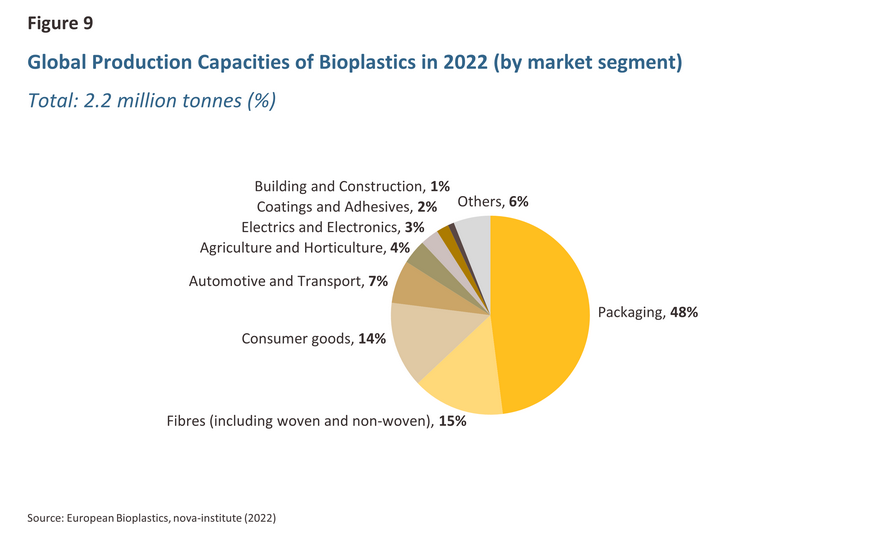
III.Using green hydrogen as a feedstock
Similar to biomass, green or renewable hydrogen can serve as an alternative to fossil fuels as a feedstock in petrochemical production. Green hydrogen is generated through renewable-powered electrolysis of water, where solar- or wind-generated electricity is utilized to separate hydrogen and oxygen atoms in water7/. This process is entirely carbon-free, both in terms of the energy used and the process outputs. This distinguishes it from most current hydrogen production methods, which involve splitting carbon and hydrogen atoms in natural gas. In such processes, hydrogen is the primary product, and carbon dioxide is produced as a by-product, often released into the atmosphere, earning it the designation of grey hydrogen (Figure 10).
Green hydrogen, generated through electrolysis, can be utilized as a feedstock in conjunction with a carbon source for the production of petrochemicals, particularly olefins like ethylene and propylene. This application is realized through two main processes: (i) methanol-to-olefin (MTO) processes, which involve utilizing green hydrogen-based methanol instead of methanol produced from grey hydrogen, and (ii) the production of synthetic naphtha using green hydrogen and carbon, as opposed to fossil fuel-derived naphtha.
As evident, the production of green hydrogen is entirely carbon-free in its core processes, ensuring no atmospheric carbon dioxide is released during its manufacture. Additionally, green hydrogen can be effectively utilized with carbon captured through CCUS technologies, providing a third major pathway to achieve substantial levels of decarbonization within the industry.
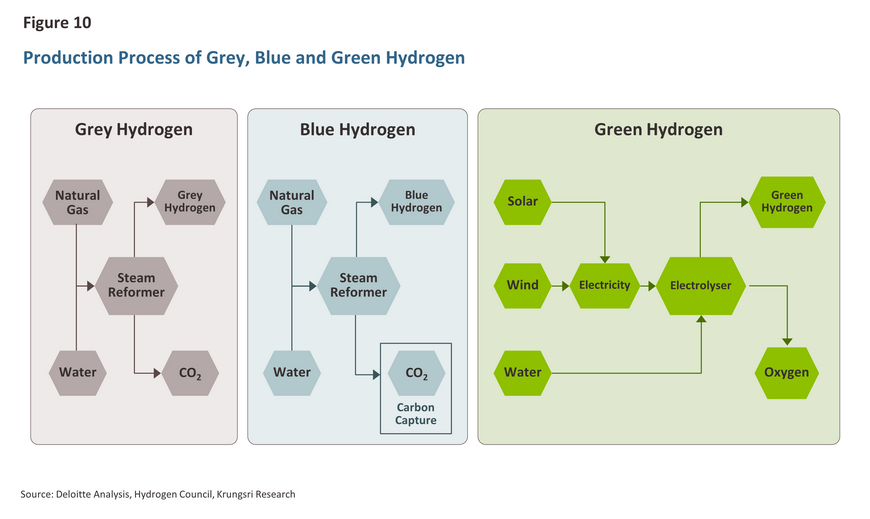
Key advantages of this pathway: Similar to the transition to biomass inputs, incorporating green hydrogen as a feedstock doesn't exclude the use of other decarbonization technologies. Notably, the integration of green hydrogen aligns seamlessly with the implementation of CCUS technologies. This enables manufacturers to capture carbon dioxide emissions and subsequently recycle this carbon as a feedstock in conjunction with green hydrogen. In the event of widespread adoption of green hydrogen by the industry, the supply of carbon from the industry's own CCUS facilities might be insufficient to meet demand. However, this scenario could expedite the adoption of CCUS technologies in other industries and stimulate the growth of carbon markets.
Challenges hindering widespread adoption: There are two main obstacles in the way to wider adoption of green hydrogen technologies.
-
Green hydrogen currently faces a significant cost challenge compared to grey hydrogen. The production cost of green hydrogen ranges from USD 3-8/kg, whereas grey hydrogen costs only USD 0.5-1.7/kg. This makes green hydrogen 2-7 times more expensive than its less environmentally friendly counterpart. The substantial cost difference presents a formidable hurdle for green hydrogen to compete effectively with natural gas-derived hydrogen in the current market landscape.
-
It will take some time for green hydrogen to gain a competitive edge, as a substantial portion (50-90%) of its production costs is associated with the price of renewables-based electricity used in the electrolytic process. Solar photovoltaic power (solar PV) is one of the most prevalent sources of renewable energy, particularly in regions with high solar insolation, like the Middle East. According to net zero emissions scenario planning by the International Energy Agency (IEA), declining prices for solar PV and electrolysers (machinery for hydrogen production) will result in the cost of solar power dropping to USD 17/MWh for Middle East production sites by 2030. This reduction will bring the manufacturing cost of green hydrogen below USD 1.5/kg H2, approaching the cost of producing hydrogen from natural gas with carbon capture and utilization (known as 'blue hydrogen'). Furthermore, if solar power costs continue to follow projections and decrease to USD 12/MWh by 2050, the production costs for green hydrogen will reach USD 1/kg H2, making it fully competitive with grey hydrogen.
In consideration of the aforementioned factors, it is evident that green hydrogen's cost competitiveness with grey hydrogen is expected to take over two decades to materialize. This poses a substantial impediment to the widespread adoption of green hydrogen as a means of decarbonizing the industry and advancing toward the net zero goals. The challenge is particularly noteworthy for producers situated in regions with constrained potential for generating electricity from solar power.
Opportunities: Deloitte anticipates a significant expansion in the green hydrogen market, projecting its value to surge from USD 160 billion in 2022 to USD 1.4 trillion by 2050. This implies a compound annual growth rate of 8.1%. This growth trajectory presents lucrative opportunities for players in the petrochemical industry to enter the green hydrogen production sector. The produced green hydrogen can be utilized internally within the petrochemical industry and also sold as a fuel to companies in the iron and steel, cement, and transport sectors. These companies, in turn, can integrate green hydrogen into their strategies for achieving net zero emissions.
Despite the optimistic projections for the green hydrogen market, Bain and Company foresee significant growth being realized only after 2030, aligning with the expected timeline for achieving price competitiveness. In the early stages of market development, players are likely to collaborate in forming hydrogen project consortiums. Consortium members will bring expertise in clean energy, infrastructure, green energy production, hydrogen storage and transportation, and commercial applications of hydrogen. Currently, several green energy projects involve players from the oil and gas sector functioning as both project developers and offtakers. This dual role is anticipated to play a vital role in shaping and reinforcing green hydrogen supply chains (Figure 11).
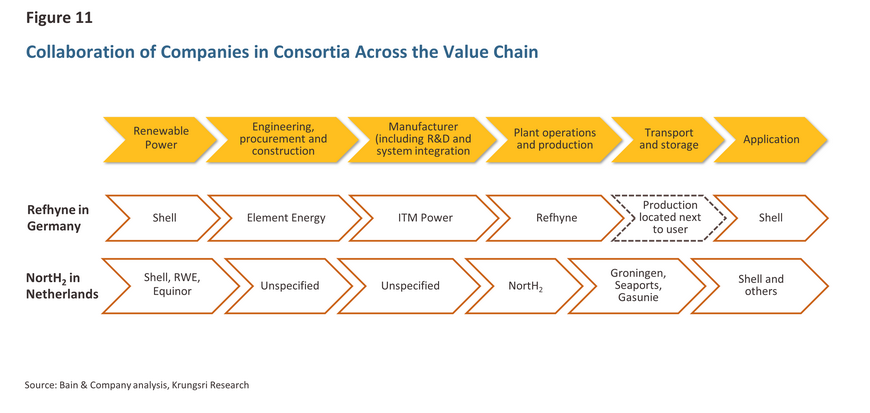
Looking ahead, supply chains are likely to witness some consolidation as businesses pursue both forward and backward integration. Petrochemical industry players in downstream positions currently serve as offtakers, but as their proficiency in utilizing green hydrogen advances, there is a likelihood that they will seek to expand upstream into the production of green hydrogen and electrolysers. This expansion would offer them more extensive market opportunities, increased profitability, and greater control over their access to feedstocks.
IV. Adoption of the circular economy principles
The concept of the circular economy is founded on four key principles: (i) demand reduction; (ii) reuse; (iii) recycling; and (iv) energy recovery. In essence, the circular economy seeks to 'close the loop' in consumption and production. An overview of how these principles are applicable to the petrochemical industry is provided below (Figure 12).
-
Demand reduction: This trend is expected to escalate as governments in numerous countries increasingly tighten regulations on the production and utilization of plastics. The focus has been particularly on single-use plastics, notably plastic bags, with a combination of public campaigns and incentives aimed at promoting increased reuse and recycling of these materials.
-
Reuse: In some cases, used plastic products can undergo a process called 'remanufacturing,' where they are reconditioned and restored to a state similar to that of a new product. Plastic items that have not been reused will turn into waste, but a portion of this waste can be collected, and some of it may be suitable for reuse.
-
Recycling: There are two types of recycling applicable to plastics: (i) Mechanical recycling involves the collection of used plastic, separating and sorting it by type, cleaning it, finely chopping the waste, and melting it into recycled nurdles that can be used in place of virgin plastic to produce new plastic products. (ii) Chemical recycling involves changing the chemical structure of the recycled plastic and converting it back into an upstream product such as a monomer, naphtha, or synthetic crude oil. The resulting raw materials obtained from this process often have quality similar to new ones.
-
Energy recovery: In the context of the petrochemical industry, this may involve using plastic that has not or that cannot be recycled as a source of energy (i.e., to provide heat, electricity, or fuel). This might be done through incineration, gasification or landfill gas recovery.
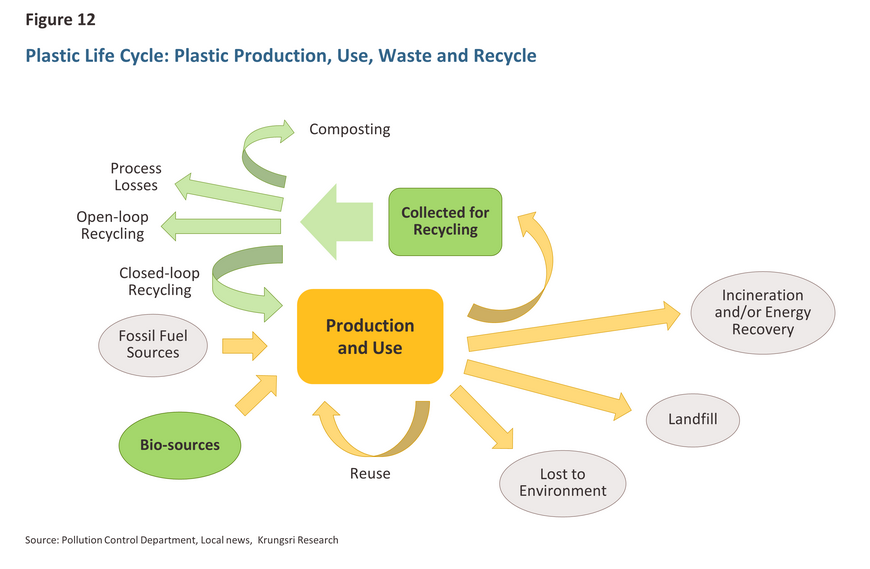
Implementing the first three of these methods will help reduce the production of petrochemicals derived from fossil fuels. Furthermore, recycling typically requires less energy than manufacturing petrochemicals from fossil fuels. As a result, this approach can lead to a 50% reduction in energy consumption and inputs compared to producing plastics from new feedstocks.
In addition, applying energy recovery principles to the management of plastic waste can improve its efficiency. Currently, waste plastic that cannot be reused or recycled is either burned (constituting around 25% of plastic waste) or disposed of in landfills (accounting for an additional 40% of the total). If these two methods are not properly managed, it will unavoidably result in increased carbon emissions. Therefore, implementing well-managed waste-to-energy schemes can help alleviate these problems. However, generating power from waste plastic will still release carbon dioxide into the atmosphere, similar to its production. To achieve the necessary emissions cuts throughout supply chains mandated by the adoption of net zero goals, waste-to-energy schemes should be coupled with the use of CCUS technologies.
Key advantages of this pathway: The increased recycling of plastics can be implemented alongside the shift to the production of bioplastics. This is because bio-based polyethylene terephthalate (bio-PET) and bio-based high-density polyethylene (bio-HDPE) share similar chemical properties with regular PET and HDPE produced from fossil fuel feedstocks. Consequently, these bio-based plastics can be recycled in the same facilities, creating a synergy that accelerates the impact of decarbonization efforts across both pathways.
Challenges hindering widespread adoption: One major challenge in adopting the principles of the circular economy is that, currently, only around 9% of all plastic is recycled. To meet the net zero goals, this recycling rate needs to increase five-fold to around 50%.
At present, more than 80 retailers and packaging material manufacturers have outlined plans to boost the use of recycled plastics in product containers and packaging, with targets ranging from 15% to 50% of the total. Governments worldwide have also taken action by implementing measures to promote plastic recycling. These measures include: (i) restrictions or bans on single-use plastics; (ii) extended producer responsibilities; and (iii) requirements for recycled content (Table 1).
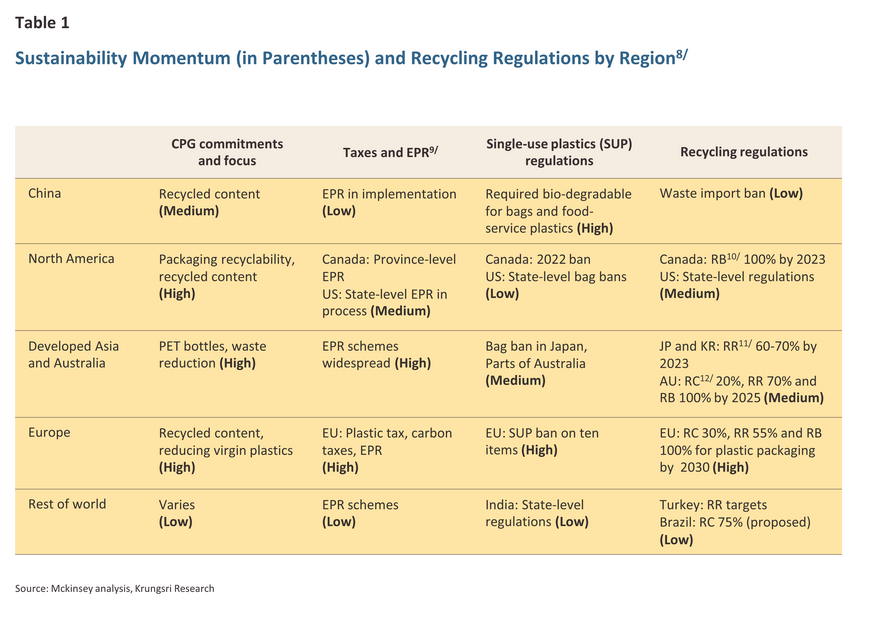
Unfortunately, the current low rate of plastics recycling means that the quantity of used plastic available for recycling processes is severely limited. As a result, the supply of recycled plastics is growing at an equally slow pace. Furthermore, with increasing consumer concerns about the environment and governments promoting measures aligned with the circular economy to reduce plastic waste, the supply is likely to be insufficient to meet the anticipated growth in demand.
The severity of this problem is underscored by research from the US, which shows that between 2012 and 2022, the supply of recycled polyethylene terephthalate (rPET) in the US expanded by 1% per year. However, over the same period, demand accelerated by 4% annually. Management consultants McKinsey also predict that if retailers and manufacturers of packaging can achieve their set targets for the use of recycled plastics by 2030, demand for rPET will expand by 15% over 2022-2030, while supply will have inched up by just 1%. By 2030, demand will, therefore, outstrip supply three times over, clearly representing a major roadblock on the way to implementing the circular economy principles as a means of helping the petrochemical industry reach net zero.
Opportunities: Over the past two decades, 44% of the gains in profitability recorded by the petrochemical industry have originated from feedstock advantages. If widespread recycling methods are employed and plastic waste can become a new source of feedstock advantage, this would contribute significantly to the profitability of the petrochemical and plastic industries, projected to constitute two-thirds of the expected overall increased profits between 2018 and 2030.
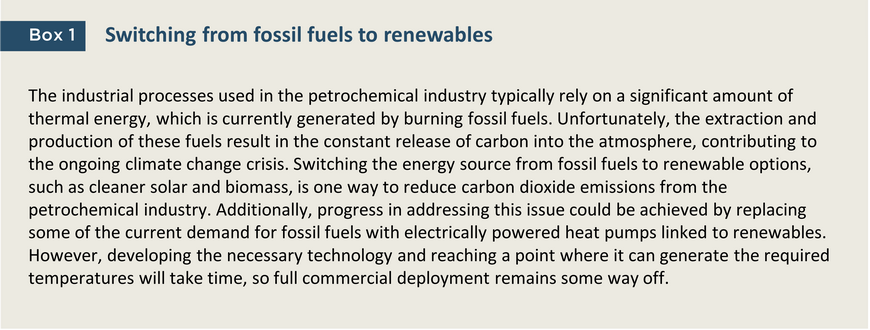
The impacts of net zero targets on the Thai petrochemical industry
Progress on meeting net zero goals
At present, the adoption of the four pathways and technologies described above by the Thai petrochemical industry remains limited, mirroring the global situation. As a result, enhancing energy efficiency remains a primary avenue for reducing carbon dioxide emissions. However, this situation is complicated by efforts to address carbon leakage in export markets—a form of regulatory arbitrage where manufacturers in countries with stringent carbon emission regulations may relocate to jurisdictions with laxer regulations. Alternatively, carbon leakage may involve companies based in countries with strict emission controls sourcing imports from manufacturers in regions with more relaxed regulatory frameworks. To counter the risks associated with unchecked offshoring, countries are implementing carbon border adjustment mechanisms (CBAMs)13/. These mechanisms function as taxes on imports calculated based on the carbon emissions associated with the production of those goods. The introduction of CBAMs indicates a tightening regulatory environment in export markets. Therefore, it is now imperative for players in the Thai petrochemical industry to respond by accelerating the adoption of these four strategies. This not only helps the industry reduce exposure to risk but also expedites its transition to net zero.
Technologies and pathways leading to net zero in Thailand
Of the four strategies discussed above, CCUS will play a crucial role in achieving net zero goals. This judgement is based on a consideration of three factors.
-
Technological readiness level (TRL)14/: CCUS is regarded as a mature technology, and this is ranked between 7 and 9 on the technological readiness scale. This maturity places CCUS in a prime position for full-scale commercial deployment, seamlessly integrating with existing infrastructure within the petrochemical industry.
-
Mitigation costs: CCUS is cheaper than alternative technologies and pathways, even though upfront investment costs can be considerable. The mitigation costs for CCUS typically range from USD 0-150 per tonne of CO2, while the cost associated with other technologies and pathways can rise higher, reaching USD 300-400 per tonne of CO2.
-
Ease of implementation: CCUS technologies can seamlessly integrate into the existing technology and infrastructure of the petrochemical industry without causing significant disruptions. In contrast to other pathways and technologies under consideration, the adoption of CCUS differs, as it avoids the need for overhauling production lines and developing entirely new supply chains.
Due to the supporting factors mentioned earlier, the IEA expects that CCUS will play the most crucial role in reducing carbon emissions from the industry. Therefore, this set of technologies should account for approximately 35% of the cumulative cuts to carbon dioxide emissions made by the industry from 2017 to 2050. Additional emission reductions, around 25% each, will be achieved through improvements in energy efficiency and the transition from coal to natural gas as a feedstock. The use of gas and naphtha as energy sources and feedstocks, instead of coal, results in lower carbon emissions. The remaining three pathways/technologies—green hydrogen, using biomass as a feedstock, and adopting the principles of the circular economy—will contribute to the remaining declines in carbon dioxide emissions, collectively representing around 15% of the total reduction.
Despite the IEA forecasts, the shift from replacing coal with natural gas as the primary feedstock within Thailand will likely have a limited impact on carbon dioxide emissions. This is because the domestic industry is already predominantly reliant on natural gas and naphtha, leaving little room for additional gains. In contrast, China, the world’s leading producer of petrochemicals, faces a different scenario. Given that its production is more heavily oriented towards the use of coal as a feedstock, especially in the manufacturing of methanol and ammonia, a widespread transition from coal to natural gas could yield significant overall impacts on carbon dioxide emissions. Given the constrained potential of natural gas as a bridge to lower emissions in Thailand, the four pathways and technologies described above will play a central role in helping the Thai petrochemical industry achieve its net zero goals.
At the global level and specifically within the Thai context, CCUS emerges as the most promising among the discussed technologies and strategies. Considering the three factors outlined earlier, CCUS stands out as the pathway most ready for immediate deployment. Given that transitioning feedstocks from coal to natural gas may not be a feasible option in Thailand, CCUS is likely to play a central role in the country's petrochemical industry, driving its efforts towards achieving net zero goals. CCUS is anticipated to contribute significantly to emission reduction by addressing both the conversion of fossil fuels into petrochemicals as well as being used alongside other emission reductions pathways, including the use of biomass-based feedstocks, green and blue hydrogen, and plastic-waste-to-energy schemes.
Regarding the other three technologies that entail the establishment of new supply chains, the use of biomass as a feedstock has the potential to become widespread within the Thai industry thanks to the strength of the domestic market on both the demand and supply sides.
- Supply: Thailand is already an important producer of the agricultural crops used as inputs into the production of bioplastics. For example, the country produces 35 million tonnes of cassava annually, or 9.6% of global yields, and with a 1.5% share of global production, the country’s bio-ethanol industry is the world’s seventh largest.
- Demand: Thailand is the world’s second most important manufacturer of bioplastics, and with production capacity that comes to 95,000 tonnes per year, the Thai industry is beaten on size only by the US’s annual capacity of 150,000 tonnes. Demand for biomass feedstocks will be further strengthened by the partnership between, Braskem and Thailand’s petrochemical players, which have launched a joint venture to manufacture bio-ethylene and bio-polyethylene.
Going forward, if output of bioplastics continues to rise, this will lift demand for biomass inputs and for bio-ethanol. At the same time, demand from the transport sector for bio-ethanol for the production of gasohol will also rise, as will that for food crops such as sugarcane and cassava that are used for consumption as food or for processing into other products. Given this increased pressure on the consumption side of the market, the price of the inputs used in the manufacture of bioplastics will climb, and this may make it difficult for players to source sufficient inputs for the industry to meet its net zero goals.
Nevertheless, raw materials like lignocellulosic biomass, such as rice straw, sugarcane bagasse, corncobs, and grasses, will play an increasingly crucial role in bioethanol production in the future. This is because they are agricultural residues that can help reduce the use of food crops and agricultural land in bioethanol production, mitigating the risk of raw material shortages for future bioplastic production. As a result, the adoption of biomass feedstocks becomes a more stable tool for reducing the carbon footprint of the Thai petrochemical industry.
Within the Thai context, green hydrogen is expected to play a less prominent role in the petrochemical industry compared to some other countries, where renewables are more easily and affordably produced. As mentioned earlier, the current production cost of green hydrogen is notably higher than that of grey hydrogen, making the latter more cost-competitive. However, the cost of electricity from renewables is gradually decreasing, which will eventually lower the overall cost of green hydrogen. Specifically, green hydrogen generated using solar power tends to be more cost-effective than other renewable sources. In regions with optimal conditions for solar power generation, such as the Middle East, Chile, Australia, and parts of China, it is projected that green hydrogen produced from solar energy might become competitively priced compared to grey hydrogen around 2050. Therefore, the expectation is that locally produced green hydrogen in Thailand, which has less solar energy production potential than the aforementioned countries, will not play a major role in facilitating the Thai petrochemical industry's transition to net zero in the short term. This may only change in the long term as production costs decrease significantly. On the other hand, blue hydrogen could have a more significant role since its production costs are only slightly higher than those for grey hydrogen, making it a viable option for those aiming to reduce corporate environmental impacts.
However, instead of relying on solar-produced green hydrogen, the production of hydrogen from biomass presents a more realistic path for the Thai industry since the country possesses competitive advantages in biomass production and related supply chains. Furthermore, the technology required for biomass-based production of green hydrogen is already considered mature, raising the strong possibility that production in this area will ramp up in the near future/15.
Finally, taking on board some of the principles of the circular economy will also play a part in helping the industry to lessen its environmental impacts and to meet its net zero goals, although fully exploiting the potential offered by this pathway will require overcoming two challenges.
- Development of the circular economy is only at its early stages in Thailand, although under the Action Plan on Plastic Waste Management Phase II (2023-2027), the government is committed to raising the standards of the national plastic waste management system. In addition to campaigns to encourage the public to reduce and eventually eliminate consumption of single-use plastics, this plan also includes implementing extended producer responsibility measures that emphasize the importance of managing packaging across its lifecycle. However, compared to progress on similar measures in the developed economies, where many retailers and manufacturers have made commitments to minimum recycled contents in packaging, Thailand’s efforts related to this issue are still in the early stages. This therefore presents an opportunity for Thailand to further develop and align its economic circularity concepts with those of other countries.
- There is a risk of a fragmented transition to the circular economy as a result of a lack of coordination at the level of industrial supply chains and with regard to the sharing of information between consumers, companies, and government agencies. This may then generate imbalances in the supply of plastic waste and recycled plastic as described above, and problems in this area would then hamper efforts to cut carbon dioxide emissions.
Structural impacts on the Thai petrochemical industry
At present, most Thai petrochemical plants are situated in the Eastern Economic Corridor (EEC), but this may change in the future. As discussed earlier, the industry is expected to more deeply embrace the four pathways outlined in this paper as companies strive to meet their net zero commitments, influencing decisions on where to locate operations. Specifically, access to low-cost inputs will become a crucial factor in future decisions on production facility locations, extending considerations to include access to renewable energy, biomass feedstocks, and locations suitable for carbon dioxide storage. This strategic shift may occur because, while it is currently feasible to transport inputs in quantity to production sites within the EEC, establishing smaller decentralized plants near input sources may be more cost-effective, enhancing the competitiveness of companies opting for this approach. This trend appears to be underway, with bio-complexes emerging outside the EEC, including locations in the central region (Nakhon Sawan) and the northeast of the country (Khon Kaen) (Figure 13). These areas attract investment due to their abundant sugarcane and cassava resources and their significance in the national ethanol industry. If, as expected, the use of biomass feedstocks becomes more widespread in the industry, bio-complexes are likely to proliferate to a broader range of locations, particularly in areas with high potential for ethanol production. This will contribute to distributing investment and income to the agricultural and labor sectors involved in upstream parts of petrochemical supply chains in these areas.

Krungsri Research view
Due to the substantial carbon dioxide emissions linked to the production and utilization of its outputs, the petrochemical industry will significantly influence Thailand's strategy in achieving its net zero goals. Anticipated trends in future demand are poised to further underscore its importance. Consequently, to meet these goals, the roles of the four pathways and technologies outlined are expected to play an increasingly substantial role, ultimately reshaping the supply chain landscape of the Thai petrochemical industry.
At present, these four pathways and their associated technologies are still in the early stages of deployment. Utilizing them in a full commercial setting to produce petrochemicals incurs higher costs compared to employing conventional methods that use fossil fuels. This, in turn, renders these products uncompetitive in the marketplace and hinders growth in demand. Given this, there is an opportunity for the government to intervene on both sides of the market. On the supply side, the government should introduce targeted measures to help environmentally friendly petrochemicals, produced using these new technologies and methodologies, become competitive in cost with fossil fuel-based alternatives. On the demand side, there is a clear role for the government in raising awareness among consumers about the importance of behavioral change and the transition to using new low-carbon products. Taking this twin-track approach will undoubtedly help each side support the other, improving the speed, efficiency, and smoothness of the low-carbon transition.
For Thai companies, adopting these pathways and technologies in a manner suitable for each individual corporation not only allows players to meet their net zero commitments but also opens the door to producing a broader range of high-value-added goods. These may include bioplastics, recycled plastics, and petrochemical products manufactured from green hydrogen. This, in turn, enables companies to explore new markets and expand their business opportunities, preventing them from being constrained to competing solely on price in the production and sale of commodity-grade products, where the competition is steadily escalating.
References
Asian Development Bank (2020) Best practice handbook: Waste to energy in the age of circular economy. Retrieved Sep 24, 2023 from https://www.adb.org/sites/default/files/institutional-document/659981/waste-energy-circular-economy-handbook.pdf
Bain and Company (2021) Business opportunities in low-carbon hydrogen. Retrieved July 25, 2023 from https://www.bain.com/insights/low-carbon-hydrogen-enr-report-2021/#
Deloitte’s 2023 Global Green Hydrogen Outlook (2023) Green hydrogen: energizing the pathway to net zero. Retrieved Sep 9, 2023 from https://www2.deloitte.com/content/dam/Deloitte/at/Documents/presse/at-deloitte-wasserstoffstudie-2023.pdf
Deloitte (2021) The potential of hydrogen for the chemical industry. Retrieved Aug 15, 2023 from https://www2.deloitte.com/content/dam/Deloitte/xe/Documents/energy-resources/me_pov-hydrogen-chemical-industry.pdf
Global CCS Institute (2019) Bioenergy and carbon capture and storage. Retrieved Aug 2, 2023 from https://www.globalccsinstitute.com/wp-content/uploads/2019/03/BECCS-Perspective_FINAL_PDF.pdf
Global CCS Institute (2020) Carbon capture and storage: Challenges, enablers and opportunities for deployment. Retrieved Aug 20, 2023 from https://www.globalccsinstitute.com/news-media/insights/carbon-capture-and-storage-challenges-enablers-and-opportunities-for-deployment/
Global CCS Institute (2019) Waste-to-Energy with CCS: A pathway to carbon-negative power generation. Retrieved Sep 3, 2023 from https://www.globalccsinstitute.com/wp-content/uploads/2019/10/Waste-to-Energy-Perspective_October-2019-5.pdf
International Energy Agency (2019) Can CO2-EOR really provide carbon-negative oil? Retrieved Oct 25, 2023 from https://www.iea.org/commentaries/can-co2-eor-really-provide-carbon-negative-oil
International Energy Agency (2023) Global hydrogen review 2023. Retrieved July 19, 2023 from https://iea.blob.core.windows.net/assets/5bd46d7b-906a-4429-abda-e9c507a62341/GlobalHydrogenReview2021.pdf
IEA-ETSAP and IRENA (2013) Technology brief: Production of Bio-ethylene. Retrieved Sep 8, 2023 from https://www.irena.org/-/media/Files/IRENA/Agency/Publication/2013/IRENA-ETSAP-Tech-Brief-I13-Production_of_Bio-ethylene.pdf?rev=e260b01daa334f97a013c23ac7f12a2e
International Energy Agency (2018) The future of petrochemicals: Towards more sustainable plastics and fertilizers. Retrieved Aug 5, 2023 from https://iea.blob.core.windows.net/assets/bee4ef3a-8876-4566-98cf-7a130c013805/The_Future_of_Petrochemicals.pdf
Lux Research, Inc. (2020) CO2 capture and utilization: The emergence of a carbon economy. Retrieved Aug 23, 2023 from http://luxresearchinc.com/wp-content/uploads/2022/07/lux-research-co2-capture-utliziation-the-emergence-of-a-carbon-economy-executive-summary.pdf
McKinsey & Company (2022) Advanced recycling: Opportunities for growth. Retrieved Aug 14, 2023 from https://www.mckinsey.com/industries/chemicals/our-insights/advanced-recycling-opportunities-for-growth
McKinsey & Company (2023) Filling the gap: Boosting supply of recycled materials for packaging. Retrieved 21 Sep, 2023 from https://www.mckinsey.com/industries/packaging-and-paper/our-insights/filling-the-gap-boosting-supply-of-recycled-materials-for-packaging
McKinsey & Company (2018) How plastics waste recycling could transform the chemical industry. Retrieved 3 Aug, 2023 from https://www.mckinsey.com/industries/chemicals/our-insights/how-plastics-waste-recycling-could-transform-the-chemical-industry
McKinsey & Company (2018) No time to waste: What plastics recycling could offer. Retrieved Aug 26, 2023 from https://www.mckinsey.com/~/media/McKinsey/Industries/Chemicals/Our%20Insights/No%20time%20to%20waste%20What%20plastics%20recycling%20could%20offer/No-time-to-waste-What-plastics-recycling-could-offer.pdf
OECD (2022) Global Plastics Outlook: Economic drivers, environmental impacts and policy options, OECD Publishing, Paris. Retrieved Oct 18, 2023 from https://doi.org/10.1787/de747aef-en
Saygin, D. & Gielen, D. (2021) Zero-emission pathway for the global chemical and petrochemical sector. Energies 2021, 14, 3772. Retrieved Oct 1, 2023 from https://doi.org/10.3390/en14133772
S&P Global Commodity Insights (2021) Bio-petrochemicals - From feedstocks to plastics: The rise of bio-based alternatives. Retrieved Aug 22, 2023 from https://www.spglobal.com/commodityinsights/en/market-insights/special-reports/chemicals/bio-petrochemicals
United States Government Accountability Office (2022) Decarbonization: Status, challenges, policy options for carbon capture, utilization, and storage. Retrieved Sep 20, 2023 from https://www.gao.gov/assets/gao-22-105274.pdf
U.S. Department of Energy (2023) Million-tonne CO2 capture, utilization and storage (CCUS): The Qilu-Shengli oilfield project. Retrieved Oct 19, 2023 from https://www.energy.gov/sites/default/files/2023-07/6b.%2020230613-Million-Tonne%20CCUS-The%20Qilu-Shengli%20Oilfield%20Project%20PDF.pdf
World Economic Forum (2022) Carbon neutral and net zero – what do they mean? Retrieved Oct 15, 2023 from https://www.weforum.org/agenda/2022/08/carbon-neutral-net-zero-sustainability-climate-change/
ห้องสมุดบรรจุภัณฑ์ ภาควิชาเทคโนโลยีการบรรจุและวัสดุ คณะอุตสาหกรรมเกษตร มหาวิทยาลัยเกษตรศาสตร์ - Packaging Library (2023) ข่าวสารบรรจุภัณฑ์ โอกาสใหม่เมืองเกษตรกรรม ไทยขึ้นแท่นฮับไบโอพลาสติก หลัง ‘Braskem’ และบริษัทระดับโลกแห่ตั้งโรงงานที่ จังหวัดระยอง
กรมควบคุมมลพิษ กระทรวงทรัพยากรธรรมชาติและสิ่งแวดล้อม (2023) แผนปฏิบัติการด้านการจัดการขยะพลาสติก ระยะที่ 2 (2023-2027)
ธนิสา ทวิชศรี (2022) Carbon neutrality กับ net zero emissions ต่างกันอย่างไร? และมีความสำคัญอย่างไร? [Pier blog post]
1/ The most important greenhouse gases are carbon dioxide (CO2), methane (CH4) and nitrous oxide (N2O), though production of petrochemicals is most closely associated with the release of carbon dioxide. In the context of this paper, references to net zero emissions will therefore principally refer to reductions in the release of carbon dioxide.
2/ For further information on carbon credits, please see: https://www.krungsri.com/th/research/research-intelligence/carbon-credit-2023
3/ For further details on the difference between net zero and carbon neutrality, please see:https://www.weforum.org/agenda/2022/08/carbon-neutral-net-zero-sustainability-climate-change/
4/ Direct air capture describes the process by which carbon dioxide is separated and removed from other atmospheric gases directly. The extracted gas can then be processed for other uses or pressurized for subsurface storage. For further details, please see: https://read.oecd-ilibrary.org/energy/direct-air-capture_bbd20707-en#page1
5/ For further details on products produced from CO2, please see: https://www.gao.gov/assets/gao-22-105274.pdf
6/ BECCS is classed as a carbon dioxide removal technology. For more details, please see:
https://www.globalccsinstitute.com/wp-content/uploads/2020/04/BIOENERGY-AND-CARBON-CAPTURE-AND-STORAGE_Perspective_New-Template.pdf
7/ Green hydrogen can also be produced through biomass gasification, which uses heat, steam and oxygen to convert biomass into hydrogen without the need for combustion. For more details, please see : https://www.etipbioenergy.eu/images/Renewable_Hydrogen_Production_from_Biomass.pdf
8/ Country Abbreviation: AU=Australia, CA=Canada, JP=Japan, KR=Korea, US=United States
9/ EPR stands for extended producer responsibilities
10/ RB stands for recyclability
11/ RR คือ Recycling rate
12/ RC คือ Recycle content
13/ For further details, please see: https://www.krungsri.com/getmedia/a1b8cb18-3238-4e46-954f-dc22fedab903/RI_CBAM_230803_TH.pdf.aspx
14/ Technological readiness levels is formally assessed on a scale from 1 (the basic principles have been observed) through to 9 (the actual system has been successfully demonstrated over the full range of expected conditions). The latter is thus the point at which the technology under discussion is considered ready for commercial use. For more details, please see: https://arena.gov.au/assets/2014/02/Technology-Readiness-Levels.pdf
15/ For more details on the production of green hydrogen from biomass, please see: https://www.energy.gov/eere/fuelcells/hydrogen-production-biomass-gasification